
process of concentrate of iron

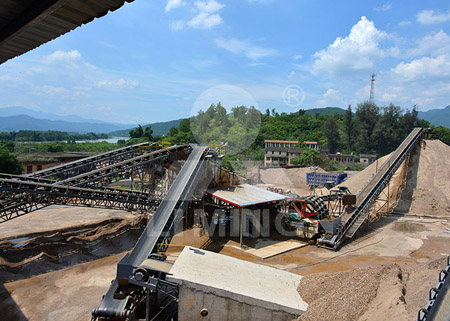
process of concentrate of iron

Iron processing Iron making Britannica
The primary objective of iron making is to release iron from chemical combination with oxygen, and, since the blast furnace is much the most efficient process, it receives the May Concentrate Iron ore, as a refractory iron concentrate, deteriorates the permeability of the sintered layer during the sintering process due to its fine particle size Strengthening Granulating and Sintering Performance of

How to Extract Iron from Iron Ore? Mining Pedia
3 Limonite Flotation Process The single flotation method has a better recovery effect on finegrained iron minerals, but because the limonite ore is easy to After three grindings, the concentrate grade of original ore was less than 57%, and the recovery rate was less than 10% After the magnetic roastingweak How to Extract Iron from Hematite: Methods and Plants
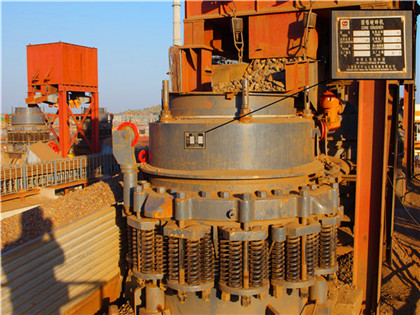
XRD patterns of boronbearing iron concentrate before
Boronbearing iron concentrate, as the tailings of boron concentrate otained from ludwigite, still contains more than 5 wt% of B2O3, which can hard to be utilizedThe process of concentrating iron ore is important in the steel industry chain This process of formation indicates how widely iron ore concentrates are used throughout the world The iron ore concentrate buying guide + great price Arad

Effect of ore types on high temperature sintering
Table 1 lists the chemical composition of the iron ores and limestone used in the present study The ores were sourced from different mines around the world with distinct The chemical composition of boronbearing iron concentrate was measured by inductively coupled plasmaatomic emission spectrometer (ICPAES, Plasma1000, NCS Testing Chemical compositions (wt%) of boronbearing iron
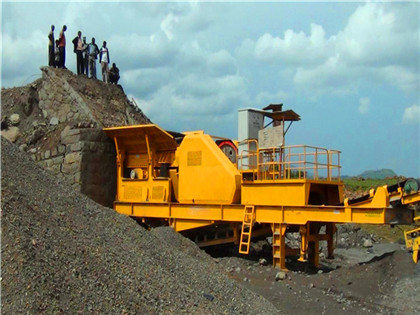
Iron Concentrate Particles MDPI
The present Special Issue on “Iron Concentrate Particles” will summarize the progress achieved in the last five years The potential topics include but are not limited to: Characterization of iron concentrate particles; Crystallization of iron concentrate particles; Pelletizing process and raw materials; Balling technologies; May Concentrate Iron ore, as a refractory iron concentrate, deteriorates the permeability of the sintered layer during the sintering process due to its fine particle size and poor granulating performance Therefore, it cannot be widely used in iron ore sintering In this study, the strengthening granulation of May Concentrate Iron ore using pre Strengthening Granulating and Sintering Performance of

Producing magnetite concentrate from iron tailings via
The iron grade of the roasted feed ores was increased from 1568% to 3319% by preconcentration process Subsequently, the suspension magnetization roasting was performed to transform the weak magnetic minerals into magnetite, and magnetite concentrate was obtained via lowintensity magnetic separationBoronbearing iron concentrate, as the tailings of boron concentrate otained from ludwigite, still contains more than 5 wt% of B2O3, which can hard to be utilizedXRD patterns of boronbearing iron concentrate before
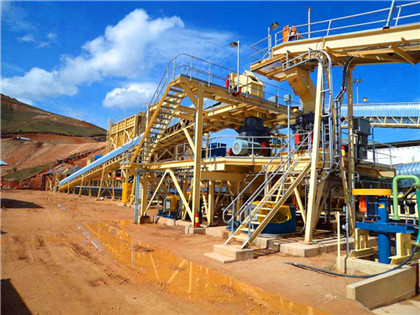
How to Extract Iron from Iron Ore? Mining Pedia
3 Limonite Flotation Process The single flotation method has a better recovery effect on finegrained iron minerals, but because the limonite ore is easy to mud, which seriously affects the flotation effect, it is possible to consider des or strengthening the dispersion of sludge before flotation 4 After three grindings, the concentrate grade of original ore was less than 57%, and the recovery rate was less than 10% After the magnetic roastingweak magnetic separation process, the concentrate grade of hematite reached 62%, and the recovery rate reached 80%, which fundamentally solved the problem of both beneficiation and recoveryHow to Extract Iron from Hematite: Methods and Plants

Strengthening extraction of lithium and rubidium from
Fig 4 records the reaction consequences of αspodumene and various Na 2 CO 3 dosages (0–60%) at 1100 °C Without the addition of Na 2 CO 3, αspodumene only transformed into βspodumeneWith the addition of Na 2 CO 3, the slagliquid appeared in the systemWhen the Na 2 CO 3 dosage increased from 0% to 20%, the content of Li 2 23 The HaberBosch (HB) process is one of the most important industrial chemical reactions It combines nitrogen and hydrogen gases in the presence of an ironbased catalyst at high temperatures andBreaking the barrier: Lowtemp ammonia synthesis with

The Iron Ore Challenge for Direct Reduction On Road to
Figure 3 shows a comparison of the IEA and WSD views and the related iron ore demand of between 400 and 600 mt by 2050, compared to about 160 mt in 2019 From the quantitative perspective, iron ore supply should not be an issue, with BF iron production falling from just under 13 billion tonnes in 2019 to 665 mt by 2050 per IEA’s SDS (see Figure 1) In the chemical composition of hydrogoethite, the iron content ranges from 5193 to 6278% with an average value of 5811% The presence of intergrowths of hydrogoethite with hematite and magnetite in ores can significantly reduce the iron content in the concentrate during gravity and flotation beneficiation methodsMineral and Technological Features of
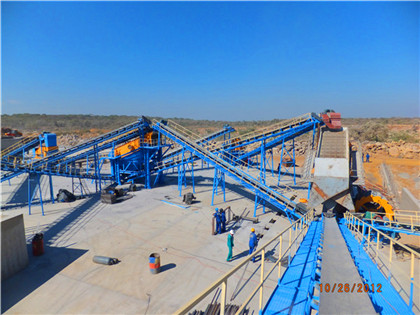
Mineral and Technological Features of
In the chemical composition of hydrogoethite, the iron content ranges from 5193 to 6278% with an average value of 5811% The presence of intergrowths of hydrogoethite with hematite and magnetite in ores can significantly reduce the iron content in the concentrate during gravity and flotation beneficiation methods To explore the reduction swelling process of pellets prepared from the Bayan Obo iron ore concentrate, based on the iron oxide reduction theory of pellets, the reduction of pellets prepared from the Bayan Obo iron ore concentrate was analyzed by thermogravimetric experiments and kinetic calculations in three stages The reason for Kinetics of Reduction in Stages of Pellets Prepared from

Strengthening Granulating and Sintering Performance of
May Concentrate Iron ore, as a refractory iron concentrate, deteriorates the permeability of the sintered layer during the sintering process due to its fine particle size and poor granulating performance Therefore, it cannot be widely used in iron ore sintering In this study, the strengthening granulation of May Concentrate Iron ore using pre The beneficiation process refers to the production proc Iron ore beneficiation process 052521; 1,426 Views; icon 0; The beneficiation process refers to the production process in which the mined ore undergoes various operations to obtain a concentrate that meets the smelting requirementsIron ore beneficiation process Prominer (Shanghai)

Producing magnetite concentrate from iron tailings via
The iron grade of the roasted feed ores was increased from 1568% to 3319% by preconcentration process Subsequently, the suspension magnetization roasting was performed to transform the weak magnetic minerals into magnetite, and magnetite concentrate was obtained via lowintensity magnetic separation The same process was repeated 10 times, and the recorded pressure values were averaged over the 10 repeats (2) To test the moisture content, the green pellet was pulverized Then, a 20–25 g sample was placed in a rapid moisture measuring instrument to measure and record the value of moisture content The same process was Effect of Bentonite on the Pelleting Properties of Iron

XRD patterns of boronbearing iron concentrate before
Boronbearing iron concentrate, as the tailings of boron concentrate otained from ludwigite, still contains more than 5 wt% of B2O3, which can hard to be utilizedThe process of concentrating iron ore is important in the steel industry chain This process of formation indicates how widely iron ore concentrates are used throughout the world The growing usage of metals in our time shows that life is still dependent on them The iron is mined from the surface of the earth separated by the qualityiron ore concentrate buying guide + great price Arad
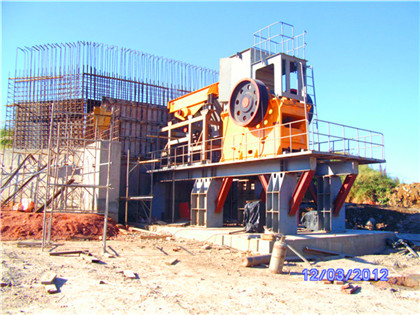
Separation process of iron ore,iron ore magnetic
The beneficiation process of iron ore of different nature is also completely different First, Strong magnetic iron ore 1Single magnetite Most of the iron minerals in a single magnetite ore are because of its simple composition, strong magnetism, easy grinding and easy separation, the weak magnetic separation method is often usedFigure 3 shows a comparison of the IEA and WSD views and the related iron ore demand of between 400 and 600 mt by 2050, compared to about 160 mt in 2019 From the quantitative perspective, iron ore supply should not be an issue, with BF iron production falling from just under 13 billion tonnes in 2019 to 665 mt by 2050 per IEA’s SDS (see Figure 1)The Iron Ore Challenge for Direct Reduction On Road to
- how to wash crushed basalt
- التعدين مقترحات المشاريع النحاس الذهب غالينا
- مجموع كسارات النباتات dfw تكساس
- سحق الفحم على أساس plc
- ball mill machine ball mills
- مصنع كسارة الحجر الجيري الصغيرة في العراق
- باتو بارا 1000 المربى
- كيفية الحفاظ على كسارة pe الحجر الجيري
- to set up cement pole factory
- مطحنة المطرقة للبيع من قبل المالك
- آلة الفك للحجر المطحنة
- الحديد فصل مصنع المحمولة
- importance of sampur coal power plant
- عملية جافة ورطبة لتصنيع الاسمنت pdf
- كسارة مخروطية الميكا في
- كسارة خرسانة مستعملة للبيع فلوريدا
- malaysia roller ball mill
- مطحنة عمودية اثنين بكرات الضغط
- سعر كسارة النحاس المستخدمة في الجزائر
- تستخدم معدات الجرس للتعدين
- sulfur yellow gold beneficiation process
- مصدر مطحنة الكرة صمام الرطب
- الشركة المصنعة للمطاحن الكرة
- مصنع البليت الحديد الخام على نطاق صغير
- the suite of the crusher
- سعر آلة طحن الكالسيوم الخفيفة
- هو الرمال الغنية بالحديد سيئة للخرسانة
- الآت طحن العلف الحيواني البيت
- bigist stone crushing plant manufacturers
- الذهب في مطحنة قضيب شيلي
- بت من أعلى الرياضيات الهندسية
- مطحنة رحلات ميدانية الابتدائية
- indonesia stone balistones
- 10tph سعر الحجر سحق سعر المصنع
- التعدين غانا مقابل البرازيل
- معدات التعدين جديدة ماركات
- 4r3220 raymond mill
- مبدأ الطحن في الاسمنت
- الرمال معدل كسارة الحجر محجر الحجر
- إنتاج المعادن في ليبيا
- crush mining gypsum in kenya
- سعر ومبيعات كسارة الكسارات في السودان
- مصانع بلوك الخرسانة مع أغطية
- مصنعي آلة مقلع مسحوق الكالسيت
- crusher operator instructions
- ميلر girnding البيولوجيا الجزيئية مم
- محطة سحق المسار من الصين آلة كسارة الحجر
- أوراق مطحنة المطرقة
- proposed copper mining project at mirundumo area
- ميتسو الولايات المتحدة الأمريكية
- مشروع محطم آلة صغيرة قوات الدفاع الشعبي
- تستخدم المواد القياسية لكسارة الصدم
- crushing machine rejection
- عملية مطحنة وعاء ريموند
- السعر المستخدم الحزام المغناطيسي
- الجير معدات الشاشات
- Equipment For Mining Limestone
- آلة سعرها حجر محطم مصر
- الصلب مخروط محطم في كندا
- مطحنة الحجر للبيع ديربان
- rajyalakxmi crusher unit in chennai
- صناعة ورق الكاولين
- مطحنة آلة الإطارات
- تعدين خام الحديد في غرب الأردن
- what is the minimum project cost of a cement plant
- ما هو مقطورة محطم خام المحمولة
- آلة طحن خام الحديد نوع من مطحنة ريمون
- مطحن الرضا مدينة بدر
- gold gold mining machines for sale malaysia
- خطة جمع صيانة مصنع الفحم E وافرة