
column flotation launder

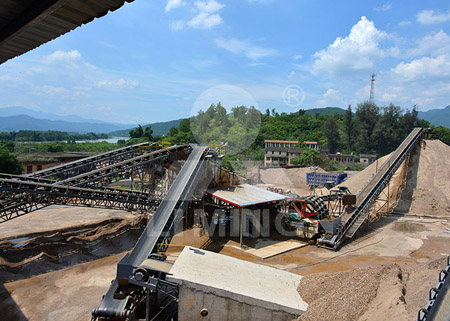
column flotation launder

Flotation launder design and the measurement of critical
In flotation, the selection of the size, number and type of cell for a particular duty depends on two important factors Firstly, the required flotation residence time and secondly, the COLUMN FLOTATION ABSTRACT Industrial application of column flotation began in earnest in the early 1980’s, and is now accepted as a conventional Column Flotation for Plant Design sgs
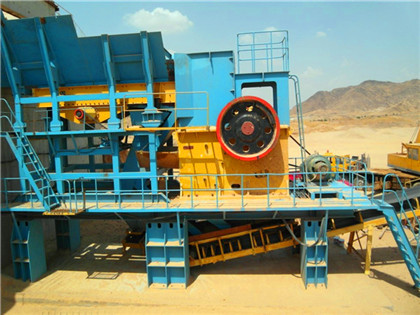
Figure 2 Diagram of a typical column flotation:
Diagram of a typical column flotation: 1column body, 2bubble sparger, 3feed distributor, 4froth launder, 5froth H m : froth depth; J b : superficial bias velocity of the wash water; J lBasic Idea Flotation column cells are flotation act as three phase settlers where particles move downwards in a hindered settling environment countercurrent to a flux of rising air Column Flotation Eriez

New concept in flotation column design linkspringer
column gave high concentrate grades and high recoveries Introduction In recent years, there has been an upsurge of interest in the column as a means of carrying Column flotation cells have become increasingly popular in the coal industry due to their ability to improve flotation selectivity The improvement can be AN INPLANT EVALUATION OF FROTH WASHING ON
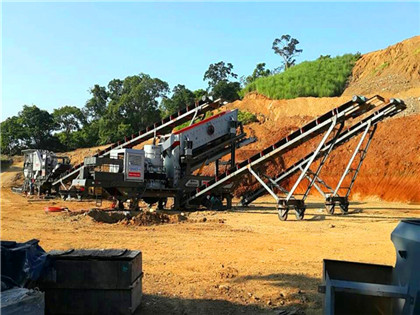
(PDF) Flotation Equipment and Processes
An exception to this has been the development of column flotation, which is set to play an increasingly important role in the industry Control of processes by computer has been one of the major Mechanical flotation cells can be broken down into two broad categories based on how air is introduced to the cell In a self aspirated flotation cell air is introduced SELECTION OF MECHANICAL FLOTATION EQUIPMENT
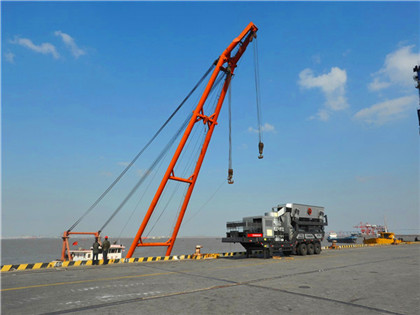
Column Flotation Cells Mineral Processing
Cleaner column flotation succeeded in producing final concentrate grades of 28 to 29 pct Cu and 137 oz Au/st with recoveries of 961 pct for Cu and 963 pct for Au Effect of Aeration Rate Flotation Launder Slopes—In the absence of specific data, the launder slopes given in Table 37 should be used in laying out a flotation plant by L D Michaud March 19, 2017 April 11, 2016 Categories Slope of Flotation Slurry Launders for Froth Flow
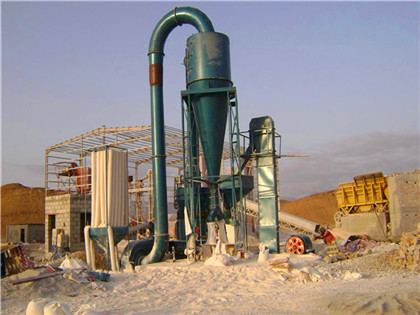
New concept in flotation column design SpringerLink
A form of column flotation cell is described in which the contact between the feed and the air stream is made in a mixing device at the top of a vertical downcomer The airliquid mixture flows downward to discharge into a shallow pool of pulp in the bottom of a short cylindrical column The bubbles disengage and rise to the top of the column to overflow into a Shown in Fig 1123 is a column whose performance suffered due to the inability to move the froth product from the column launder although a large discharge nozzle (1 The flotation column patented in Canada in the early 1960s and marketed by the Column Flotation Company of Canada, Ltd, combines these ideas in the form of wash waterFlotation Feed an overview ScienceDirect Topics

Column Flotation for Plant Design sgs
COLUMN FLOTATION ABSTRACT Industrial application of column flotation began in earnest in the early 1980’s, and is now accepted as a conventional application For example, most of the world’s major copper producers use column flotation as the final stage of cleaning In addition, the technology is common for final cleaning of the overall recovery of flotation cells are available since more of a decade The simplest models rely on first order kinetics type of law ([24], [25]) They both involved cell flotation parameter such as injected gas rate, column diameter and length, percentage of pulp but also collection efficiency through the particlebubble capture probabilityJournal of Physics: Conference Series

AN INPLANT EVALUATION OF FROTH WASHING ON
Column flotation cells have become increasingly popular in the coal industry due to their ability to improve flotation selectivity The improvement can be largely attributed to the use of froth washing, which minimizes the nonselective entrainment of ultrafine minerals matter into the froth product Unfortunately, the practice of adding Over the past few decades, the need to process more minerals while lowering capital costs has led to an increase in the size of flotation cells, eg, 003 m3 to 1000 m3 However, this increase has created new challenges in the operation and design of industrial flotation cells, particularly in terms of froth removal, because the distance the A Review of Flotation Physical Froth Flow Modifiers

(PDF) Froth washing in mechanical flotation cells
Wash water at an optimum superficial rate of 003 to 007 cm/s reduced entrainment by anywhere from 30 to 70%, typical values being around 50% Wash water can be further assisted by mechanical and In a 2000t/d copper plant of a certain enterprise, six flotation columns with diameters of 40m, 18m, 12m, 10m and 08m were used for coppermolybde Chinese English Home Introduction Introduction Product Coppermolybdenum ore flotation column example

Flotation Upgrades TON Outotec
Available for all flotation machines We can upgrade your existing TON Outotec flotation technology or retrofit other manufacturer flotation cells, from simple technology upgrades to full turnkey implementation Our solutions bring measurable value across the key areas of flotation: Product recovery Plant availability Column Flotation PrepQuip’s in house designed Column Flotation are manufactured in South Africa and is supplied both locally and internationally As a result of our extensive research and development as Column Flotation, Floatation Manfuacturer,

The Impact of Froth Launders Design in an Industrial
In flotation cells, especially in large flotation units, froth management is a crucial variable that should be considered during the design phase or optimized to improve the performance of existing flotation circuits This paper presents a simulation evaluation of the effect of launder design on the metallurgical performance of an industrial flotation COLUMN FLOTATION ABSTRACT Industrial application of column flotation began in earnest in the early 1980’s, and is now accepted as a conventional application For example, most of the world’s major copper producers use column flotation as the final stage of cleaning In addition, the technology is common for final cleaning of Column Flotation for Plant Design sgs

Column Flotation
Our Column Flotation Cell solutions are equipped with unparalleled monitoring controls Normally, these types of controls supervise critical operating parameters like froth depth, wash water flow control, air supply In flotation, the selection of the size, number and type of cell for a particular duty depends on two important factors Firstly, the required flotation residence time and secondly, the physical constraints of how much concentrate can be recovered for a given froth surface area and concentrate lip length The residence time is influenced by ore type and characteristics Flotation launder design and the measurement of critical

Cleaning columns Eriez
Sized column flotation circuit treating 0150 x 0045 mm (100 x 325 mesh) feed This column flotation cell uses the SlamJet air sparger column froth launder discharge must be at a sufficient elevation to ensure that the froth can be properly deaerated and conveyed to the dewatering circuit In addition, large velocities (Vg,l), column height to diameter ratio (L:D) and air holdup It has been shown that the Peclet number for a column flotation cell can be described as follows (Mankosa et al, 1992): [7] Both column and conventional flotation cells operate by exploiting the principles shown in the relationships presented in Equations [1] through [7]Booth 1213 NEW Flotation Cell Fine Coal Flotation Eriez
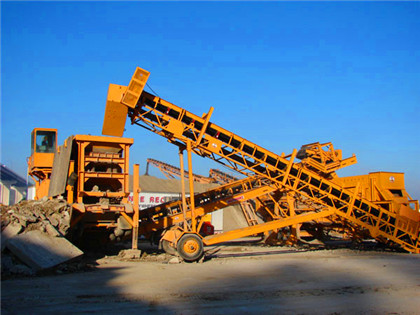
Concentrate launder design: what is right for your operation?
The external peripheral launder does not consume cell volume, so the effective cell volume for flotation is also higher This launder is predominantly used on smaller TankCells The external double launder includes a second internal launder, providing added concentrate lip length This launder design is well proven in ultrafine and high In a 2000t/d copper plant of a certain enterprise, six flotation columns with diameters of 40m, 18m, 12m, 10m and 08m were used for coppermolybde Chinese English Home Introduction Introduction Product Coppermolybdenum ore flotation column example

Minerals Processing in Mining: Getting stability in your
3 transportation of mineral particles from bulk slurry to the launder lip As the air is added to the flotation cell, bubbles rise through the slurry, up through the froth to the exposed froth Flotation columns are a newer and more advanced type of flotation equipment, consisting of a tall and narrow cylindrical vessel with a sparger at the bottom The slurry is fed into the column fromFlotation Cells vs Columns: A Comparison for Mineral
- crusher machine for concrete in india
- مصنع ميكرون المعدنية الصلبة
- آلة كسارة الفحم للمبيعاتأفريقيا المصنعين
- تهتز الشاشة لمناجم الفحم
- mobile impact crusher matso
- الرمال وعملية استغلال المحاجر الحصى خط
- مركز عروض خام الذهب كتاب مطحنة الكرة العالمية
- YGM آلة الطحن العمودي
- metal crushers mets
- خام الكروم غسل مصنع المورد