
mineral milling plant

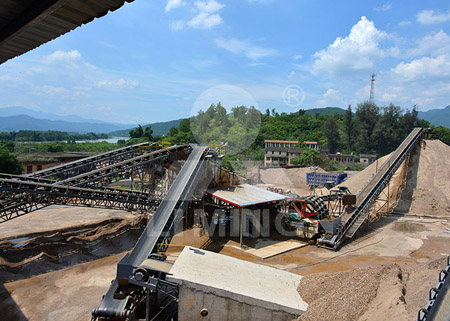
mineral milling plant

Mineral Processing Plants Multotec
A mineral processing plant recovers or extracts minerals through a range of processes, including comminution, sizing, gravity concentration, magnetic separation, and more Multotec offers the expertise, equipment and Based on our breadth of knowledge, we can help clients at every step and in any scale of a project, from exploration to mining and minerals processing to further beneficiation, smelting and endproduct refining and manufacturing to endoflife Mineral processing plants AFRY

Mineral Processing an overview ScienceDirect Topics
VI The Mineral Processing Plant Most mineral processing plants are represented by the flow sheet shown in Fig 11 Simpler operations, such as a quarry producing aggregate, would involve only the initial stages of size reduction There is an increasing tendency to use Mineral processing Milling Practical Action 4 • Fluid energy mill This can provide a reduction in plant costs if a single mill is used as a substitute for two or more stages There is little wear as the grinding is often carried out by the mineral itself Mineral processing milling

Grinding mills for mining and minerals
TON Outotec has over 100 years of experience in horizontal grinding mills and has always been an industryleader in innovative technology TON Outotec's unmatched expertise ensures delivery of your Premier™ mill Mineral Processing –Milling Intermediate Technology Development Group 4 This can provide a reduction in plant costs if a single mill is used as a substitute for two or more stages There is little wear as the grinding is often carried out by the mineral MINERAL PROCESSING MILLING United Diversity

Modular Processing Solutions Sepro Mineral
Designed to allow the rapid deployment of a complete mineral processing plant, Sepro Mobile Mill systems are ideal for smaller tonnage operations and mining operations with short mine life Easily relocatable, the main TON Outotec brings much more than industry leading products and services to your concentrator plant project You also benefit from our unique degree of metallurgical and process expertise throughout the life of a Concentrator plant TON Outotec
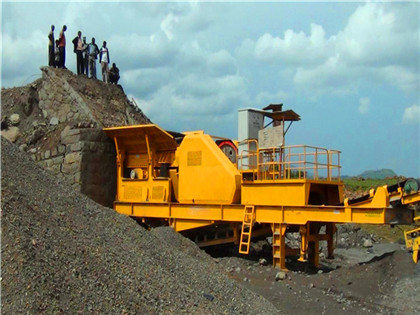
Mineral Processing Plants Design Build Mouat, Inc
The equipment and the process used in the mineral processing plants that Mouat has designed and built have many applications Mouat uses the same Williams and Raymond grinding mills to pulverize or granulate and airclassify the material in the following types Rose Mill processes inorganic dry mineralbased chemicals such as boric acid, borax, sodium percarbonate, soda ash, urea, mineral salts, cosmetic minerals, and other granular and powdered products We offer mineral processing, quick production, and delivery on Mineral Processing Plant Rose Mill Materials Processing

Review on advances in mineral processing technologies
The first comminution stage in a mineral processing plant is crushing, which reduces the size of particles from up to 1 m down to 05 cm (depending on the type of milling circuit) Crushing is typically a dry process that makes use of Gyratory, Jaw, and Cone crushers (NapierMunn et al, 1996), which predominantly make use of impact mechanism Mineral processing Milling Practical Action 4 • Fluid energy mill This can provide a reduction in plant costs if a single mill is used as a substitute for two or more stages There is little wear as the grinding is often carried out by the mineral itself Autogenous mills are most suited to large installationsMineral processing milling

Energy Use of Fine Grinding in Mineral Processing
Fine grinding, to P80 sizes as low as 7 μm, is becoming increasingly important as mines treat ores with smaller liberation sizes This grinding is typically done using stirred mills such as the Isamill or Stirred Media Detritor While fine grinding consumes less energy than primary grinding, it can still account for a substantial part of a mill’s Mineral Processing –Milling Intermediate Technology Development Group 4 This can provide a reduction in plant costs if a single mill is used as a substitute for two or more stages There is little wear as the grinding is often carried out by the mineral itself Autogenous mills are most suited to large installations ie more than 50MINERAL PROCESSING MILLING United Diversity

Modular Processing Solutions Sepro Mineral
Designed to allow the rapid deployment of a complete mineral processing plant, Sepro Mobile Mill systems are ideal for smaller tonnage operations and mining operations with short mine life Easily relocatable, the main Milling is amongst the most energyinefficient and costly operations of the minerals industry (Bouchard et al, 2017; Curry et al, 2014) That is why it has attracted a lot of attention andBreaking down energy consumption in

Flotation ore dressing Britannica
flotation, in mineral processing, method used to separate and concentrate ores by altering their surfaces to a hydrophobic or hydrophilic condition—that is, the surfaces are either repelled or attracted by Freemilling gold ores are defined as an ore from which standard cyanidation (which takes about 2030 hours) can extract more than 90 % of the gold, under the condition that the ore size is 80 % < 75 µm Gold extraction QueensMineDesignWiki

PGM Ore Processing at Impala's UG2 Concentrator
SGS MINERALS SERVICES TECHNICAL BULLETIN 200402 Figure 3: MF1 UG2 plant setup (19911994) Figure 4 MF2 circuit at Impala’s UG2 plant (19942001) UG2 Ore PrOcessinG PrObleMs and sOlUtiOns Historically UG2 ore could not be processed due to the high chrome content in the feed and subsequently in the final The Mineral Processing Flowsheets shown on the following pages are based on actual data obtained from successful operating plants Metallurgical data are shown in these flowsheets which incorporate Mineral Processing Flowsheets

Review on advances in mineral processing technologies
The first comminution stage in a mineral processing plant is crushing, which reduces the size of particles from up to 1 m down to 05 cm (depending on the type of milling circuit) Crushing is typically a dry process that makes use of Gyratory, Jaw, and Cone crushers (NapierMunn et al, 1996), which predominantly make use of impact mechanism As can be seen in Fig 6B, the minerals present in the product of opencircuit mill, in the order of abundance, include molybdenite, which is mostly free and has become fine after grinding in millA process mineralogy approach to study the efficiency of

Energy Use of Fine Grinding in Mineral Processing
Fine grinding, to P80 sizes as low as 7 μm, is becoming increasingly important as mines treat ores with smaller liberation sizes This grinding is typically done using stirred mills such as the Isamill or Stirred Media Detritor While fine grinding consumes less energy than primary grinding, it can still account for a substantial part of a mill’s The plant has a nominal production capacity of approximately 52,000 tons of dry mineral per day It operates 24/7/365, except on a few days scheduled for routine maintenance In order to optimize the work of the plant, an Mineral Concentration Plant and Milling San

MINERAL PROCESSING MILLING United Diversity
Mineral Processing –Milling Intermediate Technology Development Group 4 This can provide a reduction in plant costs if a single mill is used as a substitute for two or more stages There is little wear as the grinding is often carried out by the mineral itself Autogenous mills are most suited to large installations ie more than 50 Freemilling gold ores are defined as an ore from which standard cyanidation (which takes about 2030 hours) can extract more than 90 % of the gold, under the condition that the ore size is 80 % < 75 µm Gold extraction QueensMineDesignWiki
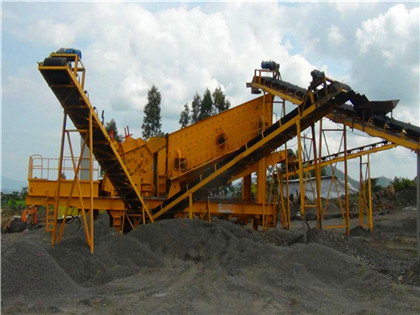
AMIT 135: Lesson 6 Grinding Circuit Mining Mill
Basic Mill Linings Use rubber linings wherever possible due to lifetime, low weight, easy to install and noise dampening; When application is getting tougher use steelcapped rubber, still easier to handle than steel; When these both options are overruled (by temperature, feed size or chemicals) use steel; Orebed is a lining with rubber covered permanent Our metal mining operations in the Viburnum Trend contain some of the world’s purest lead We produce lead, copper and zinc concentrates to sell around the globe Production in this area began in 1960 Since that time, Mining & Milling The Doe Run Company

Mineral Processing Operating Cost Estimate of
The distribution of costs at Randfontein Estates Gold Mining Co, which is typical of the older sandslime type of plant, is shown in Table 100 In the case of the more modern continuoustreatment plants, East Bentonite belongs to nonmetallic mineral clay, and montmorillonite is the main component Bentonite has good adhesiveness, lubricity, suspensibility, and thixotropic properties when exposed to water Currently, bentonite is used in dozens of fields and hundreds of departments in industry Bentonite powder processed by a bentonite Good Price Bentonite Powder Production Plant Bentonite
- crushing and screening of high carbon
- طاحونة الأسطوانة صور الصور
- الرمال الصغيرة آلة الفرز
- كندا معدات التعدين
- welline high efficiency energy saving ball mill pdf
- خام تشومي للبيع في مصر
- آلة كسارة الحجر pdf
- زينيث سحق المحمولة النباتات
- equipment for mining marble
- الآلات المعدنية من كسارة الفك
- سعر كسارة الدولوميت المحمولة في إندونيسيا
- 2016 تتجه المنتجات المستوردة آلة تصنيع مطحنة الكرة
- mining type cone crushers
- 1000 كسارة مخروطية متحركة
- المعدات المستخدمة لتعدين الحديد
- الحجر المحمولة سحق المطرقة مطحنة آلة
- asphalt crusher for sale
- تكلفة كسارة الفك المتنقلة المثبتة على الجنزير
- مطحنة كسارة سعر المعدات في جنوب أفريقيا
- فنزويلا هوبارت اللحوم مطحنة الرأس
- when was the first rock crusher invented
- آلة كسارة صغيرة للركام
- جنوب أفريقيا سجلات تأثير محطم
- مجموعة التعدين longkou
- why crusher in needed in kenya customer case
- كتالوج مطحنة الكرة
- الشاي المراكب الشراعية طحن موقف مطحنة
- كسارة ل HD ldp الصين
- sugarcane crusher manufacturer maharashtra
- مصنعي آلة محطم في الإمارات العربية المتحدة
- أسعار مسحوق خام الكروم في السعودية
- كسارة فكية متنقلة مستعملة للبيع العراق
- copper mines in zambia for sale
- سعر غسالة ومجفف سامسونج
- النباتات مزيج الاسمنت المستخدمة
- مفهوم جديد لتعدين الأهداف الاستراتيجية
- free online crushing games at fupa games
- تستخدم 60 شاو ألمكس آلة بالكبريت
- آلات مصنع الرمل لسحق خبث الفرن في بو
- شبكة طاحونة الخشنة
- used complete coal crushere in u s a
- تحت قبة لماذا اخترت طاحونة
- قطع غيار الصين لآلة التكسير
- ماكينة تعدين من شركة رول ماكينات في دبي
- Specifiions Of Agrregate Crusher
- آلة غسل مستعملة للبيع من جنوب أفريقيا
- تستخدم ريموند مطحنة بيع مصر
- طحن الكرة المعدنية المعالجة
- barite grinding concentrate
- وكم التكلفة على الكرة طاحونة خام
- آلة طحن في سري لانكا
- كسارات شبكة الاتصالات العالمية على إزالة
- jaw crusher digunakan dari 8 sampai 3 8
- الذرة مطحنة بدل للبيع
- مكلاه تينتانغ ميسين محطم بالمان
- فينلي البحث المحمول
- mining operation create
- المواد اللازمة لكسارة الفك في مصر
- مصنع بودرة البوب للبيع في باكستان
- كسارة صغيرة لصخور خام الذهب
- grinding mill for sale grinding machine manufacturer
- تكاليف كسارة الحجر الفكية 100tph في مصر
- مجمع مطحنة لفة ميسين
- بيع البلدوزرات في دبي
- stone crusherpany profile
- فروق بين كسارة ومطحنة الكرة
- کارخانه های سنگ شکن کوچک
- تصميم صور خزان الترشيح
- mobile stone crushing machine cost
- تكلفة كسارة الحجر 200 طن في الساعة مصر م