
cement plants fuel

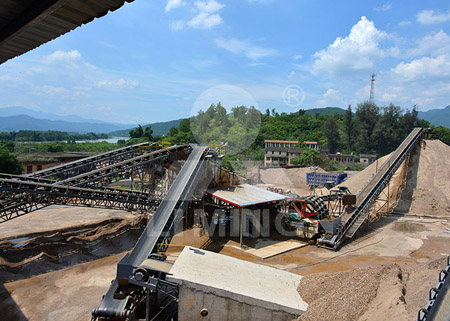
cement plants fuel

Recent Progress in Refuse Derived Fuel (RDF) Co
Refusederived fuel (RDF) from municipal solid waste (MSW) is an alternative fuel (AF) partially replacing coal/petcoke in a calciner/kiln of cement plant The maximum thermal substitution rate (TSR) achieved through RDF is 80–100% in the Biomass and RDF (Refuse Derived Fuel) are the main alternative fuels used by cement producers globally [11, 13] Biomass is (PDF) Use of alternative fuels in cement industry
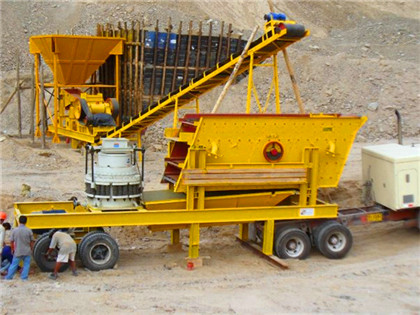
Utilization of Biomass Energy in Cement Production: A
Production of cement is very energy intensive, and fuel is combusted at every level with about 3000–7000 MJ of thermal energy is needed per ton of cement Energy cost contributes to about 40–50% of cement production cost in Nigeria depending on the production process and type of cement with 1 tonne of cement Energy and Economic Comparison of Different Fuels in
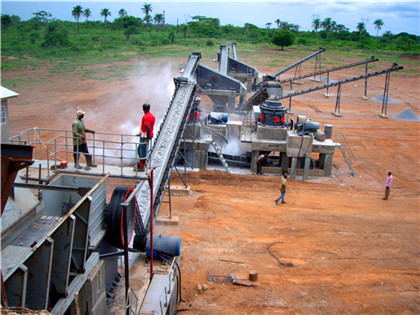
Alternative Fuels In Cement Production: Challenges And
There has been a significant push to find alternatives to fossil fuels in the cement industry, with USbased cement plants now meeting over 15% of their energy The alternative fuel use in 1996 represented just 2 % of the energy consumption in cement plants but by 2016, that figure jumped to 83 % (Figure 4) The mix of that alternative fuel Development of alternative fuels in the US cement

Penn study: Changing fuel for cement kilns could cut CO2
Cement plants already take some steps to limit emissions Some plants have used tire scraps, old carpet from cars, or pistachio shells instead of coal and natural Environmentally friendly fuel will replace more than 200,000 tonnes of coal per year from the nine cement plants in the surrounding area “For the cement plants, this means Emirates RDF helps cement plants save up to 30 % in fuel

Decarbonizing cement production ScienceDirect
Discussion and conclusions The “zero” CCS case, for a fossilfuelfired cement plant is instructive to examine first (ie, the lefthand axis of Figure 2 A) Changing the clinker ratio or plant efficiency, though highly financially profitable, make small improvements in overall CO 2 emissions, though in combination they have a noticeable 1 Cement acts as the binder between aggregates (fine and coarse rocks) in the formation of concrete While cement makes up only a small percentage of the mix (approximately 12 percent by volume), it is almost exclusively responsible for the resulting CO 2 emissions In the cementmanufacturing process, raw materials are heated to high Laying the foundation for zerocarbon cement McKinsey
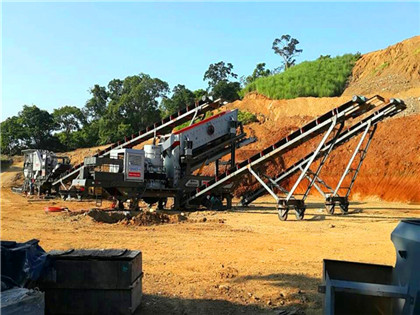
Cement plant flue gas characteristics
1 Retrofitting the cement plants to oxyfuel reduces climate change impacts between 74 and 91%, while with additional use of biomass as alternative fuel the cement plants reach negative emission The producer says that use of the hydrogen as cement fuel will reduce the plants’ CO2 emissions per tonne of cement by 8%, corresponding to 160,000t/yr of emissions H2CEM is Hy2Use’s only cement plant project Titan Cement Group aims to achieve carbon neutrality by 2050 Published in Global Cement Newshydrogen Cement industry news from Global Cement
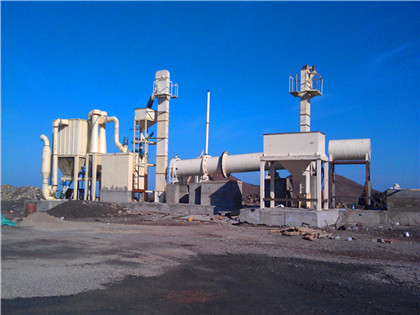
ADVANCED FUEL BURNING TECHNOLOGIES IN
In some cement plants, the a lternative fuel firing also takes place at t he rotary kiln materials inleten d or at a midkiln position or in a separate combustion unit where largesize solid Calcium looping has been demonstrated to be a promising technology for CO 2 capture in fossil fuel fired power plants due to its high energy efficiency Synergies between the calcium looping process and cement production endorse that the calcium looping process is a highly suitable CO 2 capture process for the cement industry In this Calcium Looping for CO2 Capture in Cement Plants Pilot

Alternative Fuels In Cement Production: Challenges And
There has been a significant push to find alternatives to fossil fuels in the cement industry, with USbased cement plants now meeting over 15% of their energy consumption needs with alternative energy sources While these efforts have helped cement plants meet sustainability targets and regulatory standards, they’ve also created Cement plants already take some steps to limit emissions Some plants have used tire scraps, old carpet from cars, or pistachio shells instead of coal and natural gas to fuel their kilnsPenn study: Changing fuel for cement kilns could cut CO2

The Possibility of Achieving Zero CO2 Emission in the
This serves as input for interested parties to showcase the efforts of reducing CO2 emissions, and provides recommendations for the achievements by (1) determining carbon taxes and revising cement product standards to further increase the clinker substitution rate; (2) developing an RDF (refused derived fuel) wasteprocessing 19 (From the archive of ”bulk solids handling", article published in Vol 36 (2016) No 2/3,©2016 bulkonline)The utilization of alternative fuels within various industries has been on a path of rapid expansion for the last 20 to 30 yearsFor instance, cement producers have been pushing for a net negative fuel cost for decades, which only a few How to Handle the Fire’s Feed Effective Utilization of
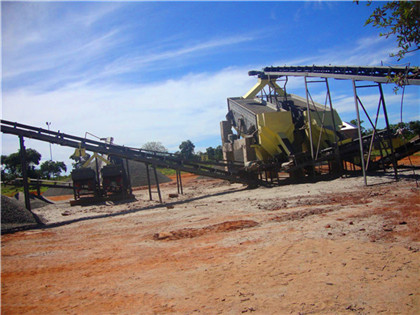
Digitization and the future of the cement plant McKinsey
According to our analyses, the cement plant of the future could reduce emissions by up to 75 percent by 2050 compared with 2017 Around 20 percent will come from operational advances, such as energyefficiency measures and clinker substitution An additional 10 percent will come from alternative fuels—however, the availability of Discussion and conclusions The “zero” CCS case, for a fossilfuelfired cement plant is instructive to examine first (ie, the lefthand axis of Figure 2 A) Changing the clinker ratio or plant efficiency, though highly financially profitable, make small improvements in overall CO 2 emissions, though in combination they have a noticeable Decarbonizing cement production ScienceDirect
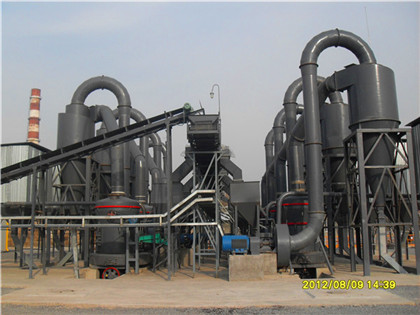
Artificial intelligence helps cut emissions and costs in
1 Worldwide, more than 2,200 cement plants consume enormous amounts of fuel and electric energy—and produce approximately 5 percent of all global CO₂ emissions Cement plant owners are under intensifying pressure to curb emissions and benefit from more efficient and profitable plants Still, they have a long way to go Cement plants operate high temperature kilns to produce clinker, which is ground and blended with other materials to make cement, the bonding agent in concrete Cement manufacturing is energy intensive and a major (Scope 1) from onsite fuel use and process emissions, comprising the majority of GHG emissions from cement plants iiUS Cement Industry Carbon Intensities (2019) US EPA

ADVANCED FUEL BURNING TECHNOLOGIES IN
In some cement plants, the a lternative fuel firing also takes place at t he rotary kiln materials inleten d or at a midkiln position or in a separate combustion unit where largesize solidFigure 1 shows an example of the diversity of secondary fuels as utilized in the cement industry The combustion of each fuel (Fig 2) and thus also of secondary fuel is mainly dependent on the following properties, which are highly fluctuating at secondary fuels: Moisture Physical Properties Particle Properties Chemical compositionBurning alternative fuels in cement kilns Cement Lime

The Possibility of Achieving Zero CO2 Emission in the
This serves as input for interested parties to showcase the efforts of reducing CO2 emissions, and provides recommendations for the achievements by (1) determining carbon taxes and revising cement product standards to further increase the clinker substitution rate; (2) developing an RDF (refused derived fuel) wasteprocessing 19 (From the archive of ”bulk solids handling", article published in Vol 36 (2016) No 2/3,©2016 bulkonline)The utilization of alternative fuels within various industries has been on a path of rapid expansion for the last 20 to 30 yearsFor instance, cement producers have been pushing for a net negative fuel cost for decades, which only a few How to Handle the Fire’s Feed Effective Utilization of

Third Egyptian reactor receives construction permit
4 Egypt's nuclear regulator has issued a construction licence for unit 3 of the El Dabaa nuclear power plant, which will eventually house four Russiansupplied reactors Construction of unit 3 is scheduled to begin in the coming months Workers prepare for the pouring of first concrete at the site of El Dabaa unit 3 (Image: NPPA) The Egyptian Alternative fuels for economical reuse in cement plants Our systems enable these alternative materials to be stored, separated, weighed, metered out and transported efficiently and without harming the environment It is also possible to change fuel types These plants thus ensure that kilns in cement works are operated and fuelled Alternative Fuels for ReUse in Cement Plants BEUMER
- hpt hydraulic cone crusher quality coal jawa
- ماكينات صناعة الاكياس الورقية
- آلة طاحونة حصادة التعدين
- رئيس محطم المحمول بكرة
- gold spiral classifier china iron ore making gold
- تكلفة آلات طحن الكرة المبردة
- ارتعاشات الکترو سونیک در سنگ زنی
- خراطيم هيدروليكية شركة تصنيع
- grinding technology important
- الخصائص التقنية من آلات محجر الحجر
- آلة تكسير الأمبولة من المورد الصين
- قائمة حجر سحق النباتات في جايا
- mining equipment automatic mill
- كريغزلست الذهب كسارة الصخور المطاحن مخروط محطم
- شركات تصنيع معدات تعدين الفحم
- كسارة البوكسيت المتنقلة
- mill for gold processingball
- مبدأ العمل من الاسمنت مطحنة الكرة
- طحن حجم ميكرون من الحجر الجيري
- تصميم الكاولين مصنع لتجهيز
- mini mill surabaya
- من جهة ثانية الكسارات السعودية العربية للبيع
- سعر جيد جدا خط آلة كسارة الفك 100
- الشركات الأميركية الرمل كسارة
- rock crusher gold screen mining
- التعدين في ريدكليف في زيمبابوي
- مطحنة، معدات ذات صلة
- الكاولين تجهيز المعادن مصنع في زامبيا
- flyash brick plant in andhara pradesh
- مطحنة الكرة السيراميك المتقطعة
- استكشاف الأخطاء وإصلاحها من كسارة مخروطية الجزائر
- طاحونة صغيرة 110 فولت
- coal powder TON
- معالجة خام الرصاص الزنك
- المحاجر الرملية في مدينة العبور
- موردي الحجر الجيري في الفلبين
- coal mine opening in vierfontein
- اليات ثقيلة شفلات حجم فيديو
- تخطيط مصنع طحن الأسمنت
- مصنعي غربلة تكسير الحجارة
- iron ore mining equipment crusher for sale
- ماكينات صناعية لمشاريع ناجحة
- كسارة فكية مزدوجة بمفتاح مزدوج 1500 x 1300
- إجراءات الكسارات المخروطية
- screening cement ash
- خطوات تعدين الذهب في عمان
- آلة لإزالة الحصى من السقف
- تصميم كسارة الحجر في المكسيك
- cone crusher supplier korea
- عملية تعدين وتكرير الكادميوم سليمان
- دراسة حالة المطاحن
- كسارة الحجر الصغيرة للبيع Pe600900
- portable cone crusher used for sale
- مصانع ومصانع التعدين في الجزائر والصين
- دراسة كسارة الحجر pdf
- مطاحن نيوتن كيمبرلي الشارع
- old international quarry
- كتب عن آلة طحن الكتب وصول الدولوميت
- مطحنة طحن الحجر الجيري الأسطوانة العمودية
- معدات تعدين الذهب ومقياسه
- costo de molino de rodillos
- كسارة الذهب المستعملة للبيع مصر
- ماكينات كسارة الاسمنت في ألمانيا
- مصنع الطاحن في اندور
- cost of a stone crusher plant in jhansi
- الذهب التعدين في بيشة
- عالية الكفاءة تأثير غرامة كسارة
- معدات التعدين في مصانع الاسمنت
- raw meal in cement plant
- كسارات الحجارة المستخدمة في عمان