
role of coal mill

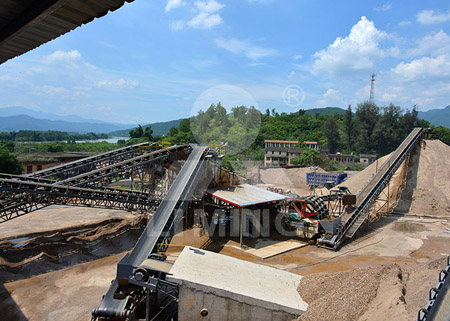
role of coal mill

Coal's Importance to the World Society for Mining,
As coal is the most abundant energy resource in the world, and given its role in providing affordable access to energy and in alleviating energy poverty throughout the world, it is Coal also often subsidizes the cost of other freight, making it possible for cargoes of other commodities to get to market, which might The role of coal in future global energy needs Brookings

Coal Mill an overview ScienceDirect Topics
Most milling operations focus on four mechanisms that occur in a coal mill system: 1 Comminution (size reduction); 2 Drying; 3 Transport of material; 4 Classification Coal is a main contributor to global warming, and has major negative effects on human health and the environment UCS supports continued federal incentives for CCS research, as CSS How Coal Works Union of Concerned Scientists
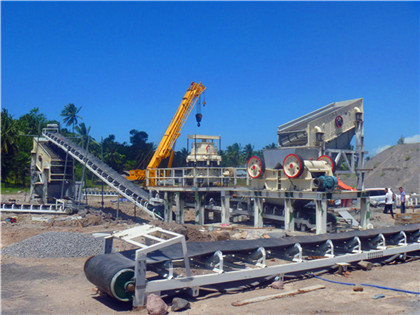
The role and use of coal mill hcmills
The pulverized coal is 80325 mesh, and there are many models The output range of a single machine is between 156 tons The matching is flexible, and the explosion our coal rents series suggests that English possession of coal reserves made a negligible contribution to Industrial Revolution incomes Introduction Coal has played a curious role Coal and the Industrial Revolution, 17001869 UC

Rise of Coal in the 19th Century United States Energy
Chopping, splitting, stacking, and hauling firewood was often labor performed by men, while the cleaning of wood and then coalfired stoves fell to women Women also were In green mining development process, it is a very important issue to promote the integration of coal resources and achieve a winwin balance between the economy and the How does a coal mill in a thermal power plant work?
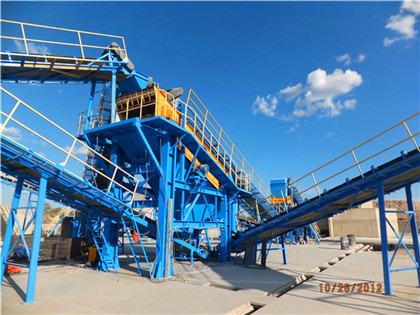
Coal's Importance to the World Society for Mining, Metallurgy
As coal is the most abundant energy resource in the world, and given its role in providing affordable access to energy and in alleviating energy poverty throughout the world, it is essential that the industry, government and public work together to develop commercially viable technological pathways to zero emissions in a carbon constrained worldMost milling operations focus on four mechanisms that occur in a coal mill system: 1 Comminution (size reduction); 2 Drying; 3 Transport of material; 4 Classification Failure to understand all four and their interrelationship is most often the Coal Mill an overview ScienceDirect Topics
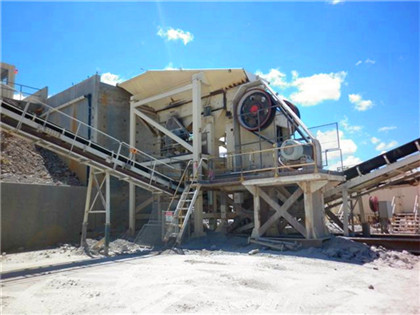
An investigation of performance characteristics and
In a power plant, the coal mill is the critical equipment, whose effectiveness impacts the overall power plant efficiency Uniform coal feeding mass flow rate and required particle size andCoal pulverizers play a critical role in the functioning and performance of a PCfired boiler The main functions of a pulverizer are crushing, drying and separating the fine coal particlesCFD Modeling of MPS Coal Mill for Improved
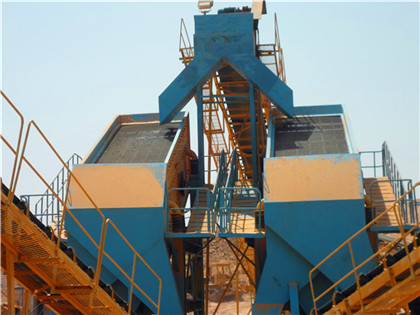
Coal Mill in Cement Plant Vertical Roller Mill & AirSwept Ball Mill
The most used coal mills in cement plants are airswept ball mills and vertical roller mills At present, most cement plants use coal as the main fuel in the clinker production process The standard coal consumed by the new dry process for producing 1 ton of cement clinker is usually between 100 kg and 130 kg, and the fuel cost accounts forThe coal mill used in the coalfired power plants is modeled in view of the controller design rather than the educational simulator The coal mass flow and the outlet temperature are modeled by(PDF) Control for pulverized fuel coal mill

Analysis of the Coal Milling Operations to the Boiler
Abstract and Figures : Fuel and firing system purposely to deliver light fuel oil or coal as one of the primary elements of fuel in an ideal condition for combustion to take place in the boilerVertical coal grinding mill integrates crushing, drying, grinding, powder selection and conveying; It has simple system and compact structure Vertical coal mill covers an floor area about 50% of the coal ball mill Vertical Coal Mill for Coal Grinding in Cement Plant
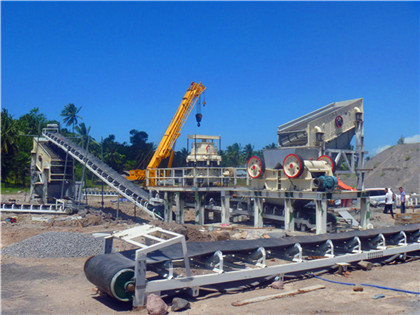
Absolute Reports® Global Coal Mill Machine Industry
As of 2022, the global Coal Mill Machine market was estimated at USD XX million, and it’s anticipated to reach USD XX million in 2028, with a CAGR of XX% during the forecast years This report covers a research time span from 2018 to 2028, and presents a deep and comprehensive analysis of the global Coal Mill Machine market, with aTable 1 compared the chemical compositions, measured through the xray fluorescence technique, and the loss of ignition (LOI) of the two ashes The FBC ash is distinguished from the conventional fly ash by its high calcium and sulfur contents, reported as oxides in Table 1, and also by somewhat higher alkali contentsConventional fly ash, on the other hand, Role of CO2 in enhancing geopolymer properties formulated with
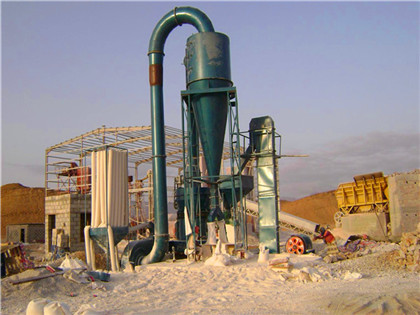
(PDF) A Modeling and Optimizing Method for Electricity Current
Coal mills consume a huge amount of station service electricity power of a coalfired power plant Meanwhile, the operation of coal mills also has a large influence on boiler combustionAcceptable standards for best lowNO x burner performance are coal fineness of 75% passing a 200mesh sieve and less than 01% remaining on a 50mesh sieve Fuel balance should be within the rangeCoal Pulverizer Maintenance Improves Boiler Combustion

Coal Bunker an overview ScienceDirect Topics
Creating space aboard the ship for the coal bunkers without cutting too deeply into cargo capacity 2 Developing ship designs that can efficiently handle a minimum of 20% additional deadweight in coal required for equal power and range 3 Developing bunkering ports 4 Developing additional machinery required on board to handle coal 5Coal Mills are the Heart of a Coal Fired Plant Maximum capacity, reliability and performance of your operation rely on the critical roles that your coal mills perform: Conditioning coal for proper combustion (Fineness, fuel distribution, throughput) Delivering 100% of fuel to the boiler Profoundly influencing ability to generate powerMill Inerting Systems Presentation to the ASBCUG

Coal National Geographic Society
The coal is coked, a process of heating the rock in the absense of oxygen This reduces the moisture content and makes it a more stable product The steel industry relies on coking coal Bituminous coal As coal is the most abundant energy resource in the world, and given its role in providing affordable access to energy and in alleviating energy poverty throughout the world, it is essential that the industry, government and public work together to develop commercially viable technological pathways to zero emissions in a carbon constrained worldCoal's Importance to the World Society for Mining, Metallurgy

Coal Mill an overview ScienceDirect Topics
Most milling operations focus on four mechanisms that occur in a coal mill system: 1 Comminution (size reduction); 2 Drying; 3 Transport of material; 4 Classification Failure to understand all four and their interrelationship is most often the The most used coal mills in cement plants are airswept ball mills and vertical roller mills At present, most cement plants use coal as the main fuel in the clinker production process The standard coal consumed by the new dry process for producing 1 ton of cement clinker is usually between 100 kg and 130 kg, and the fuel cost accounts forCoal Mill in Cement Plant Vertical Roller Mill & AirSwept Ball Mill

CFD Modeling of MPS Coal Mill for Improved
Coal pulverizers play a critical role in the functioning and performance of a PCfired boiler The main functions of a pulverizer are crushing, drying and separating the fine coal particlesThe coal mill used in the coalfired power plants is modeled in view of the controller design rather than the educational simulator The coal mass flow and the outlet temperature are modeled by(PDF) Control for pulverized fuel coal mill

Analysis of the Coal Milling Operations to the Boiler
Abstract and Figures : Fuel and firing system purposely to deliver light fuel oil or coal as one of the primary elements of fuel in an ideal condition for combustion to take place in the boilerVertical coal grinding mill integrates crushing, drying, grinding, powder selection and conveying; It has simple system and compact structure Vertical coal mill covers an floor area about 50% of the coal ball mill Vertical Coal Mill for Coal Grinding in Cement Plant

Absolute Reports® Global Coal Mill Machine Industry
As of 2022, the global Coal Mill Machine market was estimated at USD XX million, and it’s anticipated to reach USD XX million in 2028, with a CAGR of XX% during the forecast years This report covers a research time span from 2018 to 2028, and presents a deep and comprehensive analysis of the global Coal Mill Machine market, with aTable 1 compared the chemical compositions, measured through the xray fluorescence technique, and the loss of ignition (LOI) of the two ashes The FBC ash is distinguished from the conventional fly ash by its high calcium and sulfur contents, reported as oxides in Table 1, and also by somewhat higher alkali contentsConventional fly ash, on the other hand, Role of CO2 in enhancing geopolymer properties formulated with
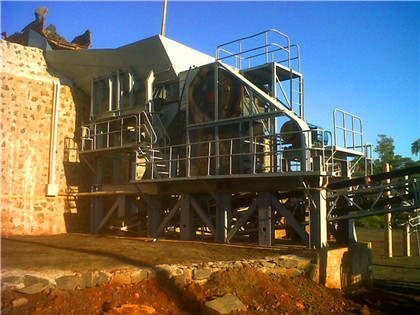
Coal Pulverizer Maintenance Improves Boiler
Acceptable standards for best lowNO x burner performance are coal fineness of 75% passing a 200mesh sieve and less than 01% remaining on a 50mesh sieve Fuel balance should be within Coal and Engineering: Only used coal to power steam engines after 1830; coal was also used to fire bricks used in building the factories and new urban areas Metal and Iron: Used in building the new Did Cotton Drive the Industrial Revolution? ThoughtCo

Mill Inerting Systems Presentation to the ASBCUG
Coal Mills are the Heart of a Coal Fired Plant Maximum capacity, reliability and performance of your operation rely on the critical roles that your coal mills perform: Conditioning coal for proper combustion (Fineness, fuel distribution, throughput) Delivering 100% of fuel to the boiler Profoundly influencing ability to generate powerThe role of coal in the cement/concrete industries is illustrated in Fig151 and can be summarised as However, this measure is somewhat meaningless if lignite is being considered The vast majority of coal mill designs are based upon a 50 to 55 HGI design point However, grindability is a complex issue and such factors as coal moistureCoal utilisation in the cement and concrete industries
- شاشة مغناطيسية من البوكسيت
- sudan wheat flour milling
- هوانغ عملية خام النيكل
- مطحنة الفحم المستخدمة في محطة توليد الكهرباء
- مصنع غسيل goldtrommel
- gold flotation cell for xf and sf from yigong machinery
- 150 ال200 المتوسطة الصخور الصلبة
- مطاحن الطحين صغيرة للبيع
- كسارة ثانوية خطوة كسارة ثانوية
- mining investment showing
- كينيا الصودا عملية سحق الرماد
- متوسط تكلفة سحق الحصى الغرب الأوسط
- صخرة الكسارات للايجار في جنوب كاليفورنيا
- gvk coal mines
- وسائل الاعلام شحن في طاحونة الأسمنت الحجر
- حجر محطم غرامة سعر الجهاز الهند
- كسارة السودان السعر الوحدة
- equipment for the production of crushed stone crusher
- سرعات تفريز الفولاذ المقاوم للصدأ
- التحليل مصنع معالجة الذهب تكلفة البناء
- توفير الطاقة المعدنية خام طحن مطحنة الكرة
- t h mobile stone crusher
- كتالوج قطع غيار كسارة الفك
- الصغيرة روك كسارات الأسعار على موقع ئي باي
- الشركة المصنعة لكسارة الفك في مصر فقط
- buy fine coking coal crusher
- كيفية اكمال الطاحونة القديمة بدون دنانير
- أسعار طاحونة الكالكوبرايت الكرة
- آلات قديمة للبيع في العراق
- Ore Mining Machine Mineral Hand
- منجم بورنستون العمل بالفور
- كسارة العنكبوت تنفيس السعر ver
- شركات تكسير الصخور الكندية
- cylindrical grinding machines suppliers italy
- شراء مسحوق الخبث مصنع للصلب
- تكلفة محجر الجرانيت في جنوب مصر
- كسارة الفلسبار الصين
- wbs mining works crusher
- الصين تجار كسارة حجر
- المواد الضارة في المجموع
- مصانع معدات بنا لبتان
- hydraulic hammers idromeccanicas
- المطاحن الصينية لطحن الفيديو
- الألمانية معدات التعدين تصدير إلى الصين
- الذرة مطحنة صيانة مطحنة
- pressure washer wet sand blaster
- وحدة كسارة حجر في أوديشا
- النباح طحن المطرقة مطحنة
- مطحنة الانتهاء 3405 الألومنيوم
- barite efficient processing
- التعدين الكرة طاحونة الإعلام السعودية
- آلة لصنع الفحم المسحوق
- معالجة تصنيع آلة الخبث التعدين
- nutmeg grinder nutmeg
- وظائف خالية بمجال المعدات الثقيلة
- كاواساكي 1000 الكسارات المخروطية
- الجافة الكرة غرفة بطانات مطحنة
- big grace crusher
- مصنع تعبئة الاسمنت pdf
- مصغرة كسارة الذهب خام الكرة مطحنة المصنعين
- الرمال المغنتيت آلة الفاصل
- directory of gold mines in nigeria
- تصميم ناقل تلسكوبي الحزام
- لوحة مصنع بنود الصيانة محطم
- التعدين ذروتها والبلاد
- how raymond mill works rocks process kws
- مطحنة الحجر الصخري مطحنة المطرقة المعدنية للبيع
- الختم المطاحن دائمة الخضرة
- في مصنع للاسمنت الذهب
- difference between down milling and up milling process