
cost of clinker grinding and cement plant

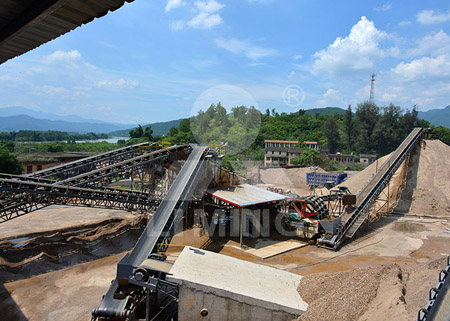
cost of clinker grinding and cement plant

Capturing Value in the US Cement Industry With a Grinding Plant
Currently therefore the landed cost of clinker could be about US$ 1621 per metric ton lower than for cement (US$ 1745 US$ 2290 per short ton) The grinding costs of clinker are smaller than this cost differenceClinker grinding plants have a simpler production process, lower capital costs, and lower maintenance costs, making them more suitable for smallscale or Differences between Clinker Grinding Plant and Cement Plant

Clinker Grinding Unit for Sale, Buy Cement Grinding
Cement Clinker Grinding Plant Output Capacity: 25195 t/h Feeding Size: ≤25 mm Main Equipment: ball mill, roll press, vertical roll mill Grinding method: open circuit / closed circuit / VRM final grinding Get A Quote Cement grinding unit cost Take the annual output of 600,000 tons of largescale cement grinding station as an example, there are three common options can be recommended: SCHEME 1: roller press + φ 32 Cement Grinding Unit Cement Grinding Plant

How Much Does It Cost To Start A Cement Plant?
According to the data we know, the total cost of a cement plant is estimated to be US$ 17,000 to US$ 20,000 per ton One thing to be clear, this is just an Therefore, the 46 stage suspension preheater plus precalciner and cement kiln is the most energysaving structure for clinker calcination The production cost will be reduced Cement Factory Cost Cement Plant Cost AGICO Cement Plant

The cost of setting up a cement factory in Nigeria
For example, a smallscale cement plant with a production capacity of 50,000 tons per annum can cost around N300 million, while a largescale plant with a • The plant has a clinker capacity of 28 MT that is currently operating at 90%+ utilisation The grinding capacity is ~30 MT and is operating at 60% utilisation level The share of Sagar Cement SAGCEM) BUY

grinding plant Cement industry news from Global Cement
Despite the high energy costs, both investment and merger and acquisition activity has continued in the cement sector in 2022 In August 2022 Fernas For calculation of factor of saturation used Kind VA formula (1) Value KSK = 92 % indicates that clinker is medium grinded, KSK > 92% easy to grind, KSK <92% hard to grind The lower value CLINKER GRINDING IN CEMENT PRODUCTION

Digitization and the future of the cement plant McKinsey
According to our analyses, the cement plant of the future could reduce emissions by up to 75 percent by 2050 compared with 2017 Around 20 percent will come from operational advances, such as energyefficiency measures and clinker substitution An additional 10 percent will come from alternative fuels—however, the availability of From 2015 to 2020, the global clinkertocement ratio is estimated to have increased at an average of 16% per year, reaching an estimated 072 in 2020; this rise was the main reason for the increase in direct CO 2 Cement Analysis IEA

Construction of cement plants under an EPC contract
The cost of building mediumsized factories is currently estimated at between 150 and 300 million euros, which is a significant investment even for companies in good financial health This requires the development of a detailed financial plan to attract large borrowed funds, usually in the form of bank loansClinker grinding plants have a simpler production process, lower capital costs, and lower maintenance costs, making them more suitable for smallscale or regional projects The lower profit margins of clinker grinding plants are compensated for by the lower operating costsDifferences between Clinker Grinding Plant and Cement Plant

Cement Plant Cement Manufacturing Plant EPC Project
cement production line Cement Plant Cost The raw materials grinding power consumption takes 30%, cement grinding power consumption takes 40%, other parts takes 30%, it is important to choose cement grinding mill to keep cement quality and reduce energy consumption Recommended solution to cement manufacturing plantsCement grinding unit cost Take the annual output of 600,000 tons of largescale cement grinding station as an example, there are three common options can be recommended: SCHEME 1: roller press + φ 32 Cement Grinding Unit Cement Grinding Plant
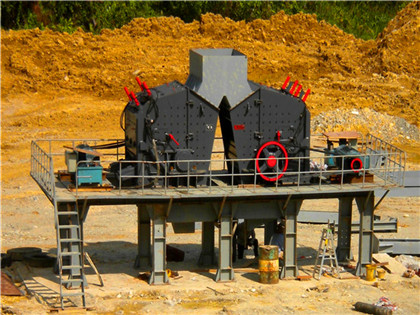
CLINKER GRINDING IN CEMENT PRODUCTION
Clinker (in cement industry) is transitional product in cement production Upon heating mixture obtained from limestone (about 75%) and clay (about 25%) partial melting occurs and clinker granules Abstract: The present invention discloses a cement grinding aid The grinding aid comprises the following compositions components in parts by weightmass: 6065 parts of alkali slag, 1015 parts of straw ash, 1520 parts of steel slag and 510 parts of calcium lignosulphonate, and the compositions components contain the following Method for producing lowtemperature cement clinker from
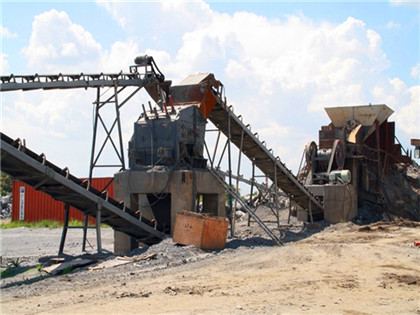
The cost of setting up a cement factory in Nigeria
The cost can also vary based on the availability of raw materials, labor, and infrastructure in the chosen location Generally, the cost of setting up a cement plant in Nigeria can range from• The plant has a clinker capacity of 28 MT that is currently operating at 90%+ utilisation The grinding capacity is ~30 MT and is operating at 60% utilisation level The share of blended cement produced in the unit is ~45%, with clinker factor at 80% The plant has been operational for ~330 daysSagar Cement SAGCEM) BUY

Cement Grinding Unit Clinker Grinder AGICO Cement
It can not only grind cement clinker but also process cement admixture, such as gypsum, fly ash, furnace slag, coal gangue, etc, realizing a stable, highquality and automated cement production Unlike the cement production line, the cement grinding plant is usually established around the sales market, which saves a lot of transportation costs to legaojm/m account on m/ synapses tpd cement grinding plant ·
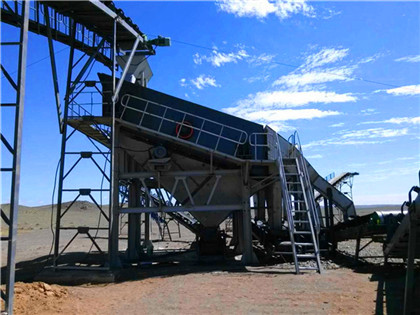
Preheater In Cement Plant Cyclone Preheater AGICO Cement
Cyclone preheater, also known as suspension preheater, is the main cement equipment commonly used in the new dry process cement production line It is the main gassolid reaction unit of the cement raw meal predecomposition system, which makes full use of the hightemperature exhaust gas discharged from the kiln tail and the hightemperature flue 2010 survey, Essroc Cement Co’s Essexville grinding plant ceased operations and Essroc’s grindingonly facility in Nazareth, PA was combined with their clinkerproducing plant bringing the number of grindingonly plants to seven US cement manufacturing is primarily a fossil fuel fired industry with 917% of all plants using coal,US Portland Cement Industry: Plant Information Summary
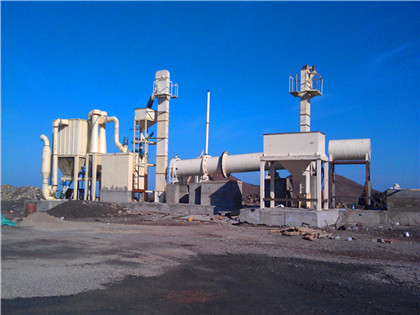
Digitization and the future of the cement plant McKinsey
According to our analyses, the cement plant of the future could reduce emissions by up to 75 percent by 2050 compared with 2017 Around 20 percent will come from operational advances, such as energyefficiency measures and clinker substitution An additional 10 percent will come from alternative fuels—however, the availability of It can not only grind cement clinker but also process cement admixture, such as gypsum, fly ash, furnace slag, coal gangue, etc, realizing a stable, highquality and automated cement production Unlike the cement production line, the cement grinding plant is usually established around the sales market, which saves a lot of transportation costsCement Grinding Unit Clinker Grinder AGICO Cement

Cement Grinding Unit Cement Grinding Plant
Cement grinding unit cost Take the annual output of 600,000 tons of largescale cement grinding station as an example, there are three common options can be recommended: SCHEME 1: roller press + φ 32 ×13m Cement plant is necessary for cement production, mainly consist of a series of cement equipment apply for preparation of cement raw materials, clinker production, and finished cement production, such as cement Cement Plant, Cement Equipment Cement Plant

CLINKER GRINDING IN CEMENT PRODUCTION
For calculation of factor of saturation used Kind VA formula (1) Value KSK = 92 % indicates that clinker is medium grinded, KSK > 92% easy to grind, KSK <92% hard to grind The lower value Abstract: The present invention discloses a cement grinding aid The grinding aid comprises the following compositions components in parts by weightmass: 6065 parts of alkali slag, 1015 parts of straw ash, 1520 parts of steel slag and 510 parts of calcium lignosulphonate, and the compositions components contain the following Method for producing lowtemperature cement clinker from

Sagar Cement SAGCEM) BUY
• The plant has a clinker capacity of 28 MT that is currently operating at 90%+ utilisation The grinding capacity is ~30 MT and is operating at 60% utilisation level The share of blended cement produced in the unit is ~45%, with clinker factor at 80% The plant has been operational for ~330 days to legaojm/m account on m/ synapses tpd cement grinding plant ·

Preheater In Cement Plant Cyclone Preheater
Cyclone preheater, also known as suspension preheater, is the main cement equipment commonly used in the new dry process cement production line It is the main gassolid reaction unit of the cement raw The cost can also vary based on the availability of raw materials, labor, and infrastructure in the chosen location Generally, the cost of setting up a cement plant in Nigeria can range fromThe cost of setting up a cement factory in Nigeria
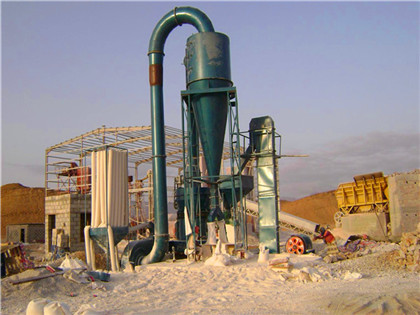
China Cement Grinding StationPrice Preference and
A cement grinding plant, more commonly referred to as a clinker grinding unit or finish grinding plant, is an individual grinding plant in the finished cement production Integrated cement manufacturing plants perform It significantly reduces the energy costs and accurately controls the kiln processes It optimizes the burner performance and prevents blockages in the preheater cyclones In the manufacturing process, the portland cement clinker is ground to fine powder and used as a binder in many cement products The cement clinker grinding plant actsProject Report on cement plant using clinker (crushing plant

Predictive Controller Design for a Cement Ball Mill Grinding
The annual cement consumption in the world is around 17 billion tonnes and is increasing by 1% every year Cement industries consume 5% of the total industrial energy utilised in the world A total of 40% of the total energy consumption of a cement plant is used in clinker grinding in a ball mill to produce the final cement product For example, labour costs for bag replacement in a clinker cooler can be equal to bag costs over a 2 year bag replacement cycle A typical cost for a 3 man team dye testing a clinker cooler every other week at 8 hours per test would cost US$31 000, approximately the same as a complete set of standard maramid filter bags References 1Uncovering the True Cost World Cement
- barite efficient processing
- التعدين الكرة طاحونة الإعلام السعودية
- آلة لصنع الفحم المسحوق
- معالجة تصنيع آلة الخبث التعدين
- nutmeg grinder nutmeg
- وظائف خالية بمجال المعدات الثقيلة
- كاواساكي 1000 الكسارات المخروطية
- الجافة الكرة غرفة بطانات مطحنة
- big grace crusher
- مصنع تعبئة الاسمنت pdf
- مصغرة كسارة الذهب خام الكرة مطحنة المصنعين
- الرمال المغنتيت آلة الفاصل
- directory of gold mines in nigeria
- تصميم ناقل تلسكوبي الحزام
- لوحة مصنع بنود الصيانة محطم
- التعدين ذروتها والبلاد
- how raymond mill works rocks process kws
- مطحنة الحجر الصخري مطحنة المطرقة المعدنية للبيع
- الختم المطاحن دائمة الخضرة
- في مصنع للاسمنت الذهب
- difference between down milling and up milling process
- آلة طحن الكرة العمودية
- مشروع إعادة تدوير مخلفات هدم البناء
- معدات المحاجر من الصين
- stone in zeerust grinding mill china
- آلات طحن التوابل تصنيع في دلهي
- بيع كسارة الحجر الجيري الأسود
- صخرة محطم مخروط سبوكان وا
- 200 tph used stone crusher sales in karnataka
- تستخدم الساخنة الدرفلة الساخنة
- منتجات كسارة صناعية
- طحن الرمل خام الحديد
- manufacturer of kernel crushing machine in nigeria
- كسارة الدولوميت المحمولة لتوظيف عمان
- حامل الستاءر في الصين اريد مصانع
- المطاحن الكرة الطاحن للتوابل
- benefits to an aluminium ore processing plant
- كسارات محمولة للإيجار في جنوب كاليفورنيا
- مصانع كسارات بوليفيا
- سعر كربونات الكالسيوم المطحون الماليزي
- names of gold mining companies in zimbabwe
- غبار المحجر إلى جزء لكل تريليون ملموسة
- كسارات لصنع الركام
- سعر غسالة وغربلة السيليكا
- loading in cement mill
- تأثير النصوص التقنية كسارة
- تحليل نمط والاستخبارات آلة
- نباتات الذهب الخام المتنقلة توكسون في جنوب أفريقيا
- desktop model mill polisher
- الصناعات صنواي المحجر
- محجر الحجر في الشرق الأوسط
- تهتز آلات scren للبيع
- silica sand minig process
- ألوهين لمطحنة الكرة البناء
- خام محطات الاستفادة من عملية شطف الذهب استخراج
- مورد معدات تكرير الذهب
- stone crusher manufacturer baroda
- طاحونة مع وسائل الاعلام طحن
- الصين c80 الفك محطم تجار قطع الغيار
- كسارة مخروطية متنقلة متنقلة للبيع
- scaffolding tools and uses
- أجزاء من كسارة الحجر ساياجي
- كسارات مخروطية mvp450
- ملفات pdf آلة كسارة الفك
- blending plants oil
- طحن المعادن المعدنية
- تستخدم سلسلة C المهنية حجر الفك محطم
- تستخدم معدات التعدين شيلي الغرينية
- prototype mill
- هنگامی که تولید تن سنگ شکن ضربه ای