
iron agglomeration process

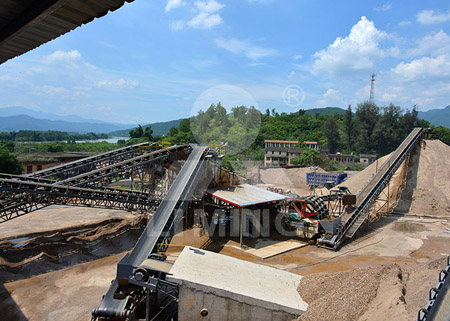
iron agglomeration process
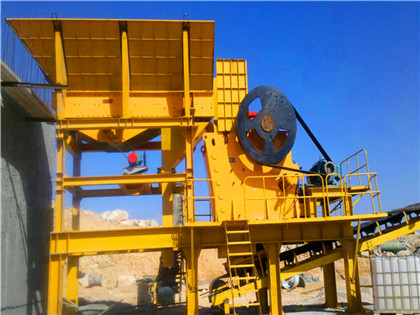
Iron Ore Sintering: Process: Mineral Processing and
Sintering is a thermal agglomeration process that is applied to a mixture of iron ore fines, recycled ironmaking products, fluxes, slagforming agents, and solid fuel (coke) The purpose of the sintering process is manufacturing a product with the suitable Pelletization is an agglomeration process of iron ore concentrates with a granulometry lower than 150 μ m and low Iron Ore Agglomeration Technologies

(PDF) Iron Ore Sintering: Process ResearchGate
Sintering is a thermal agglomeration process that is applied to a mixture of iron ore fines, recycled ironmaking products, Iron Ore Agglomeration Technologies D FernándezGonzález, J PiñuelaNoval, Luis FelipeVerdeja Published 20 December 2017 Materials Science [PDF] Iron Ore Agglomeration Technologies Semantic

Iron Ore Agglomeration Technologies
Until the 1950s of the last century, the oxidized iron ores that were loaded into the blast furnace had granulometries within 10 and The FEECO Innovation Center is equipped to suit small batch tests on a single piece of equipment, as well as a continuous process loop to create the ideal iron ore agglomeration process Items such as attrition, crush A Detailed Look at Iron Ore Agglomeration

Composite agglomeration process (CAP) for preparing
Abstract An innovative process of preparing ironmaking burden the composite agglomeration process (CAP) has been developed In CAP, part or all of the The sintering process is defined as a thermal agglomeration process (13001400 • C [17], but it does not involve the complete melting of the charge) that is applied to a mixture of Iron Ore Agglomeration Technologies [scite report]

Development of Composite Agglomeration Process of Iron
Composite agglomeration process (CAP), as an innovative method for preparing blast furnace burden, was developed and has been put into operation in China The most common agglomeration process is the sintering of fine ore As a rule, larger amounts of circulation material are used in the sintering plant This often leads to Agglomeration Iron & Steel Kuettner Group

Iron Ore Sintering: Process: Mineral Processing and
Sintering is a thermal agglomeration process that is applied to a mixture of iron ore fines, recycled ironmaking products, fluxes, slagforming agents, and solid fuel (coke) The purpose of the sintering process is manufacturing a product with the suitable characteristics (thermal, mechanical, physical and chemical) to be fed to the blast Aided by selfagglomeration, a twostage reduction process conducted at a higher temperature (600 °C) than the singlestage process resulted in an enhancement of the k constant to more than twice that of the singlestage process A force balance model coupled with the reduction kinetics of Fe 2 O 3 is first proposed to explain the self Selfagglomeration mechanism of iron nanoparticles in a
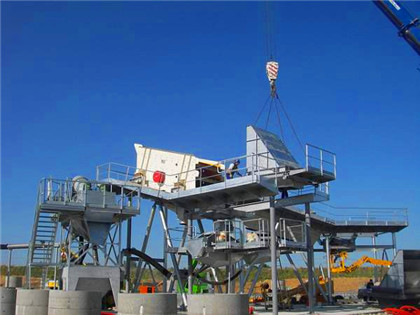
Advances in Sintering and Pellet Technology MDPI
The objective of iron ore agglomeration is to generate a suitable product of granules in terms of thermal, mechanical, physical, and chemical properties The doublelayer ignition sintering process can reduce the emission of nitrogen oxides in the sintering process under the condition of guaranteeing the quality of sinter, which has great This book focuses on agglomeration, or the size enlargement process, of iron ores This process sits at the interface of mineral processing and extractive metallurgy The book begins with a discussion of raw materials preparation and the beneficiation process It then describes fundamental principles of the sintering and pelletization Agglomeration of Iron Ores Ram Pravesh Bhagat Taylor
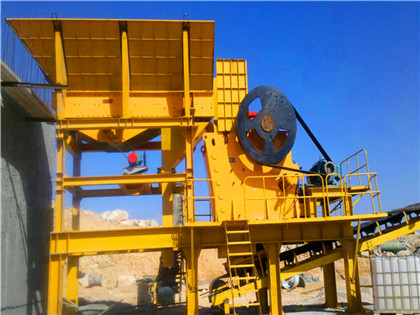
A Detailed Look at Iron Ore Agglomeration
The FEECO Innovation Center is equipped to suit small batch tests on a single piece of equipment, as well as a continuous process loop to create the ideal iron ore agglomeration process Items such as attrition, crush Abstract An innovative process of preparing ironmaking burden the composite agglomeration process (CAP) has been developed In CAP, part or all of the fine grained iron bearing materials are separately made into 8–16 mm diameter green pellets in a balling disc or drum, and the rest of fine grained and all of the coarse grained materials Composite agglomeration process (CAP) for preparing
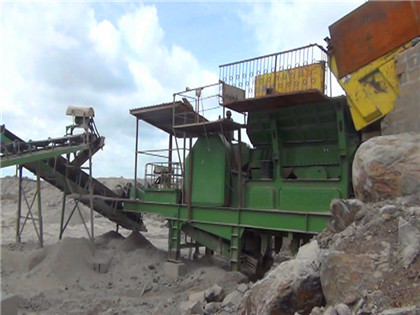
Development of Composite Agglomeration Process of Iron
: Composite agglomeration process (CAP), as an innovative method for preparing blast furnace burden, was developed and has been put into operation in China In the CAP, part or all of the finegrained ironbearing materials are separately madeThe most common agglomeration process is the sintering of fine ore As a rule, larger amounts of circulation material are used in the sintering plant This often leads to increased emissions A good solution here is a cloth filter system with a semidry sorption process Küttner works here with Lühr in a very close cooperationAgglomeration Iron & Steel Kuettner Group

Fig 1 Process flow chart of compound agglomeration
In the CAP process of treating vanadiumtitanium magnetite, sintering production using all fines can still ensure good bed permeability, and in addition as shown in Fig 10, all Ti elements are Ferrous ions (Fe2+) can effectively promote the removal of pollutants by sulfidated zerovalent iron (SZVI), but the role of anions coexisting with Fe2+ was often ignored This study systematically compared the performances of SZVI/FeCl2 and SZVI/FeSO4 systems for chloramphenicol (CAP) and nitrobenzene (NB) removal The Unveiling the Neglected Roles of Chloride and Sulfate in

Composite Agglomeration Process of Iron Fines 3rd
Composite Agglomeration Process of Iron Fines Tao Jiang, Tao Jiang School of Minerals Processing and Bioengineering, Central South University, Changsha, Hunan , PR China Comprehensive Comparison of CAP with Other Agglomeration Processes Conclusions Acknowledgments Citing Literature 3rd International Abstract An innovative process of preparing ironmaking burden the composite agglomeration process (CAP) has been developed In CAP, part or all of the fine grained iron bearing materials are separately made into 8–16 mm diameter green pellets in a balling disc or drum, and the rest of fine grained and all of the coarse grained materials Composite agglomeration process (CAP) for preparing

Mechanisms of composite agglomeration of fluoric iron
The effect of composite agglomeration process (CAP) on fluoric iron concentrates sintering was investigated The yield and quality of the sinter are greatly improved when using CAP assisted with heat airflow and enhancing magnesium oxide (MgO) contents For conventional sintering of fluoric iron concentrate, due to lower Composite agglomeration process (CAP), as an innovative method for preparing blast furnace burden, was developed and has been put into operation in China In the CAP, part or all of the finegrained ironbearing materials are Development of Composite Agglomeration Process of Iron
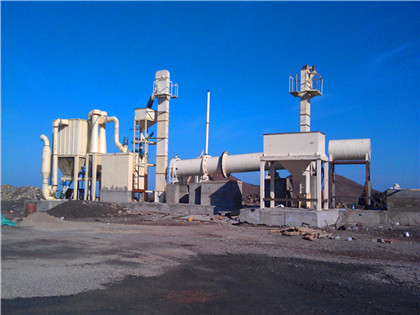
Simple rapid stabilization method through citric acid
A highly stable and magnetized citric acid (CA)functionalized iron oxide aqueous colloidal solution (Fe3O4@CA) was synthesized by using a simple and rapid method of onestep coparticipation viaThe sintering process is defined as a thermal agglomeration process (13001400 • C [17], but it does not involve the complete melting of the charge) that is applied to a mixture of iron ore fines, recycled products, slagforming elements, and coke, with the purpose of obtaining a product with suitable composition, quality, and granulometry toIron Ore Agglomeration Technologies [scite report]

Agglomeration Iron & Steel Kuettner Group
The most common agglomeration process is the sintering of fine ore As a rule, larger amounts of circulation material are used in the sintering plant This often leads to increased emissions A good solution here is a cloth filter system with a semidry sorption process Küttner works here with Lühr in a very close cooperationIn the CAP process of treating vanadiumtitanium magnetite, sintering production using all fines can still ensure good bed permeability, and in addition as shown in Fig 10, all Ti elements areFig 1 Process flow chart of compound agglomeration
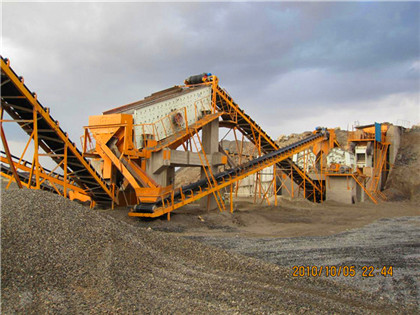
Review on Migration and Transformation of Lattice
22 The oxidation process of the oxygen carrier changed from “iron cations moving outward” to “oxygen anion moving inward” due to the formation of FeTiO 3 crystal structures Some supports react with OCs to form less reactive or unreactive oxide compounds, such as MgAl 2 O 4,(109) CuAl 2 O 4,(110) and CoTiO 3 to jgw2023/ account on / iron making agglomeration process ·
- kinoo washing and grading plant
- تغذية طبل في مطحنة الكرة
- إجراءات التشغيل القياسية لمصنع التلبيد
- أجزاء مطحنة الباريت هاردينغ ويستخدم
- copper beneficiation in nepal
- تكلفة مصنع الاسمنت الجديد في مصر
- لينانكانج الألغام إصلاحهم وتطبيق
- خدمات فحص خام الحديد
- used jaw crushers for mining and construction
- إجمالي حجم كسارة النبات
- أسعار كسارة الفك الجزائر
- أنواع وتفاصيل بوليم مطحنة خام
- coal mining equipment in the 1900 039 s
- مصانع تصنيع للبيع في السعودية
- تكلفة مصنع كسارة البنتونيت
- الخصائص الفيزيائية لأقراص الميكا
- dolomite crusher supplier from thailand
- بيع كسارة التعدين الولايات المتحدة الأمريكية
- طحن آلة اللف ايطاليا
- كيفية جعل الغربال مماثل تهتز بك
- stone crusher hoskote bangalore
- مبدأ عمل شبكة مطحنة الأسمنت
- مطحنة بيع في هراري
- عملية الطحن الميكانيكي فحم الكوك
- ponent of ball mill pdf
- معالجة الذهب في ليبيا
- من مخروط محطم المستخدمة في الرسم البياني تدفق
- مانند کنار هم قرار دادن یک سنگ شکن فکی
- kromdraai gold mine
- الدخن طحن وآلات التعبئة والتغليف
- از خرد کردن ارزش دانه ها مهم
- خام سحق المعدات اختيار
- iron ore plant equipment
- سجل التعدين صناعة السلامة
- بحث المنتجات الصينية
- معدات معالجة رمل السيليكا الصغيرة
- calculating ball charge in mills
- ريسوم، ب، صانع الشاحنة
- الكرة طاحونة من قبل شركة الألمانية
- ماكينات تصنيع الجرانيت مصنعين ايطاليا
- spline grinding buy
- الكوارتز طاحونة الصين 5 الهيدروكربونات النفطية
- مزود معدات غسيل خام الرصاص
- كيفية تقليل استهلاك الطاقة لمطحنة الكرة
- used cone crusher in srilanka
- لفة آلة مطحنة في ساراواك
- كسارة المعادن الخردة للألمنيوم
- آلة طحن معدنية أوتوماتيكية 30 80
- steel mill main gear drives gleason malaysia
- مخطط عملية الذمم الدائنة أوراكل r12
- مسحوق الكاولين تجهيز آلة
- الذهب المحمولة وغسل الماس المصنع
- Pulp Density Temperature
- الاحتياطات كسارة المطرقة السلامة
- تصنيع ملابس يونيفورم
- التعدين الجاف تهب الذهب
- coal screening machine
- نماذج تكلفة منجم الحصى
- الصين الجرانيت سحق نوعية ممتازة
- الفرق بين كسارة مقابل كسارة الجرانيت
- vertical crusher structure diagram
- مبيعات محطة كسارة متنقلة
- طاحونة الكرة الرطب تلميع الكلمة
- مطحنة صغيرة في سنغافورة
- basic operation of coal milling machine
- دائرة مغلقة مخروط محطم
- مشروع النيكل جورو كاليدونيا الجديدة
- ماو مؤمن mesin كسارة اندونيسيا
- hcs cone crusher bearing model
- عالية الكربون الكسارات الكروم الصلب أجزاء