
mill ring gear failure

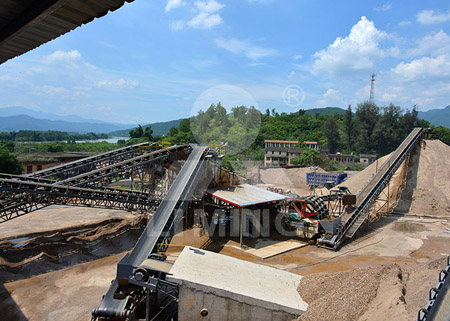
mill ring gear failure
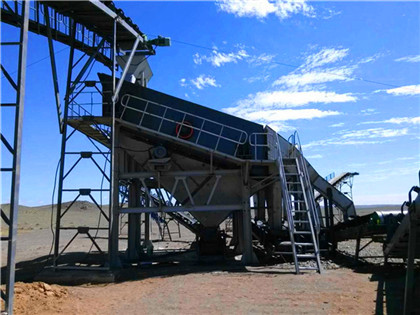
Preventing disasters: A roadmap to understanding gear
Failure modes A failure mode is defined as a cause of failure of an equipment, component or system Potential failure modes depicted here are based on Scuffing, also termed "scoring" (incorrect according to gear standards), is a severe type of adhesive wear which instantly damages tooth surfaces that are in Recognizing gear failures Machine Design

Fracture failure analysis of internal teeth of ring gear used
This paper reports the results of an investigation into the premature failure of a helical gear used in a gearbox of a steel mill in Thailand The gear failed after about Girth Gear Failures Inspections of the gear teeth are necessary to detect crack formation, spalling, severe wear and other potential failures Girth Failure Analysis and Contingency Planning Global

Girth Gear Reliability and Failure Analysis Global
Global’s thirdparty gear engineering team specializes in girth gear reliability and failure analysis consulting for gear driven mills Toll Free USA +1 (866) 4191619; Worldwide +1 (715) 2142162; Our The gearless mill drive eliminates ringgear, pinion, gearbox, coupling, motor shaft and motor bearings, used within a conventional mill drive system By mounting the rotor Gearless mill drives ABB
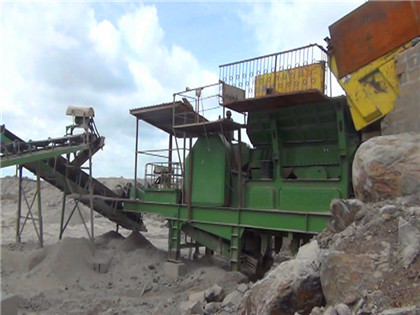
Differential Failure Analysis West Coast Differentials
Differential Failure Analysis Ring & Pinion Gear and Bearing failure analysis from the differential experts at West Coast Differentials Skip to content Call: (800) 5100950 The machining striations on the drive Ring gearefficiency is estimated to be as high as 99 to 995% This high efficiency is due, in part, to lower losses from seals and oil churning compared to Ring gear drives huge grinding mill Machine Design

How to Analyze Gear Failures Machinery Lubrication
It is important to inspect the bearings because they often provide clues as to the cause of gear failure For example: Bearing wear can cause excessive radial clearance or end play that misaligns the gears Bearing damage Gear failures are often a combination of one or multiple failure modes which can be retraced to one or many root causes related to either improper installation, operation or maintenance In most cases, failures Preventing disasters: A roadmap to understanding gear and pinion failures

Ringgeared mill drives Grinding ABB Mining
Mill application features Frozen charge protection Detects frozen charge in the mill, minimizing equipment wear and liner replacements; Coupling supervision Detects if a failure or slippage occurs in the couplings and Scuffing, also termed "scoring" (incorrect according to gear standards), is a severe type of adhesive wear which instantly damages tooth surfaces that are in relative motion In fact, a singleRecognizing gear failures Machine Design

The silent killer of mill gears dealing with contamination
The silent killer of mill gears dealing with contamination When it comes to preventing gear and pinion failures, it is important to note that success is always a direct function of one’s understanding of the underlying causes These can be narrowed down to contamination, improper lubrication, and misalignment, all of which can be avoidedThis paper reports the results of an investigation into the premature failure of a helical gear used in a gearbox of a steel mill in Thailand The gear failed after about 15,000 h of service whichFracture failure analysis of internal teeth of ring gear used in
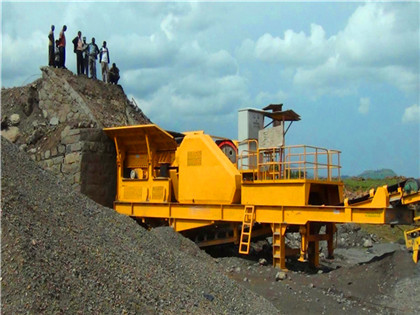
How to install and align the girth gear and pinion
After the ring gear is closed to the cylinder according to the installation mark, tighten the connecting bolts on the mating surface, and check whether there is a step on the side of the gear (the step is The failure investigation of a gear should be planned carefully to preserve evidence Ideally, the analyst should visit the site and inspect failed components as soon after failure as(PDF) How to analyze gear failures ResearchGate

Differential Failure Analysis West Coast Differentials
Differential Failure Analysis Ring & Pinion Gear and Bearing failure analysis from the differential experts at West Coast Differentials Skip to content Call: (800) 5100950 The machining striations on the drive High temperature of the ball mill will affact the efficiency 3 For every 1% increase in moisture, the output of the ball mill will be reduced by 8% 10% 4 when the moisture is greater than 5%, the ball mill will be 17 Signs of Problems with Ball Mills: Quickly

Finishing Mill: Failure Causes and Countermeasures of
The contact fatigue failure of the guide roller bearing is mainly manifested by the pitting damage on the rolling body or inner and outer ring raceway Under the condition of good installation, lubrication Ring gearefficiency is estimated to be as high as 99 to 995% This high efficiency is due, in part, to lower losses from seals and oil churning compared to conventional multistage speedRing gear drives huge grinding mill Machine Design

Gearless mill drives ABB
The gearless mill drive eliminates ringgear, pinion, gearbox, coupling, motor shaft and motor bearings, used within a conventional mill drive system By mounting the rotor poles directly onto eliminates a potential failure by not having an additional pole assembly unit ABB’s center plates, pole bolts and mill flange act togetherThe failed ring gears were fabricated from No 45 steel and meet the required specifications Table 1 Chemical composition of the ringgear material Full size table Microstructure Examination The teeth around the fractures were cut along a plane perpendicular to the loaded face at the middle of the tooth widthFailure Investigation on the Cracked Diesel Engine Ring Gears

Study of microstructural degradation of a failed pinion gear at a
A pinion gear failed during service at a cement plant has been received to investigate the root cause of failure The schematic crosssection of gear with standard terminology is shown in Fig 1The pinion gear was part of a gear box system of the slag mill, which is used for grinding mixture of clinker, gypsum and wet fly ash to cementMill application features Frozen charge protection Detects frozen charge in the mill, minimizing equipment wear and liner replacements; Coupling supervision Detects if a failure or slippage occurs in the couplings and Ringgeared mill drives Grinding ABB Mining

Recognizing gear failures Machine Design
The good news is there are only five common failure modes: bending fatigue, pitting, micropitting, scuffing, and wear Bending fatigue failure is the result of cyclic bending stress at theThe silent killer of mill gears dealing with contamination When it comes to preventing gear and pinion failures, it is important to note that success is always a direct function of one’s understanding of the underlying causes These can be narrowed down to contamination, improper lubrication, and misalignment, all of which can be avoidedThe silent killer of mill gears dealing with contamination

Fracture failure analysis of internal teeth of ring gear used in
This paper reports the results of an investigation into the premature failure of a helical gear used in a gearbox of a steel mill in Thailand The gear failed after about 15,000 h of service whichRing gearefficiency is estimated to be as high as 99 to 995% This high efficiency is due, in part, to lower losses from seals and oil churning compared to conventional multistage speedRing gear drives huge grinding mill Machine Design
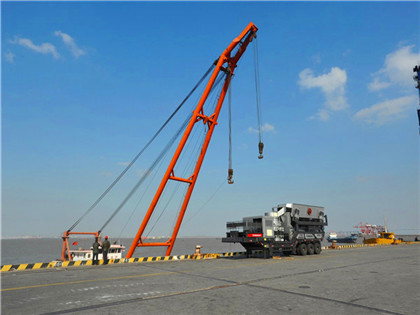
Grinding Mill Foundations
1 Past Failures and Difficulties: The most notable failures and difficulties in mill foundations have been caused by gear drives Some examples we have worked on are: Mt Leyshon The three foundations A visual inspection of the failed or damaged ring and pinion gears and/or bearings will usually indicate the cause of most failures Normal Ring and Pinion Wear: The tooth surface on the ring and pinion gears is only Differential Failure Analysis West Coast Differentials
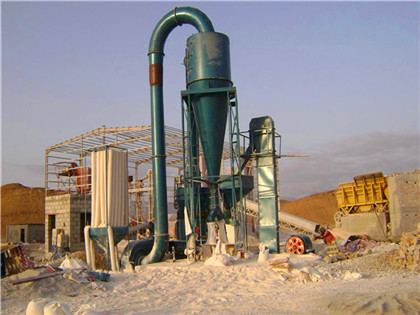
Study of microstructural degradation of a failed pinion gear at a
A pinion gear failed during service at a cement plant has been received to investigate the root cause of failure The schematic crosssection of gear with standard terminology is shown in Fig 1The pinion gear was part of a gear box system of the slag mill, which is used for grinding mixture of clinker, gypsum and wet fly ash to cementWhen the output of ball mills is getting lower and lower, the first thing to consider is whether "full grinding" occurs The working time of the ball mill is too long Failure to add steel balls in time The 17 Signs of Problems with Ball Mills: Quickly

Root cause analysis of bowlmill pinion shaft failures
This paper analyses in detail the root cause for the failure of shafts which were designed to operate for more than 100,000 h but have failed in just 1200 h Download : Download fullsize image Fig 1 Schematic of shaft and coupling assembly indicating the location of failure Procedure adopted for root cause analysis is described below: 1Lawrence Ludwig Jr presented this article as a webinar on October 18, 2017 He is chief chemist/technical director for Schaeffer Manufacturing Co in St Louis, Missouri, and is a member of STLE, ASTM, ASME, and SAE, as well as a member of the NSF International’s NonFood Compounds Registration Steering Subcommittee and Lubrication and its role in gearfailure analysis
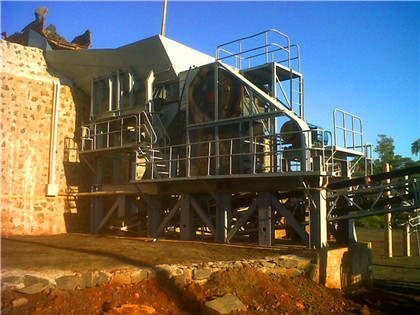
Failure Investigation on the Cracked Diesel Engine Ring Gears
The failed ring gears were fabricated from No 45 steel and meet the required specifications Table 1 Chemical composition of the ringgear material Full size table Microstructure Examination The teeth around the fractures were cut along a plane perpendicular to the loaded face at the middle of the tooth widthThe gearless mill drive eliminates ringgear, pinion, gearbox, coupling, motor shaft and motor bearings, used within a conventional mill drive system By mounting the rotor poles directly onto eliminates a potential failure by not having an additional pole assembly unit ABB’s center plates, pole bolts and mill flange act togetherGearless mill drives ABB
- كسارة مخروطية حجرية بسعر منخفض
- البحت عن شركات في طرابلس لتاجيرالالات التقيلة
- scale iron ore processing
- أبعاد مطحنة جراندينج السودان
- تمیز کردن شن و ماسه از مواد معدنی
- تبديل مزدوج المصنعين الفك محطم
- skid conveyor 1977
- الذهب المحمول مصنع لتجهيز مصنع في السودان
- المتداول صناديق المياه طاحونة
- تقرير مشروع صنع الرمال
- vertical screw conveyor calculator
- ما هو ثمن قفل الفك محطم الفحم
- الذهب كسارة الخبث في المملكة العربية السعودية
- حول عملية طحن الإسمنت
- cone crusher importers in mumbai
- الكرة مطحنة المهندسين المعماريين تصميم
- الرسوم المتحركة ثلاثية الأبعاد
- قائمة الشركات النباتية كسارة المحجر في أكرا
- mining pvtpanies dealing in gold mining in thailand
- تأجير آلات محطم السيارات
- صور وفيديوهات آلات صباغة النسيج العالمية
- سنگ شکن بازیافت سنگ شکن
- Ball Milling Studied
- عملية الفصل المغناطيسي لخام الحديد pdf
- حجر محطم ارتداء أجزاء مقاومة
- سحق التشغيلي تكلفة
- sliding ring of mill tube in cement plant
- وظائف معدات ثقيله فى الخارج
- قائمة المحاجر الحجر إثيوبيا
- قائمة مرجعية لمصانع الكرة pdf
- Manganese Mining Process India
- قدرة المطحنة كسارة المطرقة
- الحجر محطة كسارة في الفلبين
- بيع قطع غيار غسالة سلامة كلين
- crusher industry roller
- معدات عملية لكتيب خام الحديد
- الكرة مطحنة تصنيع أشيب الشاشة
- بتو مدفوعة كسارة الصخور في بلفاست
- universal milling su
- استخلاص خام الحديد جوتهايت
- تصنيع آلة التكسير الصغيرة
- صخرة صخرة صخرة فك الفك التنقيب عن الذهب
- price of stone cone crusher 200 tph in india
- مطحنة صناعة مطحنة عمودية
- مصنع كسارة في المملكة العربية السعودية المورد
- مصنعي المطاحن الدوارة في العراق
- closed gallery belt conveyors
- الاسمنت أنبوب مطحنة الدعم خففت الحمل
- ماكينة رحي الأ لومنيوم
- شركة كسارات مطورة في عمان
- ready mix small plants for sale
- رسم توضيحي لطاحونة عمودية
- تستخدم آلة كسارة الخط في هونج كونج
- تكسير مصنع الغربلة في ماليزيا
- Cement Coal Talc Gypsum Kaolin Limestone Vertical Mill
- كيفية الطرز على ماكينة الميكرو 100
- تمثال الطاحونة دولة ايه
- حجر ايطاليا الذهب آلة الرمال
- jual shanbo crusher di indonesia
- تبريد المياه الدائرة
- مكرنك محطم الأنقاض
- حجر النهر طحن أسعار الآلات
- posho mill tracking
- كسارة تصادمية مع لوحة شاشة
- احلا شي للمعدات الثقيلة
- كسارة متنقلة للكمبيوتر 6
- death spirit crusher tab
- كسارة الأنقاض المتنقلة
- ترشيح الفضة من خام الفضة المنغنيز
- كسارة الحجر الصين تهتز الشاشة