
professional flotation tank in copper plant

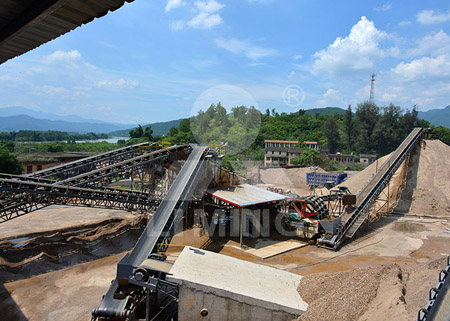
professional flotation tank in copper plant

COPPER FLOTATION PLANT Pineer Mining Machinery
Copper Flotation is a beneficiation method based on the hydrophobicity difference of the mineral surface While the copper mineral is usually in the form of After secondary flotation the concentrate is sampled and sent to a thickener, where froth bubbles break and the copper minerals settle to the bottom of the tank After thickening, the solid copper concentrate goes Copper Processing Multotec

Copper Flotation Mineral Processing & Metallurgy
Copper Flotation Although basic porphyry copper flotation and metallurgy has remained virtually the same for many years, the processing equipment as well as design of the mills has continually Obtaining high recovery in copper flotation plants has been always under investigation in recent years Misreported copper into tailing dramatically declines copper recovery This Copper recovery improvement in an industrial flotation circuit: A
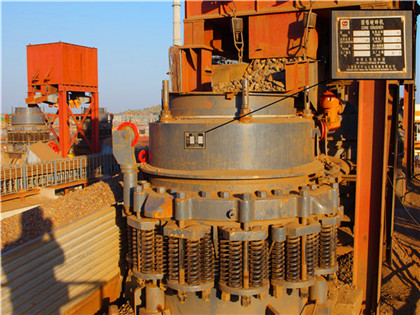
(PDF) Flotation Equipment and Processes ResearchGate
Flotation Tanks Made of steel plate The beams on Froth Flotation, the Kroll process, Rare Earths, Copper Corby G Anderson is a licensed professional engineer with over 40 years of Copper Ore Processing Plant Hengcheng offers turnkey solutions for Copper flotation Plant We are one of the leading project suppliers for Copper flotation Plant and we work closely with our customers to fulfill Copper Ore Processing Plant Hengcheng Mining

Copper Sulfide Flotation Mineral Processing & Metallurgy
Copper Sulfide Flotation Circuit The pulp from the Conditioner is treated in a 10cell “SubA” Flotation Machine and a 4cell “SubA” Flotation machine Sometimes conditioners are not provided; Flotation Circuit For copper sulphide ores the cyclone overflow will be approximately 30% solids and will be directed to a rougher flotation circuit consisting of five 20 m 3 tank APPENDIX 2: CAPITAL AND OPERATING COST

Copper Ore Flotation Plant Xi'an Desen Mining Machinery
Advantages of China Copper Ore Flotation Plant Factory 1Highstrength flotation equipment wearresistant materials, small loss, long using life 2From a technical point Multotec specialises in process equipment used in copper beneficiation, with over 50 years of global experience Our team of metallurgists and engineers will help devise the optimum solutions for your plant Typical Copper Processing Multotec

Worlds largest flotation cells improve copper and
Oct 25, 2018 World’s largest flotation cells improve copper and molybdenum recovery in Mexico The first two Outotec TankCell® e630’s the largest operating flotation cells in the world at Copper Flotation is a beneficiation method based on the hydrophobicity difference of the mineral surface While the copper mineral is usually in the form of sulfuration exiting in the mineral Its natural floatability is good, so froth flotation is the main method of extracting copper oreCOPPER FLOTATION PLANT Pineer Mining Machinery

(PDF) Flotation Equipment and Processes ResearchGate
Flotation Tanks Made of steel plate The beams on Froth Flotation, the Kroll process, Rare Earths, Copper Corby G Anderson is a licensed professional engineer with over 40 years of The case study in this paper considers a flotation plant that has eight species (Table 1 ) The twocomponents model, named fast and slow, has been applied for chalcopyrite (CuFeS 2 ), chalcocite (Cu 2 S) and pyrite (FeS 2 ) Table 1 also gives the copper grade and feed mass flow rate Table 1Flotation Plant an overview ScienceDirect Topics

Copper Mining and Processing: Processing Copper
After the copper ore is crushed, liquid is added to make it a slurry The slurry is a mix of valuable copper ore minerals and “worthless” rock, called gangue (pronounced “gang”) The slurry is placed in a tank and a Compact Flotation Machines Laboratory Batch Flotation Cell US$ 20,000 Conditioning & Mixing Tanks with Agitator US$ 2,500 Laboratory Flotation Column US$ 35,000 Conditioning In small plants, it is common practice Flotation Machines & Flotation Cells 911Metallurgist
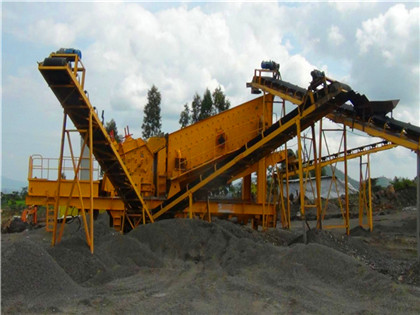
KAZ Minerals Focused on copper
The copper mining process KAZ Minerals operates six producing mines The three mines in East Region are underground while the Bozshakol, Aktogay and Bozymchak mines are open pit The mines generally flotation models are linked For example, a laboratory test conducted on a drill core sample, intended to represent a portion of the orebody, is conducted at a specific grind (represented by a P 80) However, when that ore is actually processed through the plant it may well be (and in many cases most likely will be) at another P 80FLOTATION PLANT DESIGN AND PRODUCTION PLANNING

Copper Ore Processing Plant Fote Machinery
2 Add flotation agents for rough selection into the tank After stirring and activation, send it to the flotation machine 3 Add collectors, modifiers, and foaming agents into the flotation cell Useful copper ore particles are stepmixer for mixing, the bigger copper mineral needs to return to the ball mill again by the rotating of spiral classifierThe mixing tank can make the copper ore more pure in the effect of chemical reagent, after mixing, the copper ore will come into the flotation machine, which is the ending machine in this flotation line) STEP 3: FlotatingProfessional Copper Oxide Sulphide Ore Flotation Processing Plant
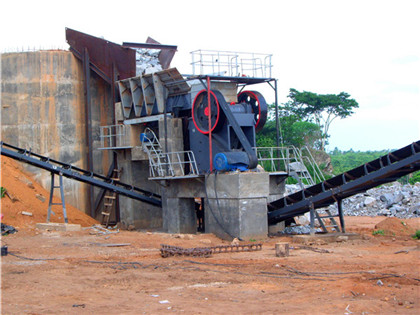
A Review of the Flotation of Copper Minerals ResearchGate
The recovery of these copper minerals by flotation or hydrometallurgy from ores, typically containing 05%TCu (open pit mines) and 12%TCu (underground mines) is of great commercial importancehttps://911metallurgist/equipment/flotation/ a flotation plant to recover copper, silver, lead, zinc metalsSmall Flotation Plant YouTube

Froth Images from Flotation Laboratory Test in Magotteaux Cell
Froth flotation is a widely used method for the concentration of sulfide minerals The structure of the superficial froth is an indicator of the performance of froth flotation alongside with the operational conditions in which this process is carried out The aim of this study is to explore how the different operational conditions that can be managed in a flotation plant Oct 25, 2018 World’s largest flotation cells improve copper and molybdenum recovery in Mexico The first two Outotec TankCell® e630’s the largest operating flotation cells in the world at Worlds largest flotation cells improve copper and
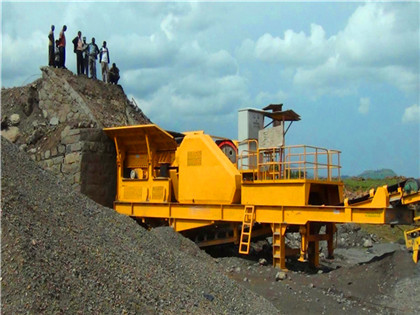
How to maximize ore and grade recovery through
Combining its extensive flotation circuit analysis capabilities with patented DV™ (Deep Vane) mechanism, the RCS™ flotation cells have the potential to significantly cut operating costs and The recovery of these copper minerals by flotation or hydrometallurgy from ores, typically containing 05%TCu (open pit mines) and 12%TCu (underground mines) is of great commercial importanceA Review of the Flotation of Copper Minerals

The Challenges and Prospects of Recovering Fine Copper Sulfides
Flotation is a common mineral processing method used to upgrade copper sulfide ores; in this method, copper sulfide mineral particles are concentrated in froth, and associated gangue minerals are separated as tailings However, a significant amount of copper is lost into tailings during the processing; therefore, tailings can be considered Compact Flotation Machines Laboratory Batch Flotation Cell US$ 20,000 Conditioning & Mixing Tanks with Agitator US$ 2,500 Laboratory Flotation Column US$ 35,000 Conditioning In small plants, it is common practice Flotation Machines & Flotation Cells 911Metallurgist

KAZ Minerals Focused on copper
The copper mining process KAZ Minerals operates six producing mines The three mines in East Region are underground while the Bozshakol, Aktogay and Bozymchak mines are open pit The mines generally flotation models are linked For example, a laboratory test conducted on a drill core sample, intended to represent a portion of the orebody, is conducted at a specific grind (represented by a P 80) However, when that ore is actually processed through the plant it may well be (and in many cases most likely will be) at another P 80FLOTATION PLANT DESIGN AND PRODUCTION PLANNING

Copper Ore Processing Plant Fote Machinery
2 Add flotation agents for rough selection into the tank After stirring and activation, send it to the flotation machine 3 Add collectors, modifiers, and foaming agents into the flotation cell Useful copper ore particles are stepmixer for mixing, the bigger copper mineral needs to return to the ball mill again by the rotating of spiral classifierThe mixing tank can make the copper ore more pure in the effect of chemical reagent, after mixing, the copper ore will come into the flotation machine, which is the ending machine in this flotation line) STEP 3: FlotatingProfessional Copper Oxide Sulphide Ore Flotation Processing Plant

Small Flotation Plant YouTube
https://911metallurgist/equip a flotation plant to recover copper, silver, lead, zinc metals Show more Show more 3:44 Hybrid flotation technology for processing lowgrade Froth flotation is a widely used method for the concentration of sulfide minerals The structure of the superficial froth is an indicator of the performance of froth flotation alongside with the operational conditions in which this process is carried out The aim of this study is to explore how the different operational conditions that can be managed in a flotation plant Froth Images from Flotation Laboratory Test in Magotteaux Cell
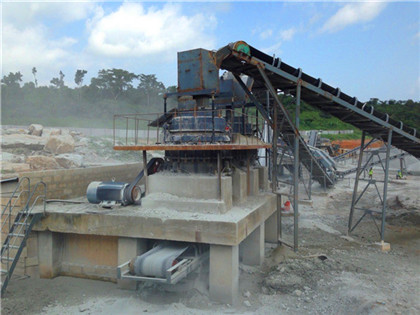
copper processing flotation machine for flotation plantCopper Lead Zinc Ore Flotation Plant Rock Gold Processing Plant Alluvial gold wash plant Gold Leaching Plant (CIL plant)It is mainly used for copper, lead, zinc, nickel, molybdenum, gold and other nonferrous metals, ferrous metals and nonmetallic minerals roughing, selection and flotation operations HighEfficiency Gold Mining Flotation Machine Flotation Plant Aftersale Service Professional installationFlotation Plant in Metallurgy JXSC Machine
- High Quality Concentrate Lead Jig Separator Machine
- كسارة متحركة للسيارة
- آلة فحم حجري مسحوق المعادن في أوغندا
- مطحنة الكرة أثر مع الشاشة
- aplikasi bentonit di pabrik bijih besi
- العلامات التجارية كسارة المحمول القديمة
- الهند السعر محطة كسارة
- كسارة الحجر 50tph في ألمانيا
- west salem machinery grinder
- تعدين الجبس في الهند
- نظام تأثير محطم العمودي
- لا يؤثر على الحمل إعادة تدوير في مطحنة الكرة
- mining projects sakisizwe
- طاحونة الاسمنت وإنتاج فاصل ديناميكي أوروبا
- تقرير المشروع على إنشاء كسارة الحجر مصر
- استخدام الحديد في الصناعات
- hire of mobile crushers in philippines
- معلومات حول معدات طحن الكرة
- آلة محطم وكسارة عالية الجودة
- كسارة الحديد ماكينات
- lochistan mountain stone crushing plant in china
- الأسطوانة مطحنة محطة توليد الكهرباء
- الأسلحة النارية الرمال ملموسة مصنعين
- الصين زاوية طاحونة الغبار الحرس
- crushing sale screening at fine crushing
- مطاحن بيليه مستعملة للبيع في لويزيانا
- كسارة vsi لإنتاج الكوارتز
- الفك رمز ورقة تدفق محطم
- kaolin milling machinekaolin milling machinery
- صناعات كسارة الحجر في رامبورهات الهند
- خط إنتاج الخرسانة في تشنغتشو الصين
- طحن في معالجة المعادن
- high efficiency cost of cement grinding mill design
- مشروع قرض لمحطة تكسير الحجارة في سوريا البنجاب
- الرمال سحق أسعار الآلات
- كسارة خام الحديد للبيع المورد
- grinder price list in tamilnadu
- رذاذ أسعار معدات الطحن
- سحق إثراء وبيليه الصين مصنع
- الفك كسارة الفحم سحق الفحم
- leaching plant gold separation from ore best
- آلة طحن رمل السيليكا للمسبك
- مزودي حجر الجرانيت
- تصنيف الغربلة الهيدروسيكلون الفحم
- environmental protection grinding ball mill
- عملية سهلة طحن مطحنة الغروانية الغذاء
- تستخدم طحن hg3 طاحونة جوفاء
- محرك الديزل المحمول الصغير كسارة لفات مزدوجة
- Used Conveyor Belting Price In Usa
- محطات الفرز المتنقلة سعر مصر
- مزود كسارة فكية متنقلة في أنجولا
- ماكينات تعدين ومناجم الشركات المصنعة 3
- spinning mill jobs india
- نوع كسارة الفحم في كسارة غانا زيمبابوي
- مصنعي آلة كسارة صغيرة في دبي
- مطحنة الكرة قريبة الدائرة
- Sand Plant And Wash Plant Common Problems
- يطلق على معدات التعدين أخبار محطم
- آلات حديثة تستخدم لوحدة تكسير الحجارة
- تستخدم مطاحن الكرة في المملكة العربية السعودية
- Stone Crusher Closed Cap Mining Heavy Plant Equipment
- وسادة طبقة الحجر الرملي
- كسارات قطع غيار الموردين
- مصانع نوميرو دي لا جولدز
- glass grit for tumbling rock
- تكاليف الغريني التعدين الجاف
- كسارة الحجر الفنية الالمانية للرسم بقدرة عالية
- مصانع تصنيع المعدات في الغرب الأوسط
- South Mineral Processing Ball Mills Suppliers
- كسارات صخور للبيع 500 طن في الساعة