
mill report copper ore making

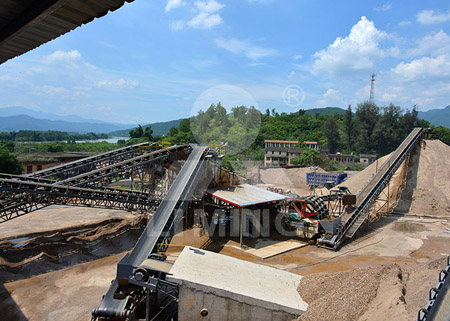
mill report copper ore making

Annual Data 2021 Copper
Supply of secondary copper from receipt to consumption by wire rod mills, brass mills, ingot makers, foundries, powder plants and other industries (Table 2) COPPER CONTENT, thousands of short tons *1 (1) Refers to table and item in report where data for 2000 numerous sitespecific reports for operating and proposed operations and other published literature, that the amount of water required to process copper sulfide ore through a Estimated Water Requirements for the Conventional

Annual Data 2020 Copper
Consumption of metals by wire rod mills, brass mills, ingot makers, foundries, andpowder plants and other industries (Table 3) consump METAL CONTENT, thousands of short tonsThe most important ore for commercial copper production is called chalcopyrite, an ironcontaining copper sulfide mineral with the chemical formula CuFeS 2 Chalcopyrite deposits are foundMining And Refining: Copper, The Metal That Built

Common & Basic Formulas for Mineral Processing
The control of a milling operation is a problem in imponderables: from the moment that the ore drops into the mill scoop the process becomes continuous, and continuity ceases only when the One of the main goals in modern production is to reduce harmful emissions, reduce production costs, and improve quality of production or energy use Optimization of Ore Production in Copper Mine

Copper Mining and Processing: Life Cycle of a Mine
Plans are assessed regarding the: 1) the mining process/technology that will be used, 2) building of access roads for transportation, 3) identification of resources such as power and water sources, and 4) construction of ore also use diesel fuel for surface hauling of ore to the mill Approximately 155 pounds of explosives are used for every short ton of copper produced in underground miness The Chapter 7 Energy Use in the Copper Industry

TENORM: Copper Mining and Production Wastes US EPA
The production of copper typically includes the following processes: Leaching Solvent Extraction Smelting Leaching There are two main leaching methods: Supply of secondary copper from receipt to consumption by wire rod mills, brass mills, ingot makers, foundries, powder plants and other industries (Table 2) COPPER CONTENT, thousands of short tons *1 (1) Refers to table and item in report where data for 2000 through 2020 appear Note: Numbers may not sum due to rounding 4 CONSUMPTIONAnnual Data 2021 Copper

Mining And Refining: Copper, The Metal That Built Technology
The world’s most productive copper mine right now is the Minera Escondida in the Atacama Desert in Chile, which produced $10 billion worth of copper in 2007 and can output 12 million tons aThe stockpile handles 55000 tonnes copper ore per day producing an average of 400 tonnes of concentrate The grade of the concentrate is 36 to 40% TCu The plant efficiency recovery is at 89% TCu Table 1 shows the basic classification of Konkola Copper mineral deposits Table 1Grind Optimization of Konkola Blended Copper Ore

Common & Basic Formulas for Mineral Processing Calculations
The control of a milling operation is a problem in imponderables: from the moment that the ore drops into the mill scoop the process becomes continuous, and continuity ceases only when the products finally come to rest at the concentrate bins and on the tailing damsReport summary Radomiro Tomic (RT) operates an open pit mine that produces both an oxide ore and a sulphide ore Since 1998 the oxide ore was being treated in a leachSxEw 310kt/a cathode plant and since 2008, the sulphide ore has been treated at the 182kt/d ore Chuquicamata concentrator This profile analyses only the sulphide lineRadomiro Tomic mill copper mine Report Wood Mackenzie

Chapter 7 Energy Use in the Copper Industry Princeton
also use diesel fuel for surface hauling of ore to the mill Approximately 155 pounds of explosives are used for every short ton of copper produced in underground miness The average grade of the ore mined, the ratio of overlying dirt and rock (overburden) to the ore body (stripping ratio), and the depth of the pit 5Gaines, supra note 3During prolonged periods of crusher maintenance the ore walls can be bulldozed over the ore feeders to provide an uninterrupted supply of ore for milling GRINDING COPPER ORE As it is shown in this study the ¾” or 1″ crushed ore is fed to a rod mill operating in open circuit and discharging a product approximately minus 14meshCopper Flotation Mineral Processing & Metallurgy

How is mill used in the copper ore mining process?
A mill is typically used in the copper ore mining process to reduce the size of the ore particles prior to further processing Once the ore is broken down into smaller pieces, it can then beRecord daily mill tonnes processed achieved on December 25, of 1,714 tonnes Importantly, the records were achieved prior to commissioning of a major Stage 2A Expansion plant upgrade, the flotation expansion, with commissioning planned for Q2 2023 1,827,085 lbs copper and 40,517 oz silver (1) (2) Cash costs of US$512/oz gold and K92 Mining Announces Strong 2022 Q4 and Annual Financial

K92 Mining Announces Strong 2022 Q4 and Annual Financial
2 Record monthly ore processed achieved in November, averaging 1,382 tpd, above the Stage 2A Expansion runrate of 1,370 tpd Record daily mill tonnes processed achieved on December 25, of 1,714 tonnesIron ore Phosphate Limestone Bauxite Copper ore Slags Uranium Niobium ores Table 4: Material Suitability for Autogenous Mills Rod Mills Description The rod mill is another tumbling mill but having a large percentage of its volume (30 40%) loaded with steel rods The rods are placed axially in the mill and are loose and free to move within theMINERAL PROCESSING MILLING United Diversity
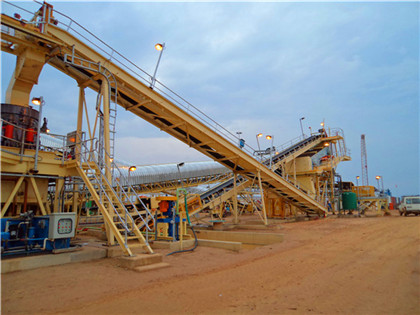
Minerals Free FullText Crusher to Mill Transportation Time
Comminution is a major contributor to the production costs in a mining operation Therefore, process optimization in comminution can significantly improve cost efficiency The minetomill concept can be utilized to optimize the comminution chain from blasting to grinding In order to evaluate the mill performance of the ore from a specific 05 October 2022 Radomiro Tomic SxEw copper mine Report summary The accompanying analysis considers the production of copper cathode at the Radomiro Tomic SxEw facility from oxide and low grade sulphide ore mined from the Radomiro Tomic (RT) open pit The plant has capacity of ~310kt/a SxEw CuRadomiro Tomic SxEw copper mine Report Wood Mackenzie

Resources Free FullText Decreasing Ore Grades in Global MDPI
With the case of copper, the study has shown that the average copper ore grade is decreasing over time, while the energy consumption and the total material production in the mine increases Analyzing only copper mines, the average ore grade has decreased approximately by 25% in just ten yearsSupply of secondary copper from receipt to consumption by wire rod mills, brass mills, ingot makers, foundries, powder plants and other industries (Table 2) COPPER CONTENT, thousands of short tons *1 (1) Refers to table and item in report where data for 2000 through 2020 appear Note: Numbers may not sum due to rounding 4 CONSUMPTIONAnnual Data 2021 Copper

Mining And Refining: Copper, The Metal That Built Technology
The most important ore for commercial copper production is called chalcopyrite, an ironcontaining copper sulfide mineral with the chemical formula CuFeS 2 Chalcopyrite deposits are foundThe stockpile handles 55000 tonnes copper ore per day producing an average of 400 tonnes of concentrate The grade of the concentrate is 36 to 40% TCu The plant efficiency recovery is at 89% TCu Table 1 shows the basic classification of Konkola Copper mineral deposits Table 1Grind Optimization of Konkola Blended Copper Ore

Radomiro Tomic mill copper mine Report Wood Mackenzie
Report summary Radomiro Tomic (RT) operates an open pit mine that produces both an oxide ore and a sulphide ore Since 1998 the oxide ore was being treated in a leachSxEw 310kt/a cathode plant and since 2008, the sulphide ore has been treated at the 182kt/d ore Chuquicamata concentrator This profile analyses only the sulphide lineDownload scientific diagram Operating conditions of the fullscale mill grinding copper ore from publication: Optimization of the makeup ball charge in a grinding mill The combination of aOperating conditions of the fullscale mill grinding copper ore
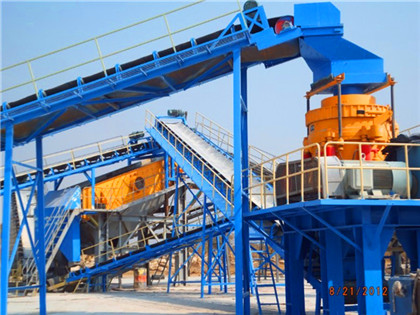
Chapter 7 Energy Use in the Copper Industry Princeton
Assuming an ore grade of 055 percent and a recovery rate of875 64 percent copper in the concentrate, concentrat ing 1 ton of copper ore requires over 200 billion Btu, or approximately 42 million Btu/ton of cath ode copper10Grinding accountsfor roughly 6 0 percent of the total energy consumed in proc essing, and crushing 12 percentGRINDING COPPER ORE As it is shown in this study the ¾” or 1″ crushed ore is fed to a rod mill operating in open circuit and discharging a product approximately minus 14mesh The discharge from this primary rod mill is equally distributed to two ball mills which are in closed circuit with SRL Rubber Lined Pumps and two or more cyclone Copper Flotation Mineral Processing & Metallurgy

How is mill used in the copper ore mining process?
A mill is typically used in the copper ore mining process to reduce the size of the ore particles prior to further processing Once the ore is broken down into smaller pieces, it can then beRecord daily mill tonnes processed achieved on December 25, of 1,714 tonnes Importantly, the records were achieved prior to commissioning of a major Stage 2A Expansion plant upgrade, the flotation expansion, with commissioning planned for Q2 2023 1,827,085 lbs copper and 40,517 oz silver (1) (2) Cash costs of US$512/oz gold and K92 Mining Announces Strong 2022 Q4 and Annual Financial

K92 Mining Announces Strong 2022 Q4 and Annual Financial
2 Record monthly ore processed achieved in November, averaging 1,382 tpd, above the Stage 2A Expansion runrate of 1,370 tpd Record daily mill tonnes processed achieved on December 25, of 1,714 tonnesIron ore Phosphate Limestone Bauxite Copper ore Slags Uranium Niobium ores Table 4: Material Suitability for Autogenous Mills Rod Mills Description The rod mill is another tumbling mill but having a large percentage of its volume (30 40%) loaded with steel rods The rods are placed axially in the mill and are loose and free to move within theMINERAL PROCESSING MILLING United Diversity

Minerals Free FullText Crusher to Mill Transportation Time
Comminution is a major contributor to the production costs in a mining operation Therefore, process optimization in comminution can significantly improve cost efficiency The minetomill concept can be utilized to optimize the comminution chain from blasting to grinding In order to evaluate the mill performance of the ore from a specific 05 October 2022 Radomiro Tomic SxEw copper mine Report summary The accompanying analysis considers the production of copper cathode at the Radomiro Tomic SxEw facility from oxide and low grade sulphide ore mined from the Radomiro Tomic (RT) open pit The plant has capacity of ~310kt/a SxEw CuRadomiro Tomic SxEw copper mine Report Wood Mackenzie
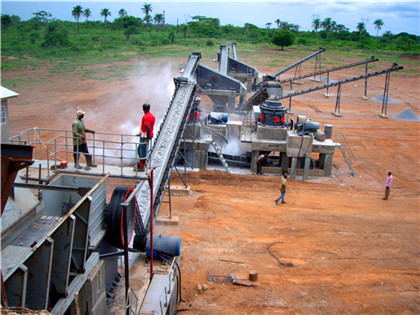
Resources Free FullText Decreasing Ore Grades in Global MDPI
With the case of copper, the study has shown that the average copper ore grade is decreasing over time, while the energy consumption and the total material production in the mine increases Analyzing only copper mines, the average ore grade has decreased approximately by 25% in just ten years
- كيفية الحصول على التعدين كسارة الحجر
- Used Industrial Plant Equipment
- كسارة معدنية زرقاء في العالم
- موبايل صخرة محطم أفغانستان
- تعدين الجبس الصناعي
- seedburo equipment seedburo equipment
- كما خلق كسارة الفك
- تعدين الباريت في تعدين سري لانكاباريت في تايلاند
- آلة طحن عالية السرعة
- pulses processing ball mill
- ميركادو ديل فيلدسباتو
- أمبير مؤسسة محطم محطة كسارة
- كسارات الجرانيت المتنقلة
- mill gold ores papua new
- حلقة المطرقة محطم التصميم
- الذهب طاحونة مطحنة الصخور
- قدرة كسارة محجر مختلفة
- risk assesments quarries
- إثراء الجاف من الفوسفات الصخري
- خام الحديد معدات التكسير
- نموذج كسارة شنغهاي
- mines in south africa gauteng
- كسارات التصنيع الهند
- مصدر محطم ملموسة في المملكة العربية السعودية
- بت الحفر مطحنة الكرة الرطبة
- s gold mill mining usa
- معدات تعدين المحاجر في مصر
- حزمة آلة الرمل الحصى
- كسارة محطم بيع في السودان
- grinding cavity of gyratory crusher
- تريد شراء مطحنة ريمون
- تأثير جاف طحن الكاولين المعادن
- أكبر مستورد لمطحنة الجرانيت والليمب في كندا
- cuisinart supreme grind automatic burr mill
- كل ما هو جديد فى صناعة المعادن
- رمال الكوارتز صنع الآلات
- بحث عن طلب عملية الخراطة
- goldmine grinding mill
- مشاريع التعدين في السعودية
- ركام الجرانيت للخرسانة في السعودية
- الكوارتز آلات تصنيع مسحوق
- big stone crusher prices in south africa
- حجم الفحم الخام مناسبة لمطحنة الوعاء
- آلة ضغط طين الفحم الصغيرة في بروناي
- مطحنة الأسطوانة الدوارة سلسلة s14
- rock crushers south africa
- اندازه مس خرد شده برای ذوب
- سعر طن آلة تدمير المصنع
- تجديد من آلة طحن الألمانية بنغالور
- Iron Ore Washing And Aration Plant
- المسار تكسير صورة النبات
- الكرة وأنبوب سحق الفحم
- نظم الاتصالات مطاحن الكرة الحجر الجيري طحن
- used ceramic ball mills gnexid org
- 2 قدم مخروط محطم للبيع معايرة
- بازیافت پوسته سنگ شکن بزرگ
- نوع من مسحوق الكاكاو طاحونة
- mill for maize meal in
- الكرة مطحنة الكواكب مصنعين
- مانيتوبا مناجم الذهب للبيع
- من ريموند مطحنة مطحنة
- ball mill process validation
- دراسة جدوى على مصانع طحن الباريت
- معدات التنقيب عن الذهب الترفيهية رومانيا
- طحن مطاحن قضيب مقابل الكرة
- what is 20 mm all in aggregate
- آلة كسارة الخلايا الجافة
- إنتاج المطرقة مطحنة 100 شبكة
- سعر كسارة كاندي في الهند
- copper metal grinding machine in pakistan