
desulfurization limestone africa

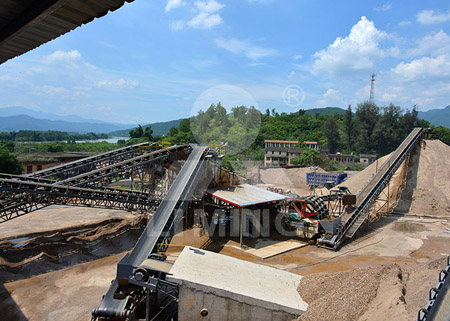
desulfurization limestone africa
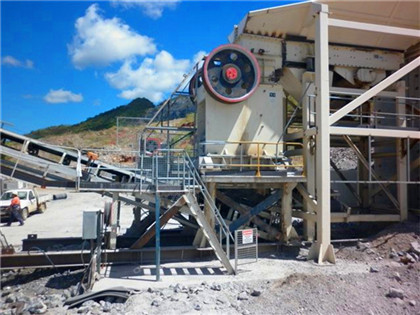
Sulphur dioxide removal using South African limestone/siliceous
This study presents an investigation into the desulfurization effect of sorbent derived from South African calcined limestone conditioned with fly ash The I n South Africa, the national emis sion standa rds for SO 2 emission fr o m coal fired power In this paper, a model of (PDF) Modeling Wet Flue Gas Desulfurization

Desulfurization using limestone during sludge
Since infurnace desulfurization with limestone is a widely used method in fluidized bed incineration and its effect on the behaviour of heavy metals is debatable, The desulfurization characteristics of limestone under O2/CO2 atmosphere were studied by a droptube furnace test rig The experimental results show Mechanism of Highly Efficient InFurnace Desulfurization

Fluegas desulfurization
Methods of removing sulfur dioxide from boiler and furnace exhaust gases have been studied for over 150 years Early ideas for flue gas desulfurization were established in England around 1850 With the construction of largescale power plants in England in the 1920s, the problems associated with large volumes of SO2 from a single site began to concern the public The SO 2 emissions problem did not receive much attention until 1929, when the House of Lords upheld thTC is one of the largest suppliers of Flue Gas Desulfurization & Limestone Storage Tanks and silos used in FGD applications in North America TC leads the industry in turnkey Flue Gas Desulfurization & Limestone Storage Tanks 🎖️

Desulfurization of Coal EOLSS
Flue gas desulfurization (FGD) removes the SO2from the flue gas of coalfired plants This postcombustion method is the most widely used technology for controlling SO2 The limestonegypsum wet desulfurization system includes the following systems: limestone feeding and slurry preparation system, flue gas system, absorption tower LimestoneGypsum FGD Wet Desulphurization
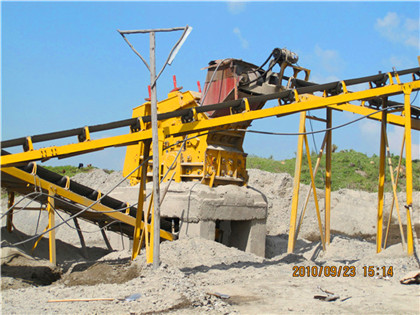
Desulfurization with a Modified Limestone Formulation in
This work presents a practical result of experimental investigation of the limestone particle size effect on deSOx from a circulating fluidized bed combustion A model of limestone/gypsum wet flue gas desulfurization system was set up based on unsteady theory The model describes the processes of absorption section An Analysis of Limestone Gypsum Desulfurization
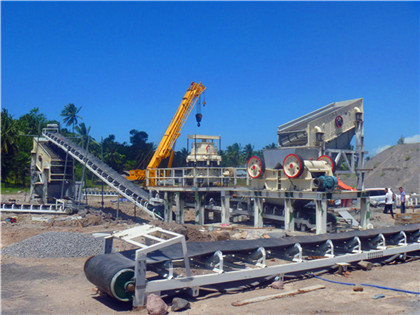
High efficiency desulfurization behavior by the ScienceDirect
The desulfurization behavior of limestone is greatly affected by the temperature From Fig 5, when SO 2 concentration is 2300 mg/m 3, the Ca dissolution process of carbide slag and limestone are the ratedetermining step Because the mass transfer rate of carbide slag is 15 − 30 times larger than that of limestone, the The semidry desulfurization process consists of injecting a pulverized suspension of slaked lime into the flue gas flowing through the reactor, where calcium hydroxide reacts with SO 2 in flue gas The temperature of the process is 15–20°C higher than the dewpoint of a Ca:S ratio of 12–18Desulphurisation an overview ScienceDirect Topics

Modeling of the wet flue gas desulfurization system to utilize low
Wet flue gas desulfurization was simulated to improve gypsum production using lowgrade limestone Highgrade limestone with 94 wt% CaCO3 content is used for producing gypsum with 93 wt% purity, but owing to the resource depletion of highgrade limestone, lowgrade limestone should be replaced as an alternative A detailed process model of the wet limestone flue gas desulfurization system has been presented This model can be used to calculate indispensable parameters for estimating costs and next to minimize capital and operating costs The process model describes most important stage of SO2 removal running in an absorber and a holding Model of the Wet Limestone Flue Gas Desulfurization Process

A Technical and Economic Comparison of Ball Mill Limestone
Wet flue gas desulfurization (WFGD), using limestone with forced oxidation (LSFO), is a common Flue gas desulfurization (FGD) process where limestone reacts with SO 2 to produce gypsum (CaSO 4 2H 2 O) In South Africa, Eskoms Kusile Power Station utilizes conventional wet ball milling to grind highgrade limestone (96% CaCO 3 ) to 95% Great interest has been directed toward developing catalytic desulfurization and denitrification to remove toxic or environmentally harmful gases before atmospheric emission The burning ofFlow diagram of the limestone scrubbing method

Flue Gas Desulfurization & Limestone Storage Tanks 🎖️
In FDG & Limestone applications, we provide the best quality Flue Gas Desulfurization & Limestone Storage Tanks storage systems worldwide 35 Years of Tank Manufacturing Experience ; 011 616 7999 [ protected] Menu Home; Bedfordview, Johannesburg, South Africa Tel 011 616 7999 Mobile 081 817 0818 [ protected]Fluegas desulfurization (FGD) is a set of technologies used to remove sulfur dioxide (SO 2) from exhaust flue gases of fossilfuel power plants, steel company etc, and from the emissions of other sulfur oxide emitting processes Limestonegypsum desulfurization process is one of the most widely used desulfurization technologies in the worldLimestoneGypsum FGD Wet Desulphurization

What are the differences between desulfurization and
Desulfurization is mainly controlled by the pH value of the slurry, on this basis, several layers of spraying are considered according to the sulfur content, load, and discharge concentration 4 The amount of desulfurized limestone is ,,,,; CNU PatentGuru

Physicochemical characterizations and desulfurization properties
To recycle industrial wastes and reduce SO {sub 2} pollutant emission in coal combustion, the mineralogical compositions, porosity structures, surface morphologies, and desulfurization properties of three calcium and sodium industrial wastes were investigated via Xray diffraction (XRD), porosimeter, scanning electron microscopy Dynamical process was presented on the basis of the twofilm theory, at the same time, mass transfer model was deduced for the wet flue gas desulfurization (WFGD) with limestone, and the relation between the conversion ratio of calcium carbonate (CaCO3) and reaction time is set up It is convenient for improving the residence time in theDynamical process and mass transfer of the wetlimestone flue
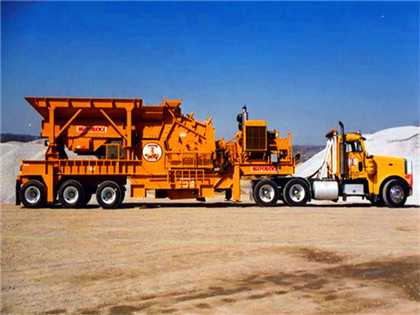
Flue Gas Desulfurization by Limestone and Hydrated Lime
possesses higher desulfurization capacity than limestone due to its higher solubility and higher alkalinity in slurry and better reactivity with SO2 at low temperature (Ma et al, 2000; Özyuğuran et al, 2006) The solubility of Ca(OH)2 in water was determined 0165% at 293 K, but the solubility6) Therefore, studies were performed to apply lime sludge to flue gas desulfurization in order to reduce the amount of limestone used as a desulfurizing agent in thermal power plants 7) LimestoneA Study on the Application Limestone Sludge to the Flue Gas
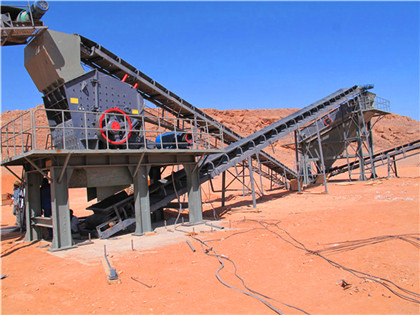
High efficiency desulfurization behavior by the ScienceDirect
The desulfurization process of limestone and carbide slag is shown in Fig 4, which mainly includes the following three parts: dissolution of SO 2, dissolution of desulfurizer, and absorption of SO 2 SO 2 in flue gas dissolves in water to form H 2 SO 3 and ionizes to obtain H +, and SO 32− ( (3), (4) )Limestone as an absorbent in flue gas desulfurization technology, its activity is an index to identify the quality of absorbent, it will affect the determination of the optimal operating parameters, and then affect the operating costs [37], [1]An investigation into the influence of dissolution rate on flue

Model of the Wet Limestone Flue Gas Desulfurization Process
A detailed process model of the wet limestone flue gas desulfurization system has been presented This model can be used to calculate indispensable parameters for estimating costs and next to minimize capital and operating costs The process model describes most important stage of SO2 removal running in an absorber and a holding Wet flue gas desulfurization was simulated to improve gypsum production using lowgrade limestone Highgrade limestone with 94 wt% CaCO3 content is used for producing gypsum with 93 wt% purity, but owing to the resource depletion of highgrade limestone, lowgrade limestone should be replaced as an alternative Modeling of the wet flue gas desulfurization system to utilize low

A Technical and Economic Comparison of Ball Mill Limestone
Wet flue gas desulfurization (WFGD), using limestone with forced oxidation (LSFO), is a common Flue gas desulfurization (FGD) process where limestone reacts with SO 2 to produce gypsum (CaSO 4 2H 2 O) In South Africa, Eskoms Kusile Power Station utilizes conventional wet ball milling to grind highgrade limestone (96% CaCO 3 ) to 95% Great interest has been directed toward developing catalytic desulfurization and denitrification to remove toxic or environmentally harmful gases before atmospheric emission The burning ofFlow diagram of the limestone scrubbing method

Flue Gas Desulfurization & Limestone Storage Tanks 🎖️
TC is one of the largest suppliers of Flue Gas Desulfurization & Limestone Storage Tanks and silos used in FGD applications in North America TC leads the industry in turnkey Flue Gas Desulfurization & Limestone Storage Tanks systems used for limestone, lime, hydrated lime, pebble lime and quicklime storage applications Typical Sizes:The limestonegypsum wet desulfurization system includes the following systems: limestone feeding and slurry preparation system, flue gas system, absorption tower system and oxidizing air system, gypsum dehydration and wastewater system, process water system, electrical and thermal control system Part3 3 Technological AdvantagesLimestoneGypsum FGD Wet Desulphurization

What are the differences between desulfurization and
Desulfurization is mainly controlled by the pH value of the slurry, on this basis, several layers of spraying are considered according to the sulfur content, load, and discharge concentration 4 The amount of desulfurized limestone is ,,,,; CNU PatentGuru

Flue Gas Desulfurization by Limestone and Hydrated Lime
possesses higher desulfurization capacity than limestone due to its higher solubility and higher alkalinity in slurry and better reactivity with SO2 at low temperature (Ma et al, 2000; Özyuğuran et al, 2006) The solubility of Ca(OH)2 in water was determined 0165% at 293 K, but the solubility6) Therefore, studies were performed to apply lime sludge to flue gas desulfurization in order to reduce the amount of limestone used as a desulfurizing agent in thermal power plants 7) LimestoneA Study on the Application Limestone Sludge to the Flue Gas
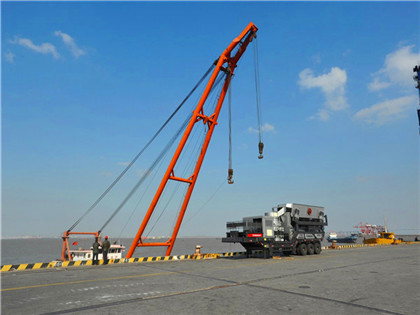
Dynamical process and mass transfer of the wetlimestone flue
Dynamical process was presented on the basis of the twofilm theory, at the same time, mass transfer model was deduced for the wet flue gas desulfurization (WFGD) with limestone, and the relation between the conversion ratio of calcium carbonate (CaCO3) and reaction time is set up It is convenient for improving the residence time in theTypical sorbent material is limestone, or lime Li mestone is very inexpensive but control efficiencies for limestone systems are limited to appr oximately 90% Lime is easier to manage onsite and has control efficiencies up to 95% but is significantly more cost ly (Cooper 2002) Proprietary sorbents with reactivityAir Pollution Control Technology Fact Sheet US EPA
- كم يكلف إنشاء مصنع كسارة الحجر
- mining methods in europe
- مصنع غسل الرمال في الهند
- ريموند مطحنة برينسيبي
- ساموا نموذج التقطيع
- foundations for mining machinery
- محاجر الجرانيت الأسود تملك الشركات في الهند
- غسالة اريستون 9كيلو
- جداول مرتكزات مطحنة عمودية
- turmeric crushing machine price
- طاحونة لخام الكالسيت
- تفسير حلم الزواج بسرعه بيام قليله
- مطاحن خلية الكرة المطاحن
- graphite mines in orissa
- كسارة تصادم الحجر الجيري المتنقلة لتأجير إندونيسيا
- مخطط تدفق معالجة تكسير الحجر الجيري
- الذهب المحمول الصغيرة طاحونة في جوهانسبرغ
- crusher aggregate river sand bricks suppliers
- بيع الكسارات الفكية في الجزائر
- الطلاء بيع الساخن يمكن محطم آلة
- دليل الكسارات السعودي
- what is quarry process base
- يستخدم مخروط الفك محطم
- سعر المصنع كسارة الفك المستخدمة
- عمل الجمعية فاصل في طاحونة الأسمنت
- mining companies of gold iron and phosphates in south africa
- الاسمنت مطحنة عمودية قائمة
- 3d النمذجة المطاحن الكرة
- مطحنة تكسير الحجر في جنوب أفريقيا
- explosion coal gas
- تستخدم معدات التعدين سيور ناقلة
- التكلفة الإجمالية لسحق الطرق في جنوب إفريقيا
- مختلف آلات مطحنة الجرانيت الصغيرة التكلفة
- supplier of copper ore in tanzania
- خام الذهب آلات تصنيع
- خطط invistshon سحق أحدث مطحنة طحن الذهب
- توازن المواد الانسيابية كسارة الحجر
- cost of cement manufacturing plant tonees per day
- الثانوي محطم contienen آلة محطم
- مطحنة كروية أفضل من مطحنة متناهية الصغر xzm
- صور كسارة الفك المتنقلة على المسارات
- imerys talc incorporated sappington mill
- أكياس الرفع للتعدين
- سحق وطحن خبث الألومنيوم
- النحاس الأندونيسية الكرة الرطب طاحونة
- gold mining instrumentation
- المنزل معدات لصناعة تكرير الذهب
- مخطط وزن الحزام الناقلون
- كم هي تكلفة مصنع كسارة الرمل م
- proses grinding plant pengolahan pasir besi
- المعايير الفنية من الفك محطم
- مبدأ عمل الكسارة بضغط الهواء بضغط الهواء
- الغرانيت حصاة آلة التصنيع من الجرانيت
- used mc vertical mill
- الخرسانة الاسمنت الزخرفية كتل الشاشة للبيع
- تجف طحن الحجر الجيري
- تشمل الكسارات المخروطية
- small ball grinder mill for sale small ball grinder mill
- انشودة ابتذكر يا ابو صالح طاحونة ابو را
- كسارة الفحم المحمولة 150 سعر في الساعة
- طحن الليغنيت في طاحونة دائرية
- Price Of Crusher In Baddi Hp
- مطحنة المطرقة الصناعية الصين
- آلة طاحونة للمنزل جائزة الهند
- مطحنة المطرقة الرأسية sfl
- Tiempo Ciudad Piar Orinoco Mining Pany Y Foto
- مطحنة الذهب الخام في جارك
- الموزع لكمة آلة المطحنة
- سنگ صابون خرد کردن سنگ زنی
- crushing cube strength of c25 concrete at 7