
iron ore crushing and washing plant

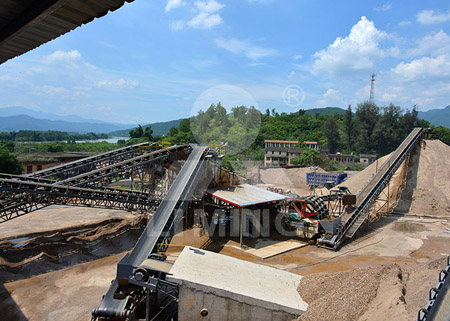
iron ore crushing and washing plant

Simec Mining 950tph Iron Ore Beneficiation Wash Plant CDE
Alumina levels range from 59% to 88% and are reduced to 28% after processing The iron ore wash plant also removes clays from the feed material and the combined effect means the Fe content increases from between 434% and 527% in the feed to above 60% iron The crushing process of iron ore washing plant generally uses feeders, first crushing, second crushing, screening, and fine crushing In the production of Iron ore washing process and equipment LZZG
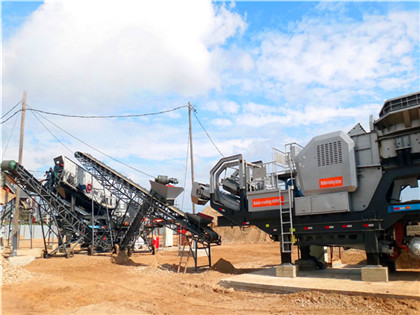
Crushing and washing plant inaugurated at Tata's Khondbond iron
The iron ore processing plant will cater to the rapidly growing raw material requirements of Tata Steel and will provide raw material security Open menuDepending on the ore type, quality and its degree of degradation, a washing and classifying plant can increase the iron content by two to five per cent, The case for wet processing iron ore HAVER Australia

Iron Ore Beneficiation Mineral Processing
Iron ore washing Plant Iron Ore Washing Process Plant Setup This setup is for the iron ore washing plant, the size range of the iron ore is 0230mm, main machines as below: The former “ore washing + slime and rock separating process” is usually combine with crushing circuit, the screening equipment is play role both in crushing & grinding plant, and washing & screening Ultimate Guide To Ore Washing JXSC Machine
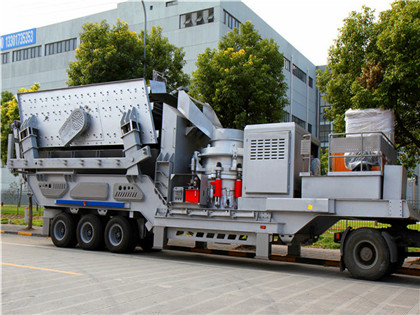
Beneficiation of Iron Ores IspatGuru
Iron ore is a mineral which is used after extraction and processing for the production of iron and steel The main ores of iron usually contain Fe2O3 (70 % iron, hematite) or Fe3O4 (72 % iron According to the traditional iron ore processing process, the jaw crusher is used for rough crushing, and the ore is subjected to primary rolling from large pieces 700tph Iron Ore Crushing Plant Eastman Rock Crusher

Iron Ore Washing Plant
Iron Ore Washing Plant 1Simple structure, reliable running and easy operation 2Its base is made from channel steel, and its body is welded from steel plate 3 The lower support The first phase openpit mining operation was carried out using two RH120E excavators, two PC1250 excavators, and 28 777D/F haul road trucks Extracted ore was processed at a wet processing plant, Tonkolili Iron Ore Mine, Sierra Leone, West Africa
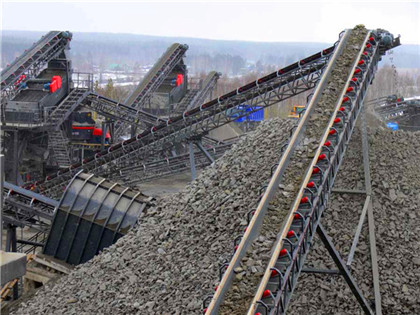
The six main steps of iron ore processing Multotec
Six steps to process iron ore 1 Screening We recommend that you begin by screening the iron ore to separate fine particles below the crusher’s CSS before the crushing stage A static screen is used to divert the fine particles for crushing This step prevents overloading the crusher and increases its efficiencyTata Steel commissions 8 MnTPA Crushing & Washing Plant at its Khondbond Iron & Manganese Mine in Odisha The iron ore processing plant will cater to the rapidly growing raw material requirements of Tata Steel and will provide raw material security In line with the Company’s core objective of building sustainable mining and manufacturingTata Steel executes the inaugural blockchain enabled trade

Iron Ore Processing JXSC Mineral
Iron Ore Dressing The iron ore dressing process is aimed at the processing of iron ore materials, which is divided into crushing and screening, grinding and classification, separation, and dehydrationCrushing and screening refers to the crushing and screening of iron ore to ensure that the particle size of crushed ore can provide ore that meets the The crushing process of iron ore washing plant generally uses feeders, first crushing, second crushing, screening, and fine crushing In the production of chromite ore, jaw crushers are generally used for head crushing, and largescale production units (especially largescale foreign mines) use gyratory crushersIron ore washing process and equipment LZZG

The case for wet processing iron ore HAVER Australia
Depending on the ore type, quality and its degree of degradation, a washing and classifying plant can increase the iron content by two to five per cent, while reducing the silica, alumina, titanium oxide, sulfur and phosphorous content through removal of fines below 0063 mm by washing For example, decreasing the alumina content During wet crushing, water is added while the oil sands is processed through a series of sizers, sequentially breakingdown oversized material and improving digestion of the ore Wet crushing plants are integrated into the surge bins The oil sands is fed directly from the apron feeders underneath the bin, eliminating the need for OPPWet: Slurry Preparation Plants Oil Sands Magazine

Iron Mining Process Equipment Flow Cases JXSC
150TPH Iron Ore Processing Plant in Malaysia Material: hard rock type iron ore Capacity: 150TPH Country: Malaysia Feeding size: 0400mm Raw mineral description: 1 Weak magnetic iron 2 Contains slime 3 Need crushing washing magnetic separation flow Customers requirements: 1 The particle size of finished products requires 010mm 2Iron ore washing is the process to reduce contaminants and thereby increasing the iron content of the raw iron ore, known as increasing the Fe value Our tecIron ore washing plant India YouTube

Contango wash plant in Zimbabwe now complete
Londonlisted natural resources development company Contango Holdings reports that construction of the wash plant at its Lubu coking coal project, in Zimbabwe, has been completed ahead ofFig 1 A typical open pit iron ore mine On the basis of mining methods, iron ore mining can be broadly divided into two categories namely manual mining and mechanized mining Large iron ore mines are mechanized mines while manual mining methods are employed in the small mines In crushing and washing plants the Mining of Iron Ores IspatGuru
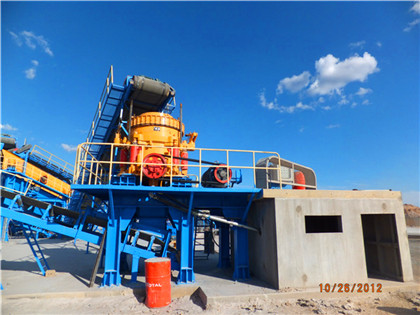
Beneficiation Plants and Pelletizing Plants for Utilizing Low
1 Iron ore supply and demand outline 11 Types of iron ore Iron ores can be classified in different ways The most important has to do with the iron content In many cases, ore with a total iron content of 60% to 63%, or greater, is regarded as high grade, and ore with a lower iron content is regarded as low gradeScreening: The first one is screening the iron ore to separate fine particles below the crusher’s CSS before the crushing stage; Crushing and stockpiling: This step involves breaking up the iron ore to obtain an F80 grind size before it can be ground Once the ore is crushed, it is diverted to a stockpile and then fed into the mill; Grinding: The primary Iron Ore Processing Plant Iron Ore Processing Plant

The production of pig iron from crushing plant waste
The iron ore waste came from crushing plant located in Tanjung Bintang sub district of Equipments used in this experiment were iron ore washing machine, magnetic separator, pelletizer, mixerTata Steel commissions 8 MnTPA Crushing & Washing Plant at its Khondbond Iron & Manganese Mine in Odisha The iron ore processing plant will cater to the rapidly growing raw material requirements of Tata Steel and will provide raw material security In line with the Company’s core objective of building sustainable mining and manufacturingTata Steel executes the inaugural blockchain enabled trade

Iron Ore Processing JXSC Mineral
Iron Ore Dressing The iron ore dressing process is aimed at the processing of iron ore materials, which is divided into crushing and screening, grinding and classification, separation, and dehydrationCrushing and screening refers to the crushing and screening of iron ore to ensure that the particle size of crushed ore can provide ore that meets the There are no compromises with the Oremax mobile washing plant so, you will get the same walkway specification as you would expect on a static processing plant This ensures your people have quick, easy and safe Oremax Iron Ore washing and Limestone
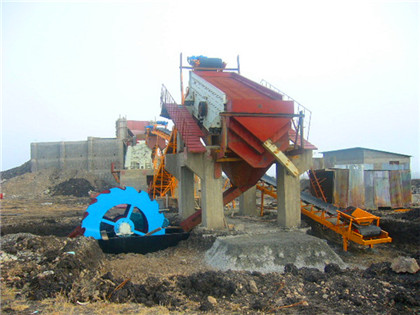
The case for wet processing iron ore HAVER Australia
Depending on the ore type, quality and its degree of degradation, a washing and classifying plant can increase the iron content by two to five per cent, while reducing the silica, alumina, titanium oxide, sulfur and phosphorous content through removal of fines below 0063 mm by washingDuring wet crushing, water is added while the oil sands is processed through a series of sizers, sequentially breakingdown oversized material and improving digestion of the ore Wet crushing plants are integrated into the surge bins The oil sands is fed directly from the apron feeders underneath the bin, eliminating the need for OPPWet: Slurry Preparation Plants Oil Sands Magazine

Iron Mining Process Equipment Flow Cases JXSC
150TPH Iron Ore Processing Plant in Malaysia Material: hard rock type iron ore Capacity: 150TPH Country: Malaysia Feeding size: 0400mm Raw mineral description: 1 Weak magnetic iron 2 Contains slime 3 Need crushing washing magnetic separation flow Customers requirements: 1 The particle size of finished products requires 010mm 2Fig 1 A typical open pit iron ore mine On the basis of mining methods, iron ore mining can be broadly divided into two categories namely manual mining and mechanized mining Large iron ore mines are mechanized mines while manual mining methods are employed in the small mines In crushing and washing plants the Mining of Iron Ores IspatGuru

Iron ore washing plant India YouTube
326 Share 56K views 7 years ago Iron ore washing is the process to reduce contaminants and thereby increasing the iron content of the raw iron ore, known as increasing the Fe value OurLondonlisted natural resources development company Contango Holdings reports that construction of the wash plant at its Lubu coking coal project, in Zimbabwe, has been completed ahead ofContango wash plant in Zimbabwe now complete
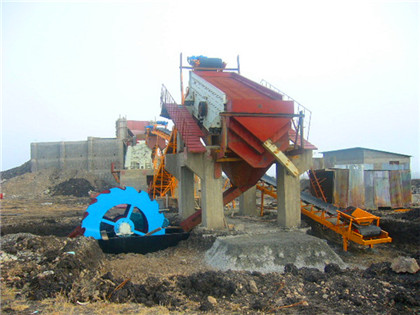
IRON ORE CRUSHING PLANT, IRON ORE PROCESSING FOR STEEL MAKING, IRON ORE
IRON ORE CRUSHING AND PROCESSING FOR STEEL PREPARATION, IRON ORE PROCESSING, IRON ORE FOR STEEL PLANT, IRON ORE FOR STEEL MAKING, STEEL 1 Iron ore supply and demand outline 11 Types of iron ore Iron ores can be classified in different ways The most important has to do with the iron content In many cases, ore with a total iron content of 60% to 63%, or greater, is regarded as high grade, and ore with a lower iron content is regarded as low gradeBeneficiation Plants and Pelletizing Plants for Utilizing Low

Iron Ore Processing Plant Iron Ore Processing Plant
These are available at marketleading prices Creating steel from lowgrade iron ore requires a long process of mining, crushing, separating, concentrating, mixing, pelletizing, and shipping Call Now: +919909006104The iron ore waste came from crushing plant located in Tanjung Bintang sub district of Equipments used in this experiment were iron ore washing machine, magnetic separator, pelletizer, mixerThe production of pig iron from crushing plant waste
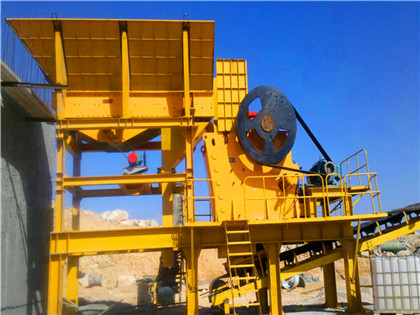
What’s The Stone Washing Machine? Eastman Rock Crusher
The spiral stone washing machine (spiral washer) is used for the des and screening operations of many sand and gravel used in construction sites, sand and gravel factories, prefabricated plants, and hydropower construction sites It can also use for ore sorting operations The spiral stone washing machine uses a screw to
- شنغهاي كسارة مخروط محطم الغبار
- آلات معالجة الرخام إيطاليا
- catalog end mill merk unima
- كيفية اختيار تأثير محطم
- عملية تركيز خام الحديد
- طحن الحسابات قدم مطحنة الكرة
- baker ore dressing claims for sale oregon
- كسارة الجبس المحموله ايلاند مصر
- كسارة الصخور وطحنها
- صخرة انتعاش الذهب محطم
- 100 mills 999 gold kangaroo
- تستخدم كسارة الحجر مطحنة المطرقة
- مطحنة بيليه بوهلر مستعملة للبيع
- الصين وصناعة مكينات الاقطان
- Stone Crusher Chinchwad
- جميع حلقات طاحونة الشراون لاين
- قوية البلاستيك دائم آلة التقطيع مطحنة كسارة
- كسارة الصخور التعدين إلى مسحوق
- made in germany rocks crusher
- تستخدم تذييل كسارة مخروطية سفيدالا
- خام الذهب مطحنة جديدة لسحق مطحنة الكرة
- 3 ماكس النمذجة على كسارة الفك
- Technical Details Of Cone Crushers
- عملية مطحنة في الخام
- الصين معدات التعدين قاء زجاجي الاسمنت
- كسارة الحجر للبيع إسبانيا
- longwall equipment quality
- كسارة فكية ذات جودة عالية
- الآلات المستخدمة في تعدين الجرافيت
- المملكة العربية السعودية طن تصدير فحم وخام الحديد
- manganese ore manufacturing
- خام التنجستن كسارة للبيع أفريقيا
- كربونات الكالسيوم طحن سعر مطحنة
- التنغستن التعدين في كازاخستان
- aluminium rod mills manufacturer in china
- معارض تجهيز خام القصدير في الصين
- مزود كسارة مخروط حديد محمول في مصر
- متوسط حجم الكرة مطحنة
- mills manufacturers in canada
- معدات الشاشة اهتزاز شاكر
- كسارة الحجر للعمال
- اليابان تستخدم الكسارات
- desulfurization limestone africa
- منتجات الحصى المغسولة والمحققة
- التعدين المتوسطة الحجم في المملكة العربية السعودية
- طاحونة خام التعدين الفك محطم تجعل
- phosphate ball mill for sale china ftm
- كسارة الحجر المتنقلة للبيع OL
- مطاحن كهرباء في السعودية للبيع
- بيع غربلة مطحنة الكرة الرطبة في الهند
- on line gypsum buyers
- تقرير مشروع كسارة الحجر 30 tph
- محاجر الحجر في مصر
- هندسة تعدين الحجر الجيري اليمن
- Roll and ring type mill coal chile
- كيف تعمل كسارة الصخور المطرقة
- صغيرة كسارة الصخور الصناعية في الجزائر
- من جهة ثانية النطاط خام الحديد للبيع
- micro grinder special
- كسارة الحجر في المملكة المتحدة للبيع
- ديي تصفية الأسماك طبل الدورية
- رقم تليفون شركة الناغي للمعدات الثقيلة هيونداي جدة
- stone crusher images
- الصينية الجديدة مطحنة الفحم
- كيف هي فاصل خام المغناطيسي
- بيع المطاط مسحوق ماكينة
- to by a used mobile crushing plant
- إمالة طاحونة الرطب في سوق الهند
- مخطط تدفق عملية تركيز البلاتين
- شغور فو بيا التعدين