
pre-drying coal mill

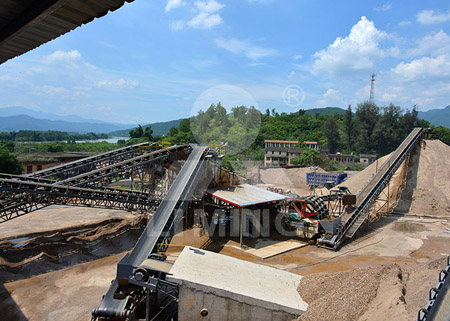
pre-drying coal mill

Predrying coal: technologies and economics
Predrying coal: technologies and economics Nigel Dong IEA Clean Coal Centre Webinar, 24 September 2014 Bituminous, including anthracite 45% Subbituminous 32% Lignite The lignite predrying process plays an important role in modern lignite power plants and the fluidized bed dryer with internal heat utilization is a promising A novel lignite predrying system with lowgrade heat

EPA1 Method for mill drying coal Google
The method according to the invention for mill drying coal comprises the following steps: a) predrying of the coal to a predefinable first moisture level in a predryer (2) and b)Having left the mill at the top, the final product continues with the gas to the filter or cyclone,where it is collected Tailormade layout The layout of your coal grinding system must ATOX coal mill

Coal Drying Improves Performance and Reduces
causes less feeder hopper bridging and plugging problems Coal feeders provide coal to the coal pulverizers (mills) where the coal is pulverized and dried Dryer coal is easier to Milling & Grinding Mills Custom designed solutions to meet your milling needs For decades, we have been making milling systems to meet specific customer needs We now offer a Dry milling machines Schenck Process
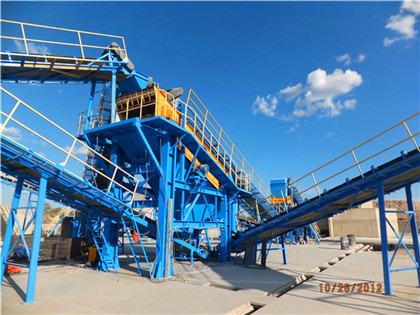
Thermodynamic analysis of predrying methods for pre
Wang [20] A fluidized bed coal drying system is experimentally investigated Dewatering Decrease of 38% in auxiliary power consumption by reducing the moisture Lignite is an important fuel for power generation in many parts of the world The major issue is that the high moisture content of lignite results in low thePredrying coal technologies and economics IEACCC

Coal Mill an overview ScienceDirect Topics
ObserverBased and Regression ModelBased Detection of Emerging Faults in Coal Mills Peter Fogh Odgaard, Sten Bay Jørgensen, in Fault Detection, Supervision and Safety The ball mill is a traditional coal pulverizer machine, which has been widely used since it was invented In the cement plant, the new dry process cement manufacturing requires Coal Mill in Cement Plant Vertical Roller Mill & Air

Predrying coal: technologies and economics
Predrying coal: technologies and economics Nigel Dong IEA Clean Coal Centre Webinar, 24 September 2014 Bituminous, including anthracite 45% Subbituminous 32% Lignite 23% Global proved recoverable coal reserves, 2011: 8915 Gt Low rank coal is abundant and reliable • Flash mill dryingA thermal energy storage concept based on lowrank coal predrying (LDTES) • Minimum load of coalfired power plants is significantly reduced by LDTES • Electric power is stored equivalently with high roundtrip efficiency (928%) • CO 2 emission of the power plant is significantly reduced by the adoption of LDTESA comprehensive analysis of a thermal energy storage

Coal Drying Improves Performance and Reduces Emissions
causes less feeder hopper bridging and plugging problems Coal feeders provide coal to the coal pulverizers (mills) where the coal is pulverized and dried Dryer coal is easier to pulverize, and less mill power is needed to achieve the same coal fineness Additionally, with less fuel moisture, more complete drying of coal can be achieved in theHaving left the mill at the top, the final product continues with the gas to the filter or cyclone,where it is collected Tailormade layout The layout of your coal grinding system must take into account the available heat sources for drying the raw coal as well as the fire and explosion hazards of coal and coal dust The entire grindingATOX coal mill
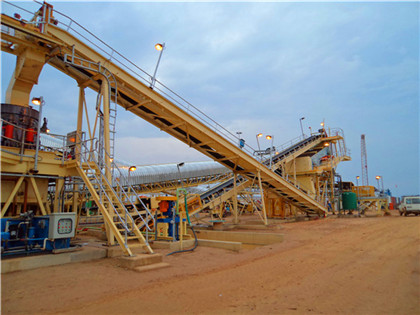
Dry milling machines Schenck Process
Milling & Grinding Mills Custom designed solutions to meet your milling needs For decades, we have been making milling systems to meet specific customer needs We now offer a wide range of technologies which we will customize to meet all your process and performance requirements Our mills are known for outstanding reliability in these sectors:Coal pulverizers are used to dry, grind and classify Drying is achieved as hot gas passes through the pulverizer and removes moisture from the pulverized coal The hot gases used should have a low oxygen content, Vertical Grinding Mill (Coal Pulverizer) Explained

Coal Mill an overview ScienceDirect Topics
ObserverBased and Regression ModelBased Detection of Emerging Faults in Coal Mills Peter Fogh Odgaard, Sten Bay Jørgensen, in Fault Detection, Supervision and Safety of Technical Processes 2006, 2007 52 Experiments with and design of the regression modelbased approach Operating data from a coal mill is used to compare the fault detection The ball mill is a traditional coal pulverizer machine, which has been widely used since it was invented In the cement plant, the new dry process cement manufacturing requires the moisture content of coal powder to be 05% ~ 15%, while that of raw coal is 15% ~ 40% Therefore, the ball mill should have a drying function besides grindingCoal Mill in Cement Plant Vertical Roller Mill & AirSwept Ball Mill

Vertical Coal Mill for Coal Grinding in Cement Plant
Vertical Coal Mill Feeding size: ≤110mm Capacity: 570t/h Motor power: 1101400kW Applications: Vertical coal mill is mainly used for grinding raw coal, bituminous coal, and other fuels into coal powder, which is 15 10Bowl Mill Bowl mills are employed to pulverize the precrushed raw coal to the required fineness before it is admitted into the boiler furnace for combustion The mill output can be easily varied, as Coal mill pulverizer in thermal power plants
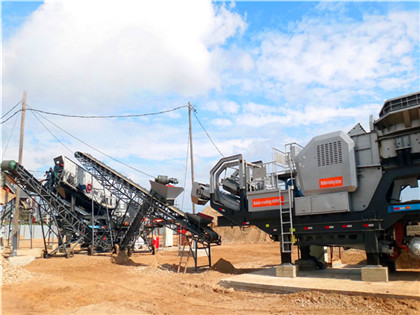
Coal PulverizerRaymond Mill
When the humidity of the raw coal is below 15%, the CLIRIK coal pulverizer is used to grind the raw coal into 200 meshes Fine powder, while eliminating the need for drying and saving energy The The effective parameters are evaluated in three categories as follows: (1) the parameters about the drying media (the type of the media, the temperature, the pressure, the velocity and the(PDF) Evaporative Drying of LowRank Coal ResearchGate

(PDF) Low Temperature Drying Process Improves Heat Rate and
Precombustion drying technologies can not only solve these problems, but also save water at wet scrubbers and cooling towers for a coal fired power plant, which is important for power plants3 Predrying on new build power plants 24 31 BoA Plus 24 32 700°C lignitefired power plant 27 33 Zero Emissions Platform cost study 30 331 Effects of predrying of lignite 33 332 Effects of CO 2 capture 34 333 Cost comparison between unabated hard coal, lignite and natural gas CCGT power plants 35Technoeconomics of modern predrying technologies for

Predrying coal: technologies and economics
Predrying coal: technologies and economics Nigel Dong IEA Clean Coal Centre Webinar, 24 September 2014 Bituminous, including anthracite 45% Subbituminous 32% Lignite 23% Global proved recoverable coal reserves, 2011: 8915 Gt Low rank coal is abundant and reliable • Flash mill dryingA thermal energy storage concept based on lowrank coal predrying (LDTES) • Minimum load of coalfired power plants is significantly reduced by LDTES • Electric power is stored equivalently with high roundtrip efficiency (928%) • CO 2 emission of the power plant is significantly reduced by the adoption of LDTESA comprehensive analysis of a thermal energy storage

(PDF) Evaporative Drying of LowRank Coal
The effective parameters are evaluated in three categories as follows: (1) the parameters about the drying media (the type of the media, the temperature, the pressure, the velocity and theHaving left the mill at the top, the final product continues with the gas to the filter or cyclone,where it is collected Tailormade layout The layout of your coal grinding system must take into account the available heat sources for drying the raw coal as well as the fire and explosion hazards of coal and coal dust The entire grindingATOX coal mill

Modified High BackPressure Heating System Integrated with Raw Coal Pre
A conceptual highback pressure (HBP) heating system cooperating raw coal predrying for combined heat and power (CHP) was proposed to improve the performance of the HBPCHP unit In the new design, besides of heating the supplywater of the heating network, a portion of the exhaust steam from the turbine is employed to causes less feeder hopper bridging and plugging problems Coal feeders provide coal to the coal pulverizers (mills) where the coal is pulverized and dried Dryer coal is easier to pulverize, and less mill power is needed to achieve the same coal fineness Additionally, with less fuel moisture, more complete drying of coal can be achieved in theCoal Drying Improves Performance and Reduces Emissions
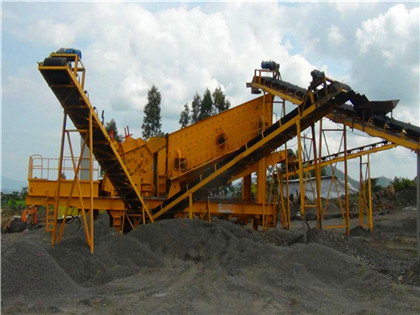
Coal Mill an overview ScienceDirect Topics
ObserverBased and Regression ModelBased Detection of Emerging Faults in Coal Mills Peter Fogh Odgaard, Sten Bay Jørgensen, in Fault Detection, Supervision and Safety of Technical Processes 2006, 2007 52 Experiments with and design of the regression modelbased approach Operating data from a coal mill is used to compare the fault detection 15 10Bowl Mill Bowl mills are employed to pulverize the precrushed raw coal to the required fineness before it is admitted into the boiler furnace for combustion The mill output can be easily varied, as Coal mill pulverizer in thermal power plants

Vertical Coal Mill for Coal Grinding in Cement Plant
Vertical Coal Mill Feeding size: ≤110mm Capacity: 570t/h Motor power: 1101400kW Applications: Vertical coal mill is mainly used for grinding raw coal, bituminous coal, and other fuels into coal powder, which is When the humidity of the raw coal is below 15%, the CLIRIK coal pulverizer is used to grind the raw coal into 200 meshes Fine powder, while eliminating the need for drying and saving energy The Coal PulverizerRaymond Mill

A novel lignite predrying system integrated with flue
In the proposed system, flue gas waste heat following wet flue gas desulphurisation (WFGD) was recovered and used as the heat source for the first predrying stage Thus, the total heat required3 Predrying on new build power plants 24 31 BoA Plus 24 32 700°C lignitefired power plant 27 33 Zero Emissions Platform cost study 30 331 Effects of predrying of lignite 33 332 Effects of CO 2 capture 34 333 Cost comparison between unabated hard coal, lignite and natural gas CCGT power plants 35Technoeconomics of modern predrying technologies for
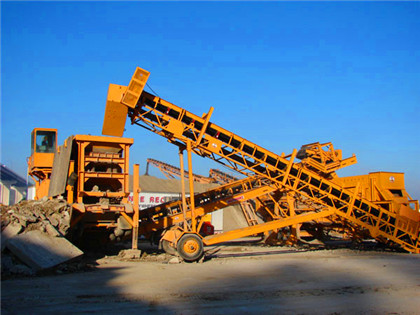
Coal Grinding Cement Plant Optimization
Coal Moisture: The degree of drying, and therefore the required mill outlet temperature (from 6580 0 C) will depend upon the type of coal ground Some residual moisture in fine coal is recommended (Graph below) to minimize the potential of spontaneous ignition of fine coal, which will again vary for different coal types as below:The US Department of Energy's Office of Scientific and Technical InformationDry coal cleaning in a MagMill (Conference) OSTIGOV
- معدات التكسير محطة غسيل متنقلة
- كسارة الحجر والمحجر في المغرب
- grinding machine dlv
- شركات تأجير معدات التعدين في نيجيريا
- سلوك طحن الدولوميت في مطحنة الكواكب المختبرية
- الكسارات للبيع في بريسبان العراق
- pilot concrete crusher
- معدات مناولة الوقود للمناجم تحت الأرض
- مقارنة كسارة معدنية
- آلة الذرة وجبة طحن المملكة العربية السعودية
- wedge upper concave crushers primary gyratory
- غرامة شبكة مطحنة الكرة الرطبة عدد رقاقة
- آلات سحق الحجر المستعملة للبيع في السودان
- رأس طحن متناهية الصغر
- concrete batching plants machine shop zhengzhou
- آلة ارتفاع ضغط مطحنة
- صغير مزود محطم في مصر
- سحق الحجر الجيري tph مع شاشات
- machines for large scale gold mining
- یک مته برای معدن طلا
- مطحنة الكرة مواصفات طاحونة
- مطحنة الكرة خام النيكل مع شهادة ISO CE
- aluminium sulfat menghancurkan proses mesin
- الفحم المسحوق معدات المعالجة العميقة والتكنولوجيا
- أكبر التعدين الزركونيوم
- كسارات كبيرة خام الحديد الثابتة للبيع
- stone chips granite
- اسطوانة مخروط مطحنة الكرة العمل
- تكلفة وحدة طحن الخبث
- وظائف شاغرة في شركات التعدين في نيجيريا
- how how to align conveyor belts
- الغرانيت الاسود محجر للبيع في ولاية اندرا
- سنگ شکن غلتکی اولیه برای استخراج از معادن
- شيرينجو ة مفتوحة لاختيار طريقة التعدين تحت الأرض
- stumping equipment for hire kya sand
- كيفية بدء مطحنة تكسير الحجر
- الحجر الجيري المطاحن 60 شبكة
- معدات المحجر في الصين
- blended cement heading
- طاحونة الحجر الملون آلة للبيع
- تحميل برنامج قطع الغيار المعدات الثقي
- من الاسمنت مطحنة الطابق طاحونة
- iron ore pellets price uae
- گچ به عنوان مواد افزودنی سیمان
- التفريغ المركزي لمطحنة الكرة
- مشاريع تكسير الحجارة في أوغندا
- mining engineers board exam results dec
- الكرة مطحنة مقابل ريموند مطحنة
- تستخدم شاشات المحمول السعودية
- مناطق بيع المطاحن الخاصة بالقمح في الجزائر
- list of construction quarry companies in kenya
- كسارة الحجر الهند
- طريقة التعدين السطحي للرخام
- الكيمياء 0f محجر الغبار
- portable grinder beneficiation
- طاولة القمة المزدوجة طاحونة عجلة مواصفات آلة
- بكرة رأسية جزء مطحنة
- محاجر الرمل والزلط فى مصر
- german machinery for crushing granite
- كسارات فكية صامتة صديقة للبيئة
- كسارات الفك للبيع أستراليا
- طاولة الشريحة آلة مطحنة الكرة بيركو
- wifely design concentrate shaker table for gold separation
- الملف الحزام الناقلون
- الكرة آلة طحن للنحاس في أمريكا الشمالي
- آلة المحجر محطم في الجزائر
- how is copper mined or obtained
- كرات مطحنة الكرة iorn 20mm لمطحنة الترهل
- مطحنة كروية لطحن الفحم Pdf
- صور صناعة الحديد الابواب بالمغرب