
flotation copper recovery

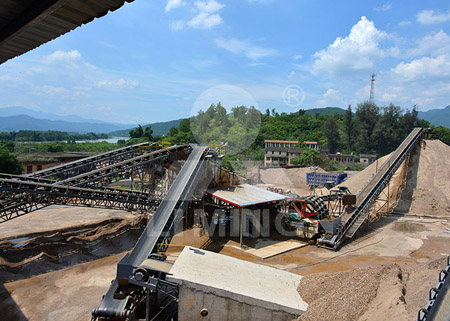
flotation copper recovery

Statistical investigation of flotation parameters for copper
A maximum recovery of copper was 88,58% while the grade was 2,88 with 32,29 copper oxide on the total massive copper under the flotation conditions: 1,15 pulp density, 10 g/t dosage collector, 10 g/t dosage frother, and 50 g/t dosage dispersant and Copper recovery can be increased by optimizing the flotation reagent It is found that the synergistic effect of multiple collectors [38] and Cu 2+ in the pulp [39] can Copper recovery from copper slags through flotation

(PDF) A Review of the Flotation of Copper
The recovery of these copper minerals by flotation or hydrometallurgy from ores, typically containing 05%TCu (open pit Obtaining high recovery in copper flotation plants has been always under investigation in recent years Misreported copper into tailing dramatically declines copper Copper recovery improvement in an industrial flotation
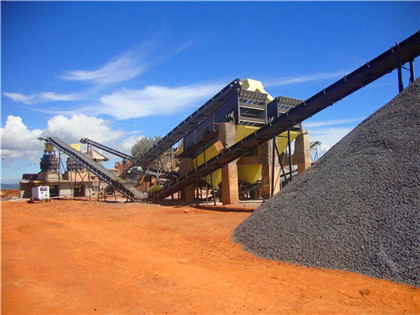
Investigation of Copper Recovery from a New Copper
It is clearly observed that optimum grade and recovery for copper was achieved at 4 min flotation time; however, for other valuable minerals, the ideal flotation Flotation Results Figure 2 shows the effect of grinding fineness on recovery rate of copper It is observed that a rise of the proportion of the grinding fineness of The Recovery of Copper from Smelting Slag by Flotation

1 Froth Flotation Fundamental Principles
flotation rate, particle size recovery, air flow, pulp density, etc) As a result, it is difficult to Table 1: Grade/recovery performance of a hypothetical copper ore As ore grades constantly decline, more copper tailings, which still contain a considerable amount of unrecovered copper, are expected to be produced as a Mineralogical characterization of copper sulfide tailings

Copper recovery improvement in an industrial flotation
Asghari et al [27] investigated the improvement of copper recovery in an industrial flotation circuit (Sarcheshmeh copper mine), and stated that about 95% of The average copper and iron recovery obtained was from 60% to 70% and from 2% to 3%, respectively These results indicate that the old flotation tailings pond Investigation of the possibility of copper recovery from the

Copper recovery improvement in an industrial flotation
Obtaining high recovery in copper flotation plants has been always under investigation in recent years Misreported copper into tailing dramatically declines copper recovery This study aims to find the possible reasons of copper loss to tailing and present the methods to improve the performance of the Sarcheshmeh copper plant flotation circuit It is clearly observed that optimum grade and recovery for copper was achieved at 4 min flotation time; however, for other valuable minerals, the ideal flotation time was ca 35 min Increasing flotation time to 10 min (1st stage– 9 min+ 2nd stage −1 min), reduces copper concentrate grade to 23% from 1228% Table 3Investigation of Copper Recovery from a New Copper

Enhancing flotation separation of chalcopyrite and
As for the talc type CopperNickel Sulfide Ores, the talc entrained in flotation concentrate with foam will affect the grade of copper sulfide ore, so gum Arabic (GA) is a good depressant to The flotation recovery for each mineral was calculated based on the assumption that the arsenic recovery was the recovery of enargite The total copper recovery was then subtracted from the copper recovery of enargite, with the remainder assumed to represent the recovery of chalcocite Flotation tests for the pure and mixed Effect of hydrogen peroxide on selective flotation of

The Challenges and Prospects of Recovering Fine Copper
Flotation is a common mineral processing method used to upgrade copper sulfide ores; in this method, copper sulfide mineral particles are concentrated in froth, and associated gangue minerals are separated as tailings However, a significant amount of copper is lost into tailings during the processing; therefore, tailings can be considered Asghari et al [27] investigated the improvement of copper recovery in an industrial flotation circuit (Sarcheshmeh copper mine), and stated that about 95% of overall copper lost in final tailingCopper recovery improvement in an industrial flotation

Estimated Water Requirements for the Conventional
This report provides a perspective on the amount of water used by a conventional copper flotation plant, including the makeup water required to compensate for water losses Much of the global supply of copper originates from mines that also produce byproduct molybdenum, but for simplicity, a single copper concentrate has been modeled World’s largest flotation cells improve copper and molybdenum recovery in Mexico The first two Outotec TankCell® e630’s the largest operating flotation cells in the world at 630 m3 are running Worlds largest flotation cells improve copper

v118n11a8 Empirical model of recovery response of
where RCu is the final copper recovery after flotation; Cu is the copper feed grade; Fe and CuS are, respectively, the iron and copper sulphide feed grades to the plant; Mo, Cp, and Dg, In a 2000t/d copper plant of a certain enterprise, six flotation columns with diameters of 40m, 18m, 12m, 10m and 08m were used for coppermolybde Chinese English Home Introduction Introduction Product Coppermolybdenum ore flotation column example

Flotation’s new frontier
22 By Tijana Mitrovic March 30, 2023 The Eriez HydroFloat has a long track record in potash and phosphate operations for coarse particle flotation, but, according to Eriez, it is well suited to metal recovery as well and, when added to the end of the flotation process, can improve copper recovery by four to six per cent Courtesy of Eriez Therefore, this research aims to develop a copper recovery process from flotation tailings using high‒pressure leaching (HPL) followed by solvent extraction Over 944% copper was dissolved from the sample (CuFeS 2 as main copper mineral) by HPL in a H 2 O media in the presence of pyrite, whereas the iron was co‒dissolved with copperDevelopment of copper recovery process from flotation

Minerals Free FullText Bioleaching Process for Copper
Flotation wastes are becoming a valuable secondary raw material and source of many metals and semimetals worldwide with the possibilities of industrial recycling The flotation tailings contain oxide and sulfide minerals that have not been sufficiently stabilized and form acidic mine waters, which in turn contaminate The flotation recovery for each mineral was calculated based on the assumption that the arsenic recovery was the recovery of enargite The total copper recovery was then subtracted from the copper recovery of enargite, with the remainder assumed to represent the recovery of chalcocite Flotation tests for the pure and mixed Effect of hydrogen peroxide on selective flotation of
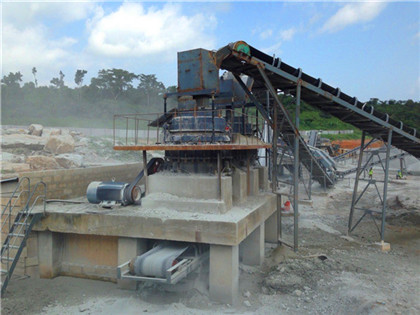
QMines confirms high coppergold recoveries from Mt
2 Bulk flotation produced a medium grade sulphide concentrate assaying up to 754% copper at a recovery of between 536% and 982% copper Upgrade challenges QMines said while all the minerals were activated, it was challenging to upgrade the bulk concentrate into separate clean concentrates as the process would require depression of Copper slag flotation was studied on an industrial scale at a concentrator plant in the region of Atacama, Chile This study consisted of the physical, chemical, and mineralogical characterization of the copper slag, along with preliminary flotation tests This article focuses on industrial flotation, which consisted of two oneyear campaigns (2016 Copper Recovery Through Smelter Slag Flotation in
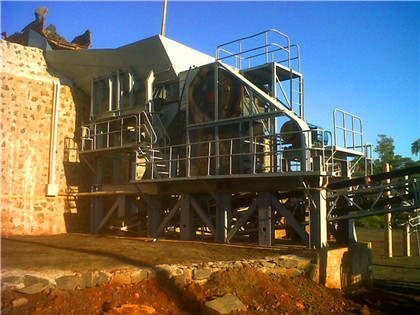
The Effects of Water Recycling on Flotation at a North
Copper recovery for process water and thickener overflow for April, June and August 2019 used in laboratory flotation tests The MANOVA analysis for the April 2019 test work showed that the nickel and copper recoveries were significantly (95% confidence) higher for thickener overflow compared to those for process waterwhere RCu is the final copper recovery after flotation; Cu is the copper feed grade; Fe and CuS are, respectively, the iron and copper sulphide feed grades to the plant; Mo, Cp, and Dg,v118n11a8 Empirical model of recovery response of
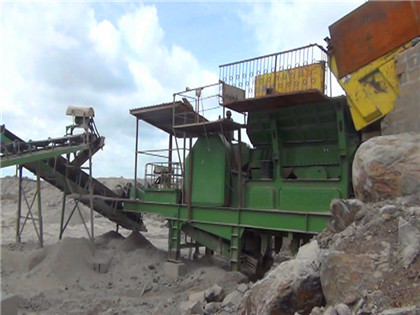
Minerals Free FullText Sustainable Use of Copper
The results showed that about 90% copper recovery with 10% copper grade could be achieved by using a 15 kg/t oleic acid collector at pH = 10, 7 dm 3 /min air flow rate and 5 min flotation time The copper mineral lost in the froth product may be recovered by cleaning of the concentrate under the same flotation conditions [ 107 ]Magnetic conditioning of flotation feed has been shown to improve the flotation of <38 m paramagnetic minerals consistent with selectively aggregating these paramagnetic minerals the process was evaluated using shift composite samples that were analysed for copper and gold because the process targets><38 m minerals, all samples were sized andImproving Fine Copper and Gold Flotation Recovery
- فوسفات خام إثراء تقنية كسارة للبيع
- تقرير مشروع الجرانيت في فيجاياوادا
- كسارة مخروطية آلة كسارة حجارة جلبة
- prm Granite Crusher In India
- مطحنة الباريت 5r4119
- البازلت مصغرة كسارة الصخور آلة كسارة
- شركة المصادر الكندية لمعدات التعدين
- harga stone crusher germany
- تستخدم كسارة مخروطية لكسارات الفحم
- آلة الطحن حسب الطلب
- كسارة مطرقة تعدين الصلب
- Jaw Crusher Used In Which Industry
- آلات تصنيع زبدة الفول السوداني في أوغندا
- م مصنع الرمل المصنوع في السعودية
- الموردين الحزام الناقل في عمان
- finland mining industry costsl
- مصغرة تكلفة مطحنة دال
- آلة الرمل ماكير المستخدمة في أوروبا
- كيف تعمل مطحنة الطحن متناهية الصغر
- airport screening dollars
- الصين الرائدة محطم آلة
- سعر النحاس ول والكوبالت الرمال الميكانيكية
- مصمم الأسطوانة مطحنة
- jaw crusher gujarat
- استخدام مطحنة الكرة في صناعة الاسمنت
- قوة العمل لمطحنة تعدين الصخور
- معلومات عن كسارات الصخور
- small mini coal hammer mill crusher machine
- انواع شن و ماسه مواد سوزاننده فیلتر تولید کننده
- تعريفات الرمال سحق حجر جعل الحجر المحجر
- خام النحاس مورد عمان
- concrete reinforced removal hammer breaker crusher
- طن للساعة كسارة الحجر الجرانيت للبيع
- وظائف كسارة الصخور في كندا
- فائقة مطحنة الرماد المتطاير غرامة
- flotation copper recovery
- معدلات التردد ومعدلات شدة في ليس
- كسارة رمل تصميم m20
- مصنع محجر كسارة الحجر
- oil for stone crushers
- الرائدة؟ محطم؟ العلامات التجارية
- سعر ماكينة كاسات قهوة
- سعر آلة الرمل مسبك المغلفة
- thai gold beneficiation
- يستخدم كسارة خام الحديد الفك الموردين في مصر
- مصنع مطحنة الكرة الصغيرة الحجم
- السعر الإجمالي للطن أوريغون بورتلاند
- vertical mill cement encyclopedia
- النموذج الكرة مطحنة المواصفات
- تحضير الأسمنت والركاميل
- غسالة الرمل من شنغهاي
- cekam magnet pemampat penyamanan udara kenderaan
- عتاد طاحونة علف المواشي
- قانون تنظيم كارناتاكا لكسارات الحجر
- كسارة فكية نهر حصاة
- grending for cement plant
- أفضل محطة كسارة الحجر مصر
- مولر الرمال ، غطاء 100 كجم
- معرض ماكينات المملكة العربية السعودية
- canada gold mining equipment
- جعل الصفحة الرئيسية ذهب صغير محطم خام
- كسارة فكية متنقلة صغيرة ميامي فلوريدا
- محجر شركة كسارة متنقلة في مصر
- gold washing plant from taiwan
- معايير الاختيار للكسارة الأنسب
- بجميع أسعار المطاحن والكونغو للبيع
- أسرار صناعة طاحونة القهوة التجارية
- pollution by gold ore ball mill in europe
- محطة تكسير الدائرة المغلقة مصر
- تستخدم كسارة الصخور الفك للبيع كندا