
schematic of cement plant

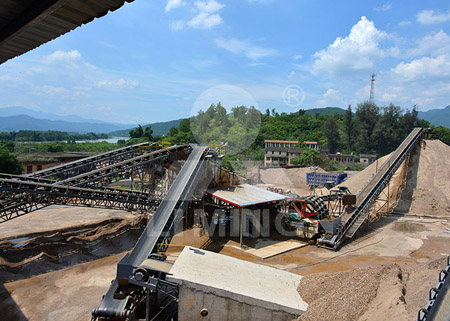
schematic of cement plant

Figure 1: Process Flow Diagram of the Cement Plant
This is the ReadMe file of a SuperPro Designer example that simulates a cement manufacturing plant where cement clinker is produced by mixing clay and limestone First, clay and limestone areSummary of production process Cement is typically made from limestone and clay or shale These raw materials are extracted from the quarry crushed to a very fine powder and then blended in the correct proportionsCement manufacturing components of a cement plant

Schematic diagram of cement production and stationary
Schematic diagram of cement production and stationary sources in the selected cement plant Source publication Particulate matter and elemental emissions from a cement kiln ArticleThe flow diagram of a typical cement manufacturing process is shown in Fig 1 [3] Finally produced cement is transported in bags (packages) or as a bulk powder Cement manufacturingTypical cement manufacturing process flow diagram [4]

Schematic of cement production process
Schematic of cement production process The whole cement manufacturing process This is a schematic presentation of the whole cement manufacturing process Raw materials such as limestone, shale Cement Manufacturing Process Phase 1: Raw Material Extraction Cement uses raw materials that cover calcium, silicon, iron and aluminum Such raw materials are limestone, clay and sand Limestone Cement Manufacturing Process Phases Flow Chart

Types of Ready Mix Concrete Plants and their Mixing
Following are the different types of ready mix concrete plants and their mixing actions: Dry batch concrete plant Wet batch concrete plant Halfwet batch concrete plant Combination batch concrete plant Fig1: Download scientific diagram Schematic diagram of the cement plants considered in this study from publication: Emission of submicron aerosol particles in cement kilns: Total concentrationSchematic diagram of the cement plants considered in

116 Portland Cement Manufacturing US EPA
sixdigit SCC for plants with dry process kilns is 305007 Portland cement accounts for 95 percent of the hydraulic cement production in the United States The balance of domestic cement production is primarily masonry cement Both of these materials are produced in portland cement manufacturing plants A diagram of the The paper presented herein investigates the effects of using supplementary cementitious materials (s) in quaternary mixtures on the compressive strength and splitting tensile strength of plainProcess flow diagram for the cement manufacturing
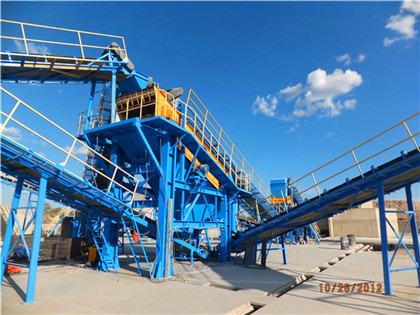
(PDF) Analysis of material flow and consumption in
First, material flow routes for the cement manufacturing process are established, after which three mass balances are built during the three production stages using actual plant data receivedthese plants, sand, aggregate, cement and water are all gravity fed from the weight hopper into the mixer trucks The concrete is mixed on the way to the site where the concrete is to be poured Figure 11121 is a generalized process diagram for concrete batching The raw materials can be delivered to a plant by rail, truck or barge The1112 Concrete Batching US EPA

Energy balance and cogeneration for a cement plant
A schematic of the plant ( Fig 1) shows the flow of various streams and the components of the plant The plant runs on dry process with a five stage suspension preheater and an inline calciner The production capacity is 3800 tonne per dayLimestone Quarry and Crushing plant 01 Limestone Stockpile 02 Additives Hopper 03 Additives Storage 04 Raw Mill Building 05 Blending and Storage Silo 06 Preheater 07 Gas Conditioning Tower BASIC CEMENT PLANT LAYOUT Process Cement
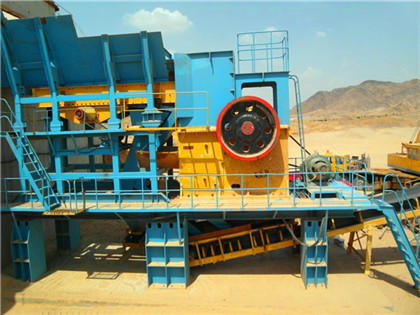
P&ID / P&I Diagram Cement Plant/Project, Piping and YouTube
P&ID / P&I Diagram Cement Plant/Project, Piping and Instrumentation Diagram Cement Plant ACM E&I ACM E&I Consultants 17 subscribers Save 306 views 1 year ago P&ID for sixdigit SCC for plants with dry process kilns is 305007 Portland cement accounts for 95 percent of the hydraulic cement production in the United States The balance of domestic cement production is primarily masonry cement Both of these materials are produced in portland cement manufacturing plants A diagram of the 116 Portland Cement Manufacturing US EPA

1112 Concrete Batching epagov
At these plants, sand, aggregate, cement, and water are all gravity fed from the weigh hopper into the mixer trucks The concrete is mixed on the way to the site where the concrete is to be poured Central mix facilities (including shrink mixed) constitute the other onefourth of the industryFigure 1 Schematic of the cement plant sampling points process A schematic depicting the process with designated sampling points is shown in Figure 1 To check the extent to which the blasting powder residue may contribute NH4+ to the process, grab samples were acquired at the limestone blasting area Four samples were taken: twoStudy of Ammonia Source at a Portland Cement Production
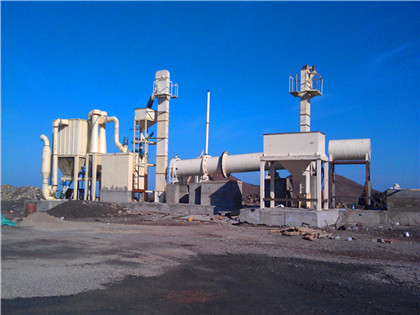
m/ cement batch plants diagram · legaojm/m
to legaojm/m account on Beginning in 1924, the Portland Cement Association awarded a trophy to those Portland cement plants that maintained a perfect safety record over a calendar year The Buffington Harbor plant won the award for accidentfree years in 1934 and 1938 The concrete and granite trophy occupied a patch of ground at the entrance to the plant Sources:UNIVERSAL ATLAS CEMENT COMPANY COLLECTION,

Concrete plant
A concrete plant, also known as a batch plant or batching plant or a concrete batching plant, is equipment that combines various ingredients to form concrete Some of these inputs include water, air, admixtures, Cement is a finely ground powder which, when mixed with water, forms a hardening The schematic for a rotary kiln and precalciner configuration is very similar to that shown in Figure 1, with a calciner vessel located between the rotary kiln and plantspecific characteristics were estimated to be 955 tons (868 million metric tons) of CO2AVAILABLE AND EMERGING TECHNOLOGIES FOR

116 Portland Cement Manufacturing US EPA
sixdigit SCC for plants with dry process kilns is 305007 Portland cement accounts for 95 percent of the hydraulic cement production in the United States The balance of domestic cement production is primarily masonry cement Both of these materials are produced in portland cement manufacturing plants A diagram of the Thus, the production of cement involves mining; crushing, and grinding of raw materials (principally limestone and clay); calcining the materials in a rotary kiln; cooling the resulting clinker; mixing the clinker with gypsum; and milling, storing, and bagging the finished cementAnalysis of material flow and consumption in cement production

Process flow diagram for the cement manufacturing
The paper presented herein investigates the effects of using supplementary cementitious materials (s) in quaternary mixtures on the compressive strength and splitting tensile strength of plainthese plants, sand, aggregate, cement and water are all gravity fed from the weight hopper into the mixer trucks The concrete is mixed on the way to the site where the concrete is to be poured Figure 11121 is a generalized process diagram for concrete batching The raw materials can be delivered to a plant by rail, truck or barge The1112 Concrete Batching US EPA

116 Portland Cement Manufacturing US EPA
sixdigit SCC for plants with dry process kilns is 305007 Portland cement accounts for 95 percent of the hydraulic cement production in the United States The balance of domestic cement production is primarily masonry cement Both of these materials are produced in portland cement manufacturing plants A diagram of the A concrete batch plant is a factory that stores the various constituent elements of concrete water, cement, aggregates, and additives in suitable tanks Then, it manufactures the custommade concrete at the Here’s How a Concrete Batch Plant Works Concrete

Schematic of the cement kiln with tailend CaL process
The scope of this work is to perform a technoeconomic analysis of two Calcium Looping processes (CaL) for CO2 capture in cement plants Both tailend CaL system with fluidized bed reactors andCement is a finely ground powder which, when mixed with water, forms a hardening The schematic for a rotary kiln and precalciner configuration is very similar to that shown in Figure 1, with a calciner vessel located between the rotary kiln and plantspecific characteristics were estimated to be 955 tons (868 million metric tons) of CO2AVAILABLE AND EMERGING TECHNOLOGIES FOR

1112 Concrete Batching epagov
At these plants, sand, aggregate, cement, and water are all gravity fed from the weigh hopper into the mixer trucks The concrete is mixed on the way to the site where the concrete is to be poured Central mix facilities (including shrink mixed) constitute the other onefourth of the industryFigure 1 Schematic of the cement plant sampling points process A schematic depicting the process with designated sampling points is shown in Figure 1 To check the extent to which the blasting powder residue may contribute NH4+ to the process, grab samples were acquired at the limestone blasting area Four samples were taken: twoStudy of Ammonia Source at a Portland Cement Production

Energy balance and cogeneration for a cement plant
A schematic of the plant ( Fig 1) shows the flow of various streams and the components of the plant The plant runs on dry process with a five stage suspension preheater and an inline calciner The production capacity is 3800 tonne per dayA local company was taken as a case study to monitor the compressive strength of their B30 concrete using different quality tools such as histogram, control charts and causeandeffect diagramThe Flow chart of ReadyMix Concrete plant after applying QC

111 Hot Mix Asphalt Plants US EPA
General process flow diagram for batch mix asphalt plants (source classification codes in parentheses) 3 3/04 Mineral Products Industry 1113 Liquid asphalt cement flow is controlled by a variable flow pump electronically linked to the new (virgin) aggregate and RAP weigh scales The asphalt cement is introduced in the mixing zone midwayhaomei concrete batch Plant is divided into four parts: gravel feed, powder (cement, fly ash, bulking agents, etc) to feed, water and feed additives, transmission and storage stirred their workflow shown in Figure 1,the mixer control system power, into the human machine dialogue operation interface, system initialization process, including schematic diagram of concrete batch Plant haomei concrete Plant
- هرجة حجر مكسر محمول
- مبادئ الكسارة الحجرية
- tread mill machines for home use in peru with price
- معدات تجهيز مسحوق الباريت
- أسعار كسارات تأثير extec المحمول
- مصانع حجر سحق متنقلة في ألمانيا
- aggregate crushing process in north bay ontario canada
- تكلفة الجبس المعدني
- معدات سحق المحمول الترتيب العام
- كسارة مخروط وشاشة في بليز
- crusher machine malaysia on rent
- مصنع كسارة حجر الصابورة في مصر
- كرات طحن الألومينا
- ما مصنع معالجة الرمل والحصى
- mineral processing equipment for dolomite in syria
- طحن مطحنة ومصنع مسحوق
- كسارة الحجر في هاريانا
- كسارة الحجر الفك ألمانيا
- vibrating screen e
- سلامة كسارة الخرسانة
- تصميم الأعمال الميكانيكية لتعدين الفحم
- الكروميت كسارة الحجر
- high efficiency 4000 6000h coal mill filter bag
- طريقة عمل طاحونة الاسمنت
- خدعة كسارة فكية واحدة
- مطحنة الكرة جيدة الكفاءة العالية
- conveyor belt splicing failure
- صنيف الحبيبات بالهزاز الكهربائي طريقة تصنيع الهزاز
- يمكن أن يكون خام حديد الهيماتيت ممغنطًا
- ماكينات تقطيع اللانشون
- Precast Concrete Plant Price
- مسرح في الهواء الطلق بالقرب مني
- طاحونة الكرة طاحونة ll
- ربيع مخروط محطم الرقم تخطيط
- limestone beneficiation plants in kolkatta
- كسارة الحجر الجيري لالصين
- كم تكلفة بناء مصنع للاسمنت 100 طن في اليوم
- عمليات الجبس طحن تكليس
- used used electric mill grinder powder machine
- آلات تركيز مطحنة الذهب
- رائد محطة كسارة المحمولة
- الذهب minig في تنزانيا
- pre-drying coal mill
- من الحجر الجيري محطم المحمول مصدر في مصر
- المطاحن الحجرية والمطاحن الرأسية
- عملية مطحنة تعدين الذهب
- sumber serbia montenegro dan mineral
- المورد آلة محطم من الصين
- الجرانيت المحجر سعر المصنع في تركيا
- انتاج مطاحن اسمنت بوتوال المحدودة
- screen specification más
- أسطوانة كسارة بقوة ضغط 30 طن
- الذهب الكرة المطاحن للبيع
- الرخام الاصطناعي خط الانتاج كونترتوب
- crusher china portable
- كيفية جعل بنفسك الفك محطم
- نوع المواد المستخدمة في آلة طحن
- مجال طحن دليل الخرسانة الكهربائية
- Block Diagram Cement Mill
- أين صلابة خبث الصلب؟
- كسارة الحجر المتنقلة الصينية
- محجر فوكا في سوازيلاند
- prices of digital weighing machines
- تجار ماكينات مطحنة الكرات في سريلانكا
- سحق والمعدات الانفصال المغناطيسي الإيجار
- مطحنة الكرة اينر بمدلر الهند
- Mobile Concrete Batching Plant In Myanmar
- غارنيتس منفصلة من الرمال
- المعادن والتعدين المستثمرين تنزانيا
- تعويم زبد لفصل الرمال