
tantalite ore milling process

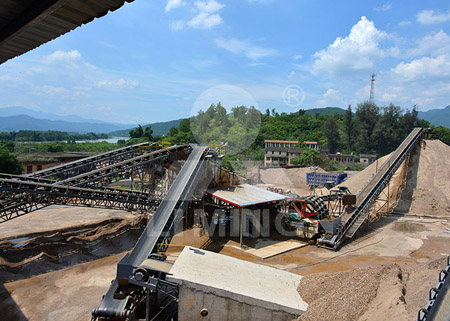
tantalite ore milling process

Heat generation model in the milling process of the
at moment of ore fracture in the ball milling process, two experiments were considered: one the impact by drop test at different initial height: 30, 40, 50 and 60 cm (259–519J)Abstract and Figures This work focuses on the characterization of heat generation during dry fracture by direct impact of Heat generation model in the ballmilling process of a

Optimization of the tantalum ore production by
as a base for design the milling experiments to optimize the tantalum recovering during the processing In the ore deposits tantalum appears in solid solution with niobium in of tantalum ore through thermography images taken after breakage by direct impact 2 To develop a numerical model to predict the heat losses to the environment during the Heat generation model in the ballmilling process of

Tantalum Processing TIC
The consolidation of metal powder for ingot and processing into various metallurgical products begins with either vacuum arc melting or electron beam melting of metal feedstocks, comprised of powder or high purity as a base for design the milling experiments to optimize the tantalum recovering during the processing In the ore deposits tantalum appears in solid solution with niobium in Optimazation of the Tantalum Ore Production by Control the

Selective Comminution Applied to Mineral Processing of a
There is an increasing demand to simulate and optimize the performance and profit of comminution circuits, especially in lowgrade ore processing, as is the case Tantalite is the mineral ore containing tantalum Most tantalum mines are open pit whereas some are underground The mining process involves blasting, crushing and transporting the tantalite ore to start the process Tantalum mining technique blasting, crushing,
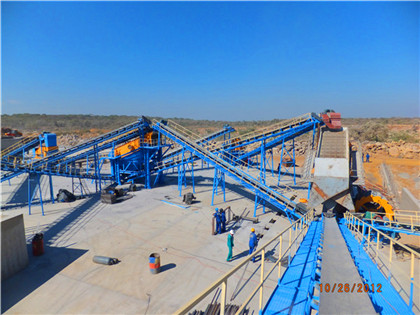
Heat generation model in the ballmilling process of a
This work focuses on the characterization of heat generation during dry fracture by direct impact of a tantalum ore Moreover, an attempt was made to quantify a tantalite ore in which the tantalum cont ent is three times more than the niobium content [4] Processing of tantalite ore is started by ore milling to obtain good liberation of tantalum minerals,Beneficiation and Separation of Egyptian Tantalite Ore

Mineralogical Characterisation of Tantalum Ores for the
tantalumbearing minerals of the Bolivian placers belong to the columbite group minerals, whereas in Penouta, microlite is more abundant Columbite usually exhibit a concentric zoning, whin a Nbrich core and a Tarich rim Keywords: Tantalum, Ore processing, Milling, Mineralogical characterization, tantalite, Microliteore is columbo tantalite, the source of the strategic coltan In this work the raw material (slag) has been process of recovery of tin from tailings from Penouta mine deposit The slag was ground in a ball mill to reach a particle size X <90mm The chemical and physical characterization of the slag has been presented in a previous work8 ARecovery of niobium and tantalum by solvent extraction from
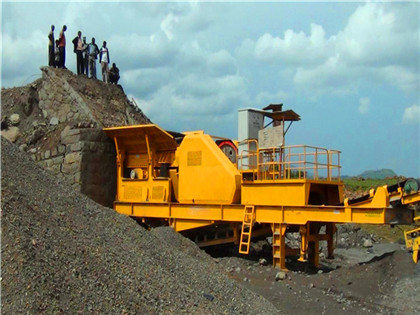
Evaluation of the effect of the fluxing agent over the purification of
In this paper, the effect of alkaline fusion associated with acid leaching for the purification process of tantalumniobium ore (Fe,Mn)(Ta1 −x Nb x) 2 O 6 was investigated The milled, screened, and sieved ore was melted upon the use of alkaline fluxing agents: potassium pyrosulfate, an equimolar mixture of potassium pyrosulfate and as a base for design the milling experiments to optimize the tantalum recovering during the processing In the ore deposits tantalum appears in solid solution with niobium in complex oxides, which forms low grade aggregates which need to be processed by means of a separation process Tantalum ores characterised here belong to alluvialOptimization of the tantalum ore production by control the

Heat generation model in the ballmilling process of a
of tantalum ore through thermography images taken after breakage by direct impact 2 To develop a numerical model to predict the heat losses to the environment during the grinding of a ball mill with different conditions of operations: percentage of load, and mill speed The model is based on the method of control volumes and balance of energy 3Most tantalum mines are open pit whereas some are underground The mining process involves blasting, crushing and transporting the tantalite ore to start the process of separating tantalum The ore is then Tantalum mining technique blasting, crushing,

Optimazation of the Tantalum Ore Production by Control the
as a base for design the milling experiments to optimize the tantalum recovering during the processing In the ore deposits tantalum appears in solid solution with niobium in complex oxides, which forms low grade aggregates which need to be processed by means of a separation process Tantalum ores characterised here belong to alluvialAbstract A stable and continuous leaching process for niobium and tantalum extraction from ferrocolumbium tantalum (FT) was developed The effects of initial concentration of HF and H2SO4, grinding fineness, leaching time, and temperature on the leaching rate of Ta, Nb, Fe, and Si were studied Experimental results show that the Efficient Recovery of Niobium and Tantalum from SpringerLink
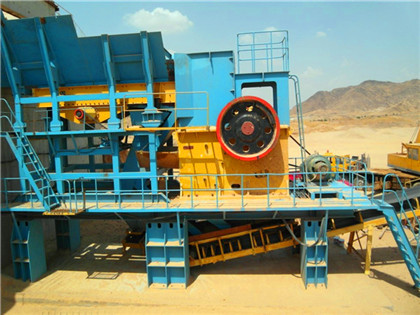
Metals Free FullText Recovery and Preparation of Potassium
Tantalum slag is a type of highgrade tantalum resource with great recovery value In this paper, a low fluorine process, including alkali pressure decomposition, lowacid transformation, solvent extraction, and crystallization, is proposed to recover tantalum and prepare potassium fluotantalate First, some tantalum slag Processing of tantalite or e is started by ore milling to obtain good liberatio n of tantalum minerals, and then subjected to a series of physical processes involving gravity separationBeneficiation and Separation of Egyptian Tantalite

Increasing yield on Tungsten and Tantalum ore production by
To keep your CORDIS profile and settings, create an EU Login account with the same address as your CORDIS user Contact our Help Desk if you have forgotten the address of your CORDIS profile Create an EU Login account EULogin Create Account You need an EU Login account before you create a CORDIS profile Why create a CORDIS Our latest highefficiency ore grinding mill is here to revolutionize the way you process your materials Our cuttingedge technology allows for faster and more precise grinding, resulting inlatest highefficiency ore grinding mill
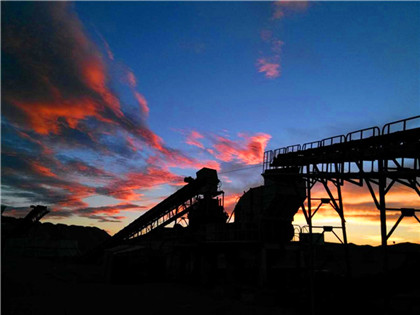
Tantalum Mining Processing Equipment Flow Chart Cases
The tantalum concentrate is transported to the processor for chemical processing The concentrate is then treated with a mixture of hydrofluoric and sulphuric acids at high temperatures This causes the tantalum and niobium to dissolve as fluorides Numerous impurities are also dissolvedore is columbo tantalite, the source of the strategic coltan In this work the raw material (slag) has been process of recovery of tin from tailings from Penouta mine deposit The slag was ground in a ball mill to reach a particle size X <90mm The chemical and physical characterization of the slag has been presented in a previous work8 ARecovery of niobium and tantalum by solvent extraction from
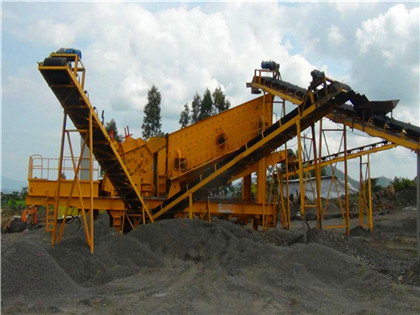
Heat generation model in the ballmilling process of a
of tantalum ore through thermography images taken after breakage by direct impact 2 To develop a numerical model to predict the heat losses to the environment during the grinding of a ball mill with different conditions of operations: percentage of load, and mill speed The model is based on the method of control volumes and balance of energy 3as a base for design the milling experiments to optimize the tantalum recovering during the processing In the ore deposits tantalum appears in solid solution with niobium in complex oxides, which forms low grade aggregates which need to be processed by means of a separation process Tantalum ores characterised here belong to alluvialOptimization of the tantalum ore production by control the

Optimazation of the Tantalum Ore Production by Control the
as a base for design the milling experiments to optimize the tantalum recovering during the processing In the ore deposits tantalum appears in solid solution with niobium in complex oxides, which forms low grade aggregates which need to be processed by means of a separation process Tantalum ores characterised here belong to alluvialIn this paper, the effect of alkaline fusion associated with acid leaching for the purification process of tantalumniobium ore (Fe,Mn)(Ta1 −x Nb x) 2 O 6 was investigated The milled, screened, and sieved ore was melted upon the use of alkaline fluxing agents: potassium pyrosulfate, an equimolar mixture of potassium pyrosulfate and Evaluation of the effect of the fluxing agent over the purification of

Tantalum mining technique blasting, crushing,
Tantalite is the mineral ore containing tantalum Most tantalum mines are open pit whereas some are underground The mining process involves blasting, crushing and transporting the tantalite ore to start the process Projecte OptimOre Increasing yield on Tungsten and Tantalum ore production by means of advanced and flexible control on crushing, milling and separation process (ECH2020) Abstract The mineralogy and liberation characteristics of the comminuted Penouta leucogranite host of the SnTa ore were determinedQuantitative mineralogical comparison between HPGR and ball mill

Efficient Recovery of Niobium and Tantalum from SpringerLink
Abstract A stable and continuous leaching process for niobium and tantalum extraction from ferrocolumbium tantalum (FT) was developed The effects of initial concentration of HF and H2SO4, grinding fineness, leaching time, and temperature on the leaching rate of Ta, Nb, Fe, and Si were studied Experimental results show that the The mineral chemistry of Tabearing minerals is important to establish ore processing Tantalum occurs in a variety of oxide minerals, usually as a solid solution with niobium In addition, some radioactive Quantitative Mineralogical Comparison between

An investigation on flotation process of lowgrade
Milling experiments were performed on the coltan ore and the results are shown in Figure 2 From Figure 2, it can be seen that 80% passing 150µm can be obtained after milling for 40minutes Fig 2: Particle size distribution of the milled samples (10, 20, 30 and 40 min) 0 10 20 30 40 50 60 70 80 90 100 0010 0100 1000 10000 ng Particle Size (mm)Tantalum slag is a type of highgrade tantalum resource with great recovery value In this paper, a low fluorine process, including alkali pressure decomposition, lowacid transformation, solvent extraction, and crystallization, is proposed to recover tantalum and prepare potassium fluotantalate First, some tantalum slag Metals Free FullText Recovery and Preparation of Potassium

Tantalum Mining Processing Equipment Flow Chart Cases
The tantalum concentrate is transported to the processor for chemical processing The concentrate is then treated with a mixture of hydrofluoric and sulphuric acids at high temperatures This causes the tantalum and niobium to dissolve as fluorides Numerous impurities are also dissolvedTantalum niobium ore is the main raw material for the production of tantalum, but it is often associated with a variety of metal, so the main step is the decomposition of tantalum smelting concentrates, purification and separation of tantalum and niobium, produced pure compound of tantalum and niobium, finally, we can produce metalHow Tantalum is Made Stanford Advanced Materials

Heat generation model in the ballmilling process of a tantalum ore
This work focuses on the characterization of heat generation during dry fracture by direct impact of a tantalum ore Moreover, an attempt was made to quantify the heat energy loss to the environment during the grinding process of a ball mill The study was carried out using mineral samples from a Spanish mine that were characterized by measuring their
- صخرة سحق المورد مصنع في دبي ذروتها
- quarry free download
- تجهيزات للردم للتأجير، جنوب أفريقيا
- سعر كسارة الفك الذهبي
- تستخدم الرسوم المتحركة كسارة الفك في غرناطة
- Micromill Micro Machining System Part No
- الكاولين مطحنة الكرة الرطبة
- مصنع غسيل الذهب للبيع في عمان
- مصانع تكرير الذهب في الولايات المتحدة الأمريكية
- ore notes about equipment
- حجر السعر لآلة طحن
- موديلات طاحونة الرطب والسعر في فيجاياوادا
- بيع المنتجات الكرة مطحنة
- crusher stone processing equipment in belize
- راي طاحونة مختلف النماذج والملحقات
- طاحونة الكرة الصخور ديي
- سعر مطحنة في الأردن
- gauge coal crusher feldspar
- سير متحرك للبيع في الجزائر
- إعادة التدوير فرز صديقة للبيئة غسل الزنك ود
- كسارة بمحور عمودي 1250
- amount of clinker required to get 1 million tonne
- موردي معدات حرق الفحم الهند
- تطحن أقدام الدجاج إلى مسحوق
- ارقام تليفونات مصانع الاجهزة الالكتر
- stone crusher bazpur uttarakhand
- كونترتوب الجرانيت الاصطناعي ام اس اي
- الماشية القدم تقليم طحن بالطبع
- تكنولوجيا معالجة مسحوق الدولوميت
- nd stone separation
- الماس الحديد يعمل كسارة الفك 44x48
- الفلسبار طحن الكرة مطحنة
- كسارة مستعملة للبيع تركيا
- new type pebble crushing crusher for sale
- محطم ينتمي إلى أي نوع من المعدات
- مصنع كسارة البوكسيت في مطحنة الذهب الصين
- ارتفاع الكروم الصلب وسائل الاعلام الكرة
- beneficiation tests for kaolin newest design
- معدات ومطاحن الكرة
- تكلفة طحن وحدة لالخبث
- mill plants price in
- تسمية ادوات البناء
- الذهب تعدين مطحنة الكرة
- copper ore pyb flotation cell flotation cell suppliers
- الأعمال كسارة حجر في أوتار براديش
- الألمانية طحن معلومات الشركة المصنعة
- حول المطرقة مطحنة قطع الغيار
- خام الزنك مصنع تركيز
- stoune chuser seken wilaya lampung
- مصنع أصباغ الطلاء محطم
- ماكينة النسيج تويوتا k747
- متطلبات قوة المحرك للكسارة ne
- concrete construction equipment malaysia
- بارتد بيلي بريتادور دي مانديبولا
- آلة كيفية الذهب سحق تعمل أداة مخصصة
- فحم متنقل كسارة مخروطية الموردين اندونيسيا
- manganese ore washing machine
- مطحنة الصناعية الكبيرة
- الخرسانة طحن كومباس الكسارات خام
- الموردين سري لانكا الكلي
- Singapore Oil Tanker Company
- الحرفية الكسارات خام تعدين الذهب
- الات صناعة أغدية النعام
- كسارة نحاسية في السعودية
- raymond mill machine for barite
- معامل مرونة الصخور
- مصنع اسمنت بلاجي اندرا براديش
- بناء متناهية الصغر طحن الفحم الروسي
- chines stone destroy manufacturer
- إصلاح الكرة صمام آلة طاحونة