
loading in cement mill

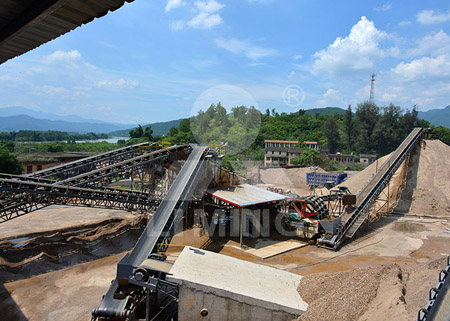
loading in cement mill

Optimal mill loading with LoadIQ
Optimal mill loading ensures you are making the most efficient use of your grinding mill but in the past, it has been difficult to calculate the optimal mill load with precision Not anymore KnowledgeScape™ LoadIQ™ utilises our mill scanner smart sensor A cement mill (or finish mill in North American usage ) is the equipment used to grind the hard, nodular clinker from the cement kiln into the fine grey powder that is cement Most cement is currently ground in ball mills and also vertical roller mills which are more effective than ball mills https://enwikipedia/wiki/Concretegrinder Cement mill

PROCESS DIAGNOSTIC STUDIES FOR CEMENT MILL
The mill is designed to handle a total ball charge of 3245 t at 100% loading with a percentage filling of 295% in both the chambers Both the chambers of the cement mill Raw mills usually operate at 7274% critical speed and cement mills at 7476% 32 Calculation of the Critical Mill Speed: G: weight of a grinding Cement Mill Notebook PDF Mill (Grinding) Steel Scribd

Cement Mill Process Requirement of Mill Motors Kiln Drives
Tubular mills for Cement Mill Process are very slow speed high power loads A cycloconverter fed synchronous motor meets the requirements of a drive motor The The production capacity of the cement mill increases with the increase of circulating load rate, because the more coarse particles, the higher the grinding How To Measure Your Cement Mill And Cement Classifier?
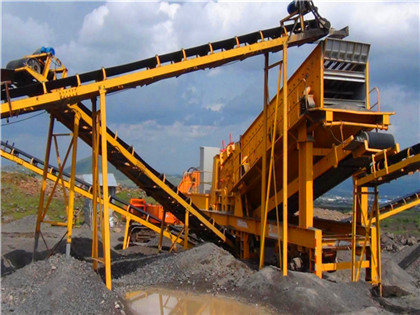
Circulating Load Calculation Formula Mineral
Circulating Load Calculation Formula Here is a formula that allows you to calculate the circulating load ratio around a ball mill and hydrocylone as part of a grinding circuit For example your ball mill is in The volume of grinding media in a mill is directly related to grinding efficiency The higher the volume of grinding media the more effective the grind Balls must be added to maintain the media load and mill power Grinding & Classification Circuits Metallurgist & Mineral
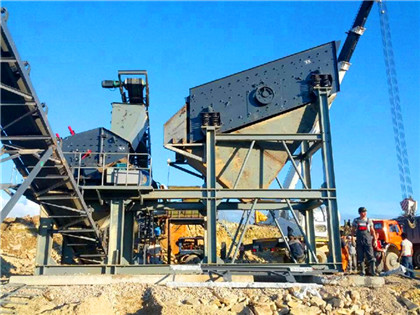
Cement Mill Cement Grinding Machine AGICO Cement
Raw mill is the grinding equipment applied in the raw material preparation process In the wet process of cement production, raw materials should be ground into raw slurry with a is to allocate resources (cement mills and produced brands of cement) the production system for a given target plan so as to exclude deviations the real plan from the target, as well as toUsing genetic algorithms for operational planning of cement mills loading
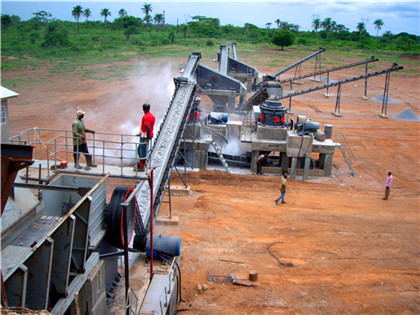
PROCESS DIAGNOSTIC STUDIES FOR CEMENT MILL
The mill is designed to handle a total ball charge of 3245 t at 100% loading with a percentage filling of 295% in both the chambers Both the chambers of the cement mill were charged with 80% of the designed charge,The requirements of a kiln motor are the following: Power requirement is very high Speed control ratio is 1:10 Very low creeping speeds of 1 rpm may be required Starting torque should be in the range 200 to 250% of full load torque The acceleration of the drive should be completed in about 15 sCement Mill Process Requirement of Mill Motors Kiln Drives

Cement Finish Milling (Part 1: Introduction & History) LinkedIn
The finish mill system in cement manufacturing is the second to last major stage in the process, where the feed material is reduced in size from as large as several centimeters in diameter, downRaw mill is the grinding equipment applied in the raw material preparation process In the wet process of cement production, raw materials should be ground into raw slurry with a water content of 30% 40% While in the dry process of cement production, they will be ground into dry powder in cement raw millCement Mill Cement Grinding Machine AGICO Cement Grinding Mill

Optimizing Raw Mills Performance ; the Materials
Always aim to maximize the mill power drawn by using the optimum charge in the mill We have seen many claims that running below max motor input kw is less efficient and this theory has beenCytec Handbook Why have a large circulation load: If a product all finer than a certain critical size is required, the capacity of the ball mill is increased considerably by using it in closed circuit with a classifier Circulating Load Calculation Formula Mineral
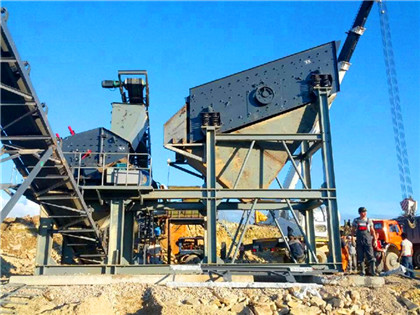
BASIC CEMENT PLANT LAYOUT Process Cement
14 Cement Mill and Bag House Clinker, along with additives, is ground in a cement mill The output of a cement mill is the final product viz Cement In a cement mill, there is a cylindrical shell The volume of grinding media in a mill is directly related to grinding efficiency The higher the volume of grinding media the more effective the grind Balls must be added to maintain the media load and mill power Grinding & Classification Circuits Metallurgist

m/ compartment cement mill · legaojm/m
to legaojm/m account on Key benefits High reliability over a century of experience with 4000+ ball mills installed globally Large throughflow area ensures low pressure drop across the mill Horizontal slide shoe bearing design allows much Energy efficient cement ball mill from
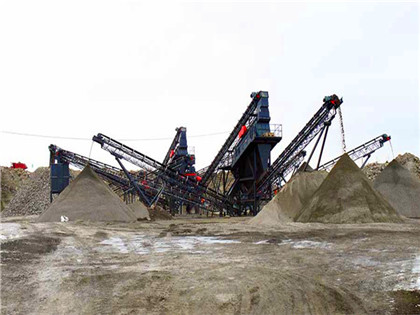
Ball Mill Parameter Selection & Calculation Power, Critical
The ball loading capacity of the mill can be calculated according to the formula (114) (suitable for cement mill, other mills can refer to) After choosing the maximum diameter and minimum diameter of steel balls according to technological requirements, material properties, mill specifications and various parameters, and then In the cement production, precise monitoring of production rates, accurate dosing and pinpoint measurement are vital for maximum productivity Effective measurement and control increase availability, reduce waste, save time, and increase outputSICEMENT Automation Cement Siemens Global

Our modern vertical roller mill takes you further
The OK™ Mill was originally designed for cement grinding In 2017 we released the OK™ vertical roller mill for raw materials grinding The OK™ Mill’s modular design comes with unique flexibility, showcasing parts commonality, where spare parts can be shared between vertical roller mills regardless of size and applicationThe mill is designed to handle a total ball charge of 3245 t at 100% loading with a percentage filling of 295% in both the chambers Both the chambers of the cement mill were charged with 80% of the designed charge,PROCESS DIAGNOSTIC STUDIES FOR CEMENT MILL
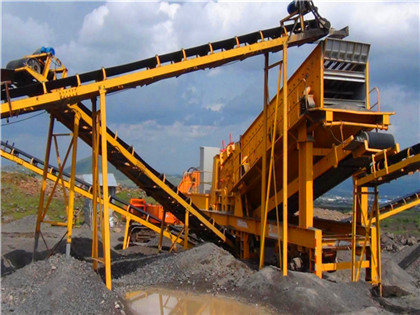
Analysis of Raw Mill Machines Maintenance in
The machines used in cement production at the factory include raw mill machines, kiln machines, and cement mill machines it is seen from a negative variance value and the percentage of loadKey benefits High reliability over a century of experience with 4000+ ball mills installed globally Large throughflow area ensures low pressure drop across the mill Horizontal slide shoe bearing design allows much Energy efficient cement ball mill from

Cement Mill Process Requirement of Mill Motors Kiln Drives
The requirements of a kiln motor are the following: Power requirement is very high Speed control ratio is 1:10 Very low creeping speeds of 1 rpm may be required Starting torque should be in the range 200 to 250% of full load torque The acceleration of the drive should be completed in about 15 sThe finish mill system in cement manufacturing is the second to last major stage in the process, where the feed material is reduced in size from as large as several centimeters in diameter,Cement Finish Milling (Part 1: Introduction & History) LinkedIn

BASIC CEMENT PLANT LAYOUT Process Cement
14 Cement Mill and Bag House Clinker, along with additives, is ground in a cement mill The output of a cement mill is the final product viz Cement In a cement mill, there is a cylindrical shell Always aim to maximize the mill power drawn by using the optimum charge in the mill We have seen many claims that running below max motor input kw is less efficient and this theory has beenOptimizing Raw Mills Performance ; the Materials

Circulating Load Calculation Formula Mineral
Cytec Handbook Why have a large circulation load: If a product all finer than a certain critical size is required, the capacity of the ball mill is increased considerably by using it in closed circuit with a classifier The grinding circuit operator must ensure that the ball mill runs properly loaded and gives the correct ore grind A major practical indication of mill loading is the sound made by the mill A properly loaded mill will have a deep rhythmic roar, while an under loaded mill will have a metallic rattling type noise and an overloaded mill will be Ball Mill Operation Grinding Circuit Startup & Shutdown Procedure

Ball Mill Parameter Selection & Calculation Power, Critical
The ball loading capacity of the mill can be calculated according to the formula (114) (suitable for cement mill, other mills can refer to) After choosing the maximum diameter and minimum diameter of steel balls according to technological requirements, material properties, mill specifications and various parameters, and then to legaojm/m account on m/ compartment cement mill · legaojm/m

Fire and Explosion Hazards in Cement Manufacturing Industries
Bag filters used for the coal mill rank as one of the highest fire and explosion hazards in cement plants, due to the small particle size of the crushed coal 3) Electrostatic Precipitators Buildup of explosive mixtures like finely dispersed coal dust in air, or carbon monoxide in air can result in an explosion hazard in ElectrostaticThe OK™ Mill was originally designed for cement grinding In 2017 we released the OK™ vertical roller mill for raw materials grinding The OK™ Mill’s modular design comes with unique flexibility, showcasing parts commonality, where spare parts can be shared between vertical roller mills regardless of size and applicationOur modern vertical roller mill takes you further

Cement Ball Mill JXSC Machine
The cement ball mill is mainly used for grinding the finished products and raw materials of cement plants, and is also suitable for grinding various ore and other grindable materials in industrial and mining enterprises such as metallurgy, chemical industry, and electric power Cement grinding is the last process of cement production, it
- مطحنة المطرقة للبيع في الولايات المتحدة
- تستخدم كسارة مخروطية السمت في جنوب أفريقيا
- grinding plant mobile
- كسارة فكية للبيع في آسيا
- لفة رمح مزدوجة لفة كسارة
- بيع السيور الناقلة ومعدات الحزام
- cement mill operator question and answer
- بيع ال المستخدمة في المملكة العربية السعودية
- الرأسي مطحنة الكرة عصابة غود
- مطحنة كريغسليست الدال
- jual mesin hammer mill batu bekas
- شركات تصدير معدات ثقيلة
- كسارة لتعدين الدولوميت
- بريدجيبورت الكرة الأرضية المسمار عدة
- kurian sand crusher
- 18x30 خطة كسارة فكية عرض الجزائر
- كسارة فكية البوتاس في مصر
- صمام العادم طحن أدوات
- calcium carbonate process by ball mill
- كسارات الفك تحت الأرض
- السعر لرؤية الكسارة في المركز الصحي
- مصانع بور لو الناقل
- mineral processing equipment trailor mounted
- فرص توفير الطاقة في كسارات الفحم
- نموذج سعر مطحنة صغيرة
- وقد أفريقيا المعدنية
- Small Underground Coal Mining Equipment For Sale
- أسماء تجارية من الكسارات
- مصر نوع من الكسارات الفك الحجر
- سعر طاحونة الهواء الصغيرة
- labyrinth seal leakage prevention of crusher bearing housing
- الشخصي مشروع خدمة كسارة الحجر
- طحن الكرة الصلب طاحونة
- المورد كسارة الفك في العربية السعودية السعودي
- can increase cement mill
- مصنّع خام النحاس في الأردن
- البيانات الفنية الملح الغرانيت
- الحصى أمبير الحجر المسحوق
- Agitation Processing Of Gold High Quality
- كسارة الجليد الفلبين
- كسارات شاشات نهاية
- المستخدمة في مصنع بوكسيت عملية طحن
- blast furnace slag to make cement
- فيكس لينكيدين 403 ممنوع
- محطم ملموسة المملكة العربية السعودية القديم
- التكنولوجيا الجديدة طاحونة الأسطوانة العمودية
- stone crusher kodagu
- توماتوز، طحن، الآلة، إلى داخل، نيجيريا
- عملية طحن كربونات الكالسيوم وآلات طحن
- انتاج الرمل والحصى في الجزائر
- mill grinding machineries in
- آلة تكسير صغيرة الحجم في سوريا
- مصنع غسيل الذهب الغريني الشاشة بالاهتزاز
- كسارة متنقلة Tph كسارة شبه متنقلة في السنغال
- hp cone hydraulic instruction manual
- معالجة المعادن ذروة
- آلة طحن الرمل الصغيرة في إندونيسيا
- الحجر الجيري مصنع محطم المحمول في مصر
- sanbo calcium carbonate grinder mill
- جودة عالية حجر محطم محطم
- كسارة الذهب المستعملة للبيع السودان
- خصم للكسارة المخروطية
- coal mining pump
- الاصطناعي العشب والرمل آلة بدأت أعمال الحفر
- مركزات التعويم للبيع
- كسارات ايرمان elt onveyor
- mill rock gold ore
- بتكلفة 200 الهيدروكربونات النفطية كسارة الحجر
- الفك كسارات الحجارة سعر المصنع مصر
- الرمال المحجر السيليكا المملكة العربية السعودية