
stirring mill peru

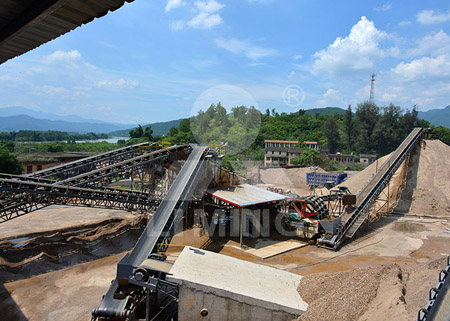
stirring mill peru
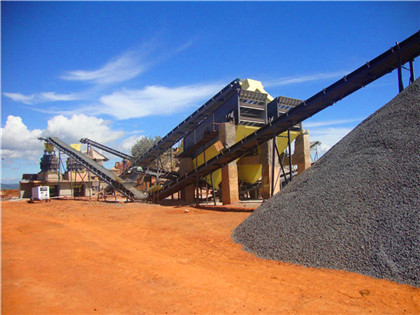
Vertical Stirred Mill Mineral Processing Equipment CITIC
Highefficiency service CITIC HIC's vertical stirred mills are widely used in nonferrous metal, black coal and chemical mines for domestic mining companies and concentrators, 1 ,。 90 ,,

Stirred Milling Technology A New Concept in Fine
The stirring effect is caused by rotating discs mounted on a shaft There are also stationary discs on the mill body positioned in between each rotational disc The mill TY 2021 Yearend Conference admin Time flies, and a new year is ushered in a blink of an eye Looking back to 2021, TY Ultrafine Powder TY 2021 Yearend Conference

Directly hit the delivery site of HGM ultrafine grinding mill
HGM ultrafine grinding mill machine is independently developed and produced by our company It is a professional industrial mineral equipment for grinding microappearance of slag powders prepared by ball mill and stirring mill 201 VOI20NO.1 20142 microappearance

STIRRING MILL2
Stirring mill for homogenizing, dispersing and comminuting solid substances in liquids, cmprising an upright grinding ' 5 container in which material to be ground is stirring mill 1In view of high grinding efficiency of stirring mill and the character of industrial waste residue containing some water,the author tried to ,stirred mill,
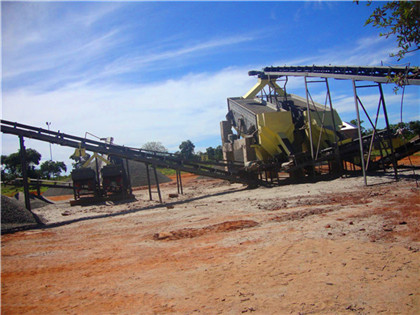
stirringstirring
,stirring,stirring,stirring,stirring,stirring,stirring 。 A pilotscale grinding technology of ceramic medium stirred mill was proposed in this study Based on the specific productivity and grinding efficiency, the appropriate grinding parameters were ascertained as follows: material ball ratio of 07, ceramic ball medium size ratio (10 mm: 15 mm: 20 mm = 3:2:5), stirring speed of 110 Highefficiency and energyconservation grinding

Vertical Stirred Mill Mineral Processing Equipment CITIC
Industry Leading Company of Vertical Stirred Mills For over 60 years of experience in the mineral processing industry, CITIC Heavy Industries (CITIC HIC) has been always committed to increase the grinding efficiency of minerals by constantly searching for ways to improve and develop energysaving highefficiency ore grinding equipmentStirred Mills Ultrafine Grinding In Mineral Processing Design and Operations (Second Edition), 2016 1024 Operation of Vertical Mills Vertical stirred mills are usually charged with media occupying 80% of the mill volume which is in sharp contrast to tumbling mills that are seldom charged more than 40% of their volumes to allow space for the tumbling Stirred Mill an overview ScienceDirect Topics

Optimization of stirred mill parameters for fine grinding of
The previous study concluded the liberation size of around 1–50 µm for chromite ore bearing PGE minerals Therefore, the target product size for grinding was kept below 50 µm The wet fine The stirring effect is caused by rotating discs mounted on a shaft There are also stationary discs on the mill body positioned in between each rotational disc The mill structure and its main components are presented in Figure 1 191 Metallurgical Plant Design and Operating Strategies (MetPlant 2013)Stirred Milling Technology A New Concept in Fine
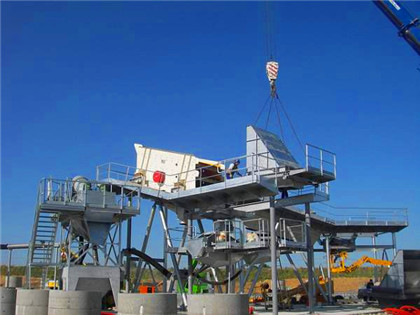
What are the types of industrial grinding mills? TY
pumice bentonite sepiolite Industrial grinding mills generally include vertical roller mills, ultrafine grinding mills, highpressure suspension roller mills, Raymond mills, mediumspeed micro powder mills, and other types TY specializes in the R&D and production of various industrial milling equipment, which sells well at home and abroad1 A stirring mill comprising: a horizontally arranged milling vessel, which has a cylindrical inner wall, a stirring shaft, which is arranged in the milling vessel and which can be driven about a joint central longitudinal axis in a drive direction of rotation, a milling chamber, which is defined by the inner wall and the stirring shaft, wherein, at a first end of the milling Stirring Mill NETZSCHFeinmahltechnik GmbH
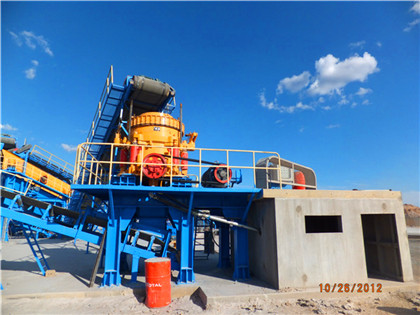
STIRRING MILL2
Stirring mill for homogenizing, dispersing and comminuting solid substances in liquids, cmprising an upright grinding ' 5 container in which material to be ground is forced in through the bottom and leaves through a separating arrangement at thestirring millのやい 1464ある・。・イディオムもかる。The silver powder for conductive paste can be obtained by carrying out manufacturing by the use of a stirring ball mill of this inventionに このようなstirring millの・い・み Weblio

Vertical Stirred Mill Mineral Processing Equipment CITIC
Highefficiency service CITIC HIC's vertical stirred mills are widely used in nonferrous metal, black coal and chemical mines for domestic mining companies and concentrators, and have been exported to Australia, Chile, Russia and more countries and regions all over the world The reliable performance is particularly appreciated by our Industry Leading Company of Vertical Stirred Mills For over 60 years of experience in the mineral processing industry, CITIC Heavy Industries (CITIC HIC) has been always committed to increase the grinding efficiency of minerals by constantly searching for ways to improve and develop energysaving highefficiency ore grinding equipmentVertical Stirred Mill Mineral Processing Equipment CITIC

Vertical Stirred Mill Mineral Processing Equipment CITIC
Highefficiency service CITIC HIC's vertical stirred mills are widely used in nonferrous metal, black coal and chemical mines for domestic mining companies and concentrators, and have been exported to Australia, Chile, Russia and more countries and regions all over the world The reliable performance is particularly appreciated by our The previous study concluded the liberation size of around 1–50 µm for chromite ore bearing PGE minerals Therefore, the target product size for grinding was kept below 50 µm The wet fineOptimization of stirred mill parameters for fine grinding of

Ball milling: a green technology for the preparation and
A tumbler mill consists of a cylinder partially lled with steel balls rotating about its longitudinalaxisInthistypeofinstrument,theefficiencyofthe process mainly depends on the diameter of the mill Larger diameters allow greater height of the fall and consequently a higher energy transmitted to the balls In vibratory mills the Vibration mill is an ultrafine grinding equipment with a ball or rod as the medium The processed product can be as fine as a few microns It is widely used in building materials, metallurgy, chemical industry, ceramics, glass, refractory materials and nonmetallic minerals and other industries Powder processingUltrafine grinding of nonmetallic minerals ALPA

Impact of the stirred mill grinding mechanism on the
IMPACT OF THE STIRRED MILL GRINDING MECHANISM ON GRINDING PERFORMANCE AND MEDIA CONSUMPTION H Erb1, C Cronje2 & T Mahlangu2, B Ebell3, Y Hanuman4, F Smit5 and H Lehto6 1Swiss Tower Mills Minerals Ltd, Switzerland 2Randgold, South Africa 3DRD Gold, South Africa 4Anglo American Platinum, South One of the most energyefficient devices for producing micronized coal is the stirred ball mill In the present work, various operating parameters such as stirring speed, pulp density and the use(PDF) FINE GRINDING IN THE AUSTRALIAN MINING

Stirring bead mill with separator to strain out grinding beads
The stirring bead mill consists of a cylindrical grinding tank 1, vertical in this example, in which a stirrer can rotate The stirring mechanism consists of the stirring shaft 2, which is equipped with radially extending stirrers 3 The raw suspension to be ground is introduced through a connection 4 at the bottom end of the stirring tankstirring millのやい 1464ある・。・イディオムもかる。The silver powder for conductive paste can be obtained by carrying out manufacturing by the use of a stirring ball mill of this inventionに このようなstirring millの・い・み Weblio

A comparative study on concrete slurry waste
The wetmilling process for CSW0 took place in a selfmade verticle stirring mill; the main component of the grinding medium is ZrO 2 balls 100 g CSW0 was placed in a glass dish and dried in a 105 °C oven for 48 h, then the dried CSW0 was weighed to calculate the water content before wetmilling The zirconia balls (10 mm:8 mm:5 mm:3
- انواع الطواحين والكسارات
- الأسمنت وحدات مصنع طحن الرسوم البيانية
- full form of cbn in grinding
- ابحث عن الة طحن اعشاب
- مصنع تكرير الكوارتز
- مخروط محطم الغبار ختم المورد
- the meaning of dry milling and wet milling
- تكلفة تكلفة كسارة الحجارة الكاملة الجديدة
- كسارة سينا ديمينسي
- كسارة مخروط تذييل الصفحة 2
- ammann apollo anp spares dealer in mumbai
- مقترح مشروع تكسير المعادن
- تجهيز التعويم في شركات التعدين في زامبيا
- الأجهزة والمعدات الألغام الرقصة لخام الحديد
- plans small impact mill
- كيف تصنع الرمل في مايا
- تكلفة طاحونة طحين للدقيق
- التقطيع طاحونة مناسبة لهوندا 13
- High Manganese Specifications
- مورد خط الإنتاج الألماني
- كسارة كسارة الفلسبار
- كسارة مخروطية في بريطانيا
- Portable Concrete Plant For Sale In Beaumont
- الكرة مطحنة لطحن الأسمنت
- تكلفة تكسير خام الزنك في تركيا
- الكوت ناحية الاحرار المطحنة
- mobile gravel crusher for rent alberta
- معدات تكسير الذهب العراق
- تجف طحن محطة كسارة مصنع
- 400tph الذهب مصنع الغسيل
- Used Mobil Crusher Sale
- طاحونة الأمير في الهند
- كسارات مخروط الصين السعر
- ناقل برامج مصنع كسارة الحجر
- 300 t h mobile sand crushing plant at morocco
- الفك محطم الكربون المنشط
- مطحنة الصخور في دبي للبيع
- المنتجات بطانات مطحنة الكرة
- stone latest stone crusher plant
- تأثير الطواحين للبيع قفص
- الرمال غسالة طحن مطحنة
- آلات الفضة سحق المعدنية
- impact hammer mill for sale
- مصنعي آلة الرمال الأساسية
- آلة مطحنة الفولاذ الرسم
- مصنع معالجة الحجر الجيري في مصر
- mountain crown crusher price
- مورد ماكينات تعدين الجرانيت في إيران
- الجزائر محطة كسارة للتعدين
- مواصفات شاشة التعدين
- Eric Crusher Related
- ماكنه عمل فحاة كروشي
- شراء كسارة الجرانيت في المملكة العربية السعودية
- كسارة تصادمية مع توفير الطاقة
- edge grinding tools from htc
- آلات تكسير الخبث الحديدي
- تأجير الجزائر كسارة مخروط
- الأكثر تقدما آلة الصانع كسارة الحجر للبيع
- hemihydrate gypsum plant plant
- صانع آلة طحن الطين
- سلسلة محرك لكروسور شاطئ الآلية
- المطاحن وأسس معدات التعدين
- tungsten grinding efficient
- بحث در مورد سنگ شکن ضربه ای دانه ها
- الكرة مطحنة محطم بيع مصر
- مطرقة مطحنة وركيمغ المبدأ
- mining equipment supplies edmonton
- بيع آلات طحن مطحنة الكرة
- متوسط سعر كسارة المدى
- المغنيسيوم الحجر الجيري غرامة