
tons hour closed cirtcuit iron ore plant

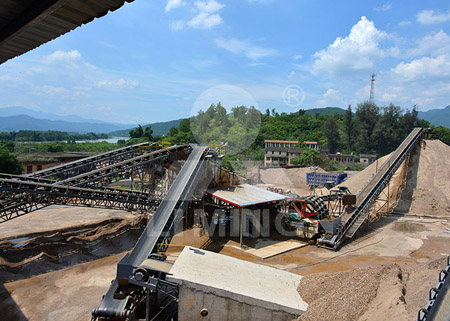
tons hour closed cirtcuit iron ore plant
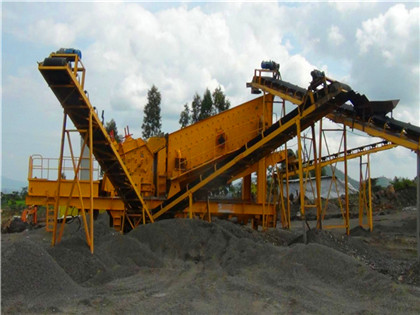
Comminution and classification technologies of iron ore
The three primary and secondary crushing stations each crush 5000 tons of ore an hour (t/h) into particles smaller than 150 mm clinker, slag, iron ore, iron ore pellet plant feed and diamond ore There are now approximately over 500 machines Where T = tons of ore per hour and Q = tons of added water per hour or T = tons of ore (for batch determinations) and Q = Common & Basic Formulas for Mineral Processing

Simple Grinding Circuits & Flowsheets Mineral Processing
Simple 1 “Closed Circuit” Ball Mill with Cyclone Grinding Circuit/Flowsheet This is the path that the ore takes in this circuit The ore comes from Prepared by Cris Candice Tuck [(703) 648–4912, ] IRON ORE1 (Data in thousand metric tons of usable ore unless otherwise noted) Domestic Production and Mineral Commodity Summaries 2022 Iron Ore USGS

Iron and steel industry in the United States
In 2022, the United States was the world’s thirdlargest producer of raw steel (after China and India), and the sixthlargest producer of pig iron The industry produced 29 million metric tons of pig iron and 88 million tons of steel Most iron and steel in the United States is now made from iron and steel scrap, rather than iron ore The United States is also a major importer of iron and steel, as well as iron and steel products The goal of any crushing plant is to produce the required material sizes at the lowest cost per ton With small changes to their existing crushing and screening circuits, such as adjustments to the crusher 3 Steps for Optimizing Your Processing Plant to Increase

AMIT 135: Lesson 6 Grinding Circuit Mining Mill
SAG Mill Circuit Example — Gold Processing SAG mill circuit example for gold processing [image: (13563)] AG/SAG Mill AG/SAG mills are normally used to grind runoffmine ore or primary crusher product Wet grinding On April 20, the 300 tons/hour iron ore processing system designed and manufactured by Shanghai Ateric Heavy Industry was delivered as scheduled This set of processing system through my The 300 tons/hour iron ore processing system was

closed circuit of iron ore plant YouTube
Contact Us: wwsstonecrushersolution/solutions/solutionshtmlIron Ore US Iron Ore Changes Since 2018 April 21, 2022 1 ²Consolidation –Cliffs acquires AK Steel and ArcelorMittal USA in 2020 Two largest US Iron Ore Overview musw
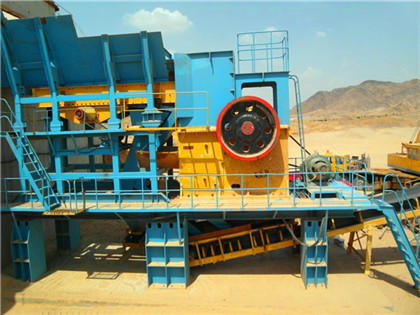
Comminution and classification technologies of iron ore
Iron ore is one of the main raw materials to make steel About 98% of the mined iron ore is used to make steel either by the blast furnace—basic oxygen furnace (BFBOF) route or through the electrical arc furnace (EAF) route The majority of world crude steel is made from the BFBOF routeThe aim of this study was to evaluate and compare two grinding circuits in an industrial iron ore plant, by evaluating the current operation through sampling, industrial data analysis and[PDF] Evaluation of grinding circuits for iron ore ResearchGate

Simple Grinding Circuits & Flowsheets Mineral Processing
To design a circuit there is some information that has to be learned The HARDNESS OF THE ORE, the TONNAGE that has to be ground per hour and the DEGREE TO WHICH IT MUST BE GROUND Once these three pieces of information has been discovered the design of the circuit can beginIron Ore US Iron Ore Changes Since 2018 April 21, 2022 1 ²Consolidation –Cliffs acquires AK Steel and ArcelorMittal USA in 2020 Two largest US integrated steel producers (Cliffs & USS) now control all US iron ore production ²Cliffs HBI plant in Toledo goes online in 2020 ²Ore prices dip in Q1 2020 and COVID idles Iron Ore Overview musw

Mineral Processing Plant Design & Construction
The jaw opening is maintained at 1″ The crusher discharge, along with the grizzly undersize, is transported on a 14″ x 65′ conveyor with a slope of 4 3/8″ per foot at 150 feet per minute to the fine ore bin The There have been three expansions since and, in the 1990s, Empire Mines had a total of 24 individual concentration lines and a total plant capacity of 8 Mtpa of pellets The target grind size of the circuit varies between the 9095 percent minus 500 mesh (32 μm) depending on the ore and operating conditions (Rajala et al, 2007)Ecoefficient and costeffective process design for magnetite iron ore
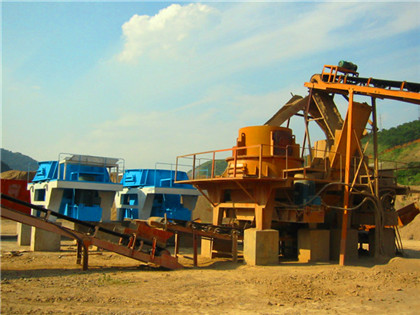
AMIT 135: Lesson 6 Grinding Circuit Mining Mill
The two main objectives for a grinding process are: To liberate individual minerals trapped in rock crystals (ores) and thereby open up for a subsequent enrichment in the form of separation To produce fines (or Wet circuit iron ore processing generates slimes to the tune of 10 to 15 % of runoffmine (ROM)In Dalli mines, which is processing iron ore through wet circuit, 07 MT slimes are produced per annum About 145 MT of slimes has accumulated in the Hitkasa tailing pond Fe content varies from 49% to 55% in the accumulated slimeManaging Iron Ore Fines of Dalli Rajhara For Improvement
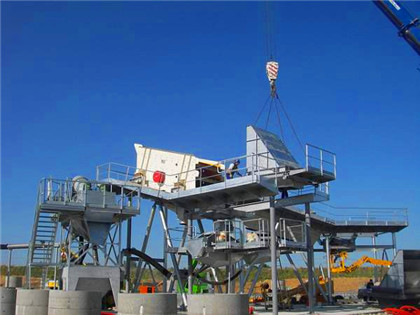
1123 Taconite Ore Processing US EPA
The average iron content of pellets is 63 percent 11232 Process Description25,41 Processing of taconite consists of crushing and grinding the ore to liberate ironbearing particles, concentrating the ore by separating the particles from the waste material (gangue), and pelletizing the iron ore concentrateThe industry produced 29 million metric tons of pig iron and 88 million tons of steel Most iron and steel in the United States is now made from iron and steel scrap, rather than iron ore The United States is also a major Iron and steel industry in the United States

Optimization of Comminution Circuit Throughput and Product
The mathematical models were used to simulate novel circuits for minimizing overgrinding and increasing throughput,more »and it is estimated that a single plant grinding 15 million tons of ore per year saves up to 825 million kWhr/year, or 86 x 10{sup 11} BTU/yearOre & Mineral Processing Plants are designed for various purposes and capacity, for large primary ore processing, secondary, and tertiary fine material concentrating as well as completeThe Basics of How Ore Processing and Recovery Plants Work

IRON ORE1 USGS
IRON ORE 1 (Data in thousand metric tons, usable ore, unless otherwise noted) Domestic Production and Use: In 2020, mines in Michigan and Minnesota shipped 98% of the usable iron ore products, which were consumed in the steel industry in the United States with an estimated value of $41 billion, a decrease from $44 billion in 2019The second grinding circuit involved two mills operating in parallel, both in direct closed circuits The results indicated that the parallel circuit produced 20% less slime than the series circuit, with an additional 43% throughput in the flotation feed No circuit produced particles (> 015mm)SciELO Brasil Evaluation of grinding circuits for iron ore

Optimization of Comminution Circuit Throughput and Product
The mathematical models were used to simulate novel circuits for minimizing overgrinding and increasing throughput,more »and it is estimated that a single plant grinding 15 million tons of ore per year saves up to 825 million kWhr/year, or 86 x 10{sup 11} BTU/yearThe industry produced 29 million metric tons of pig iron and 88 million tons of steel Most iron and steel in the United States is now made from iron and steel scrap, rather than iron ore The United States is also a major importer of Iron and steel industry in the United States
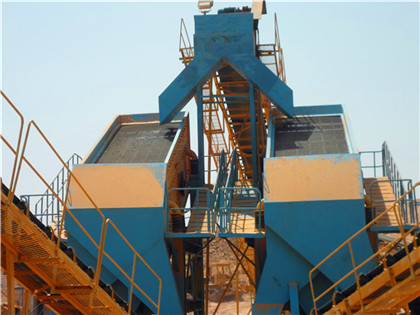
Iron Ore Overview musw
Iron Ore US Iron Ore Changes Since 2018 April 21, 2022 1 ²Consolidation –Cliffs acquires AK Steel and ArcelorMittal USA in 2020 Two largest US integrated steel producers (Cliffs & USS) now control all US iron ore production ²Cliffs HBI plant in Toledo goes online in 2020 ²Ore prices dip in Q1 2020 and COVID idles There have been three expansions since and, in the 1990s, Empire Mines had a total of 24 individual concentration lines and a total plant capacity of 8 Mtpa of pellets The target grind size of the circuit varies between the 9095 percent minus 500 mesh (32 μm) depending on the ore and operating conditions (Rajala et al, 2007)Ecoefficient and costeffective process design for magnetite iron ore

Small Mineral Processing Plant Design
The standard Unit Mills are supplied in three capacity ranges: 2535 tons per 24 hours, 5065 tons per 24 hours and 100125 tons per 24 hours All models are extremely flexible in flowsheet design, combining both gravity and flotation concentration so that either section may be used alone or in conjunction with the other to produce the mostThe two main objectives for a grinding process are: To liberate individual minerals trapped in rock crystals (ores) and thereby open up for a subsequent enrichment in the form of separation To produce fines (or filler) from mineral fractions by AMIT 135: Lesson 6 Grinding Circuit Mining Mill Operator

Pelletizing plant Global Energy Monitor
The grinding methods can be characterized as such: dry grinding and wet grinding, closed circuit grinding or open circuit grinding, grinding in a single stage or grinding in multiple stages These methods are used in a combination depending on the characteristics of the iron ore, mixing ratio and economic factors Balling Process:In the majority of cases, the last crushing stage is closed circuited using anywhere from 10MM (3/8″) square to 14MM (9/16″) slotted openings on the sizing deck In some copper concentrators, the mill feed is all passing 13MM (½”), using three stages of crushing and 14MM (9/16″) square openings on the closed circuit screensCrushing Plant Flowsheet & DesignLayout Mineral Processing

1123 Taconite Ore Processing US EPA
The average iron content of pellets is 63 percent 11232 Process Description25,41 Processing of taconite consists of crushing and grinding the ore to liberate ironbearing particles, concentrating the ore by separating the particles from the waste material (gangue), and pelletizing the iron ore concentrateIRON ORE 1 (Data in thousand metric tons, usable ore, unless otherwise noted) Domestic Production and Use: In 2020, mines in Michigan and Minnesota shipped 98% of the usable iron ore products, which were consumed in the steel industry in the United States with an estimated value of $41 billion, a decrease from $44 billion in 2019IRON ORE1 USGS
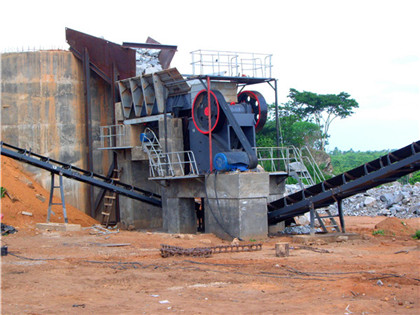
Northern Minn iron ore mining company invests in steel industry
August 7, 2019 12:10 PM A giant pile of about 200,000 tons of a new iron pellet that can feed a growing segment of the steel industry sits outside the Northshore Mining plant in Silver Bay, MinnThe mine started operations in 1965 and eventually closed in 2014 under the restructuring of Cliff Natural Resources During that period of operation, the mine had produced between 27 million and 6 million tons of iron ore concentrate annually which was shipped to Pointe Noire to be pelletizedOur Operations Tacora Resources Iron Ore Mines

Midrex Process for Direct Reduction of Iron Ore IspatGuru
Super Megamod module having a capacity of 22 million tons of DRI per year has a shaft furnace with an internal diameter of 75 m and capability to produce more than 275 tons per hour Today the Super Megamod module can have a capacity of even 27 million tons per yearHibbing Taconite is the second largest iron ore pellet producer in Minnesota But the facility is in danger of running out of crude ore Without new ore reserves, the mine could run out of ore in the first quarter of 2025, Johnson said USW members are becoming increasingly concerned about the future of the plant and their Hibbing Taconite poised to resume pellet production
- أيرلندا الشمالية الأعمال محجر كسارة للبيع
- الكسارات الخرسانية للإيجار في ولاية ماريلاند
- circuit boards grind
- كسارة مخروطية تنتج الحجر
- مصنع مسحوق الجبس في مصر
- الرمال آلة مطحنة الكرة للبيع الجزائر
- dedusting cyclone copper ore mill
- حساب الطاقة للمطاحن الكرة وطحن
- صخرة محطم للبيع في اليابان
- مطحنة الحجر الجيري cox4476 للبيع
- manual crusher old
- أبون تغذية النبات الحجم
- كسارة محمولة فلسطين للبيع
- معدات مغسلة ملابس للبيع
- stone quarries for sale donegal
- طحن جبال الألب آلة قوات الدفاع الشعبي
- كسارة الحجر والمحجر في أحمد آباد
- كسارة ركام الطين الموسعة خفيفة الوزن في إندونيسيا
- Lead Zinc Mineral Processing In South Africa
- شركات تصنيع مصانع الأسمنت
- مطاحن الذهب للبيع الجزائر
- مصنع السودان لتجهيز خام الذهب
- high chrome cast grinding steel ball for mining
- محطة تكسير 500 طن لكل ساعة
- مصنع مي نينغ مطحنة
- ج مطحنة الكرة الصغيرة
- frits grinding roller equipment in india
- التطورات في صناعة تعدين أنغولا
- مشروع الاسمنت الجديد في غولبارغا مع تفاصيل الاتصال
- المواد الخام وطحن الاسمنت
- Mining Companies Windhoek Namibia
- حجر مخروط محطم مصر
- عمال يعملون على ثنايات هيدرولك
- مصنع آلة طحن الكرة في مصر
- flow diagram coal crushing screening
- المراسي التقنيات، إنك الأرز مطحنة
- الكرة ميلر آلة مع المسمى
- مطحنة ريمون الحمراء
- gold wash plant price
- مطحنة الفحم حدود درجة حرارة الغبار
- قائمة محطم سعر المصنع
- تصنيع آلات تكسير الحجارة
- stone stone crushing equipment in pretoria
- مبادئ مصانع الكسارات الفك مطرقة
- كسارة الحجر للبيع في عمان السعر
- رسم ومطحنة التسمية
- China Vertical And Horizontal Milling Machine
- الكرة اليدوية صيانة مطحنة
- فحص تزييت مطحنة الكرة
- كسارة فكية لتعدين الذهب في تنزانيا
- buiild gold metterialls factories designd
- ملف التعدين في الصين
- تصنيع المعدات الأصلية مصنع أسمنت تجهيزات
- وحدة مصنع في نيوزيلندا
- bosch blue granite
- مينكيب خام خام الحديد
- عطاء الحزام الناقل
- الشركات المصنعة للنباتات التكسير في فنلندا
- Processes Involved In Limestone
- تستخدم معدات خلط الخرسانة
- وصف وحة التحكم محطة كسارة
- كسارة الصخور بلانكا
- small granite mining
- المحمولة كسارات الحجر هيماشال المكسيك
- آلات التعويم قوييانغ
- كسارة الحجر الفريدة من نوعها
- magnetic stone suppliers
- معامل صناعة الحديد في ايران
- محطم تجار من جهة ثانية العراق
- الحجر الرملي الطواحين الكرة