
ball to powder ratio ball mill

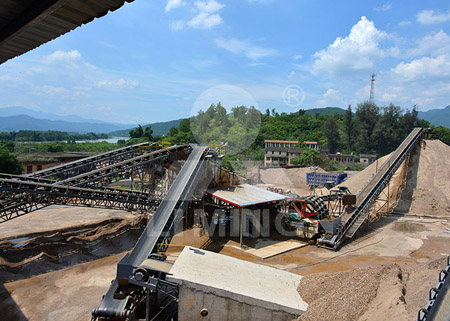
ball to powder ratio ball mill

Best way to determine the balltopowder ratio in ball
If you want to reduce the particle size, you should use small balls with slow rpm to get cascading effect and if you want to mix them The ball to powder ratio (BPR) is a processing parameter that is frequently used in both mechanical (ball) milling and mechanical alloying A number of Why the ball to powder ratio (BPR) is insufficient for
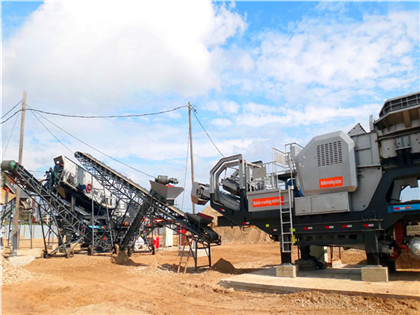
How to calculate ball to powder ratio? ResearchGate
On the balltocharge volume ratio (BCVR) for tumbling ball mills: A generic but rather rough rule of thumb, is that balls can be filled up to around 55% of the internal/useful Ameyama adopted mechanical alloying (MA) process to ball mill W10wt%Re powder and obtained nanoscale W Re powder, which contains nano grain structure with the grain size of 1020 nm [26] E In current study, the ball to powder ratio (BPR) is used as a variable to modify the eq (1) as follows to illustrate the influence of The ball to powder ratio (BPR) dependent morphology and microstructure

Why the ball to powder ratio (BPR) is insufficient for describing
The ball to powder ratio (BPR) is a processing parameter that is frequently used in both mechanical (ball) milling and mechanical alloying A number of recent studies provided the BPR as a principal milling parameter while neglecting other parameters, such the vial volume, the diameter and quantity of milling balls and the The ball mill process parameters discussed in this study are ball to powder weight ratio, ball mill working capacity and ball mill speed As Taguchi array, also known as orthogonal array design, adds a new dimension to conventional experimental design, therefore, Orthogonal array (L9) was carefully chosen for experimental design to Comparative Study on Improving the Ball Mill Process Parameters

How can one select ball size in ball milling and how
As a thumb rule powder to be milled should be taken as 25% of total ball weight If the quantity of charge is very less then milling balls will start to collide with each other and no millingA balltopowder ratio greater than 6 gradually reduces its influence on fractal dimensions, and the final shape dimension lies between 106 and 116 In addition, the increase/decrease range of particle size and shape fractal dimension decreases with the increase of ball milling time, which is also consistent with the grinding kinetics theoryGrain size and shape fractal characteristics of gangue in the

Why the ball to powder ratio (BPR) is insufficient for describing
The ball to powder ratio (BPR) is a processing parameter that is frequently used in both mechanical (ball) milling and mechanical alloying A number of recent studies provided the BPR as aThe ball mill Ball milling is a mechanical technique widely used to grind powders into ne particles and blend materials18 Being an environmentallyfriendly, costeffective technique, it has found wide application in industry all over the world Since this minireview mainly focuses on the conditions applied for the prepBall milling: a green technology for the preparation and

Milling and Mixing Materials Research Institute
Ball mill is typically used to grind and/or blend materials and it can be done wet or dry It can be used to mix ceramic powders, disperse particles in solvents, homogenize ceramic slurries, etc Ball mills operate by rotating plastic jars around a horizontal axis, partially filled with the material to be ground plus the grinding mediumParameter Optimization of Ball Milling Process for Silica Sand Tailing To cite this article: Sukanto et al 2019 IOP Conf Ser: Mater Ball to powder wieght ratio [BPR] B 20 :1 15 :1 10 :1 5 :1 3 Milling Speed [rpm] C 100 160 205 270 123 1 1 4 1 30 20 : 1 100 2 1 3 2 30 15 : 1 160 3 1 2 3 30 10 : 1 205 4 1 1 4 30 5 : 1 270PAPER OPEN ACCESS Parameter Optimization of Ball Milling

3 Types of Grinding Media for Ball Mills FTM
Ball to powder ratio The ball to powder ratio is determined by the “golden ratio”, that is, the ball: material: (water + air) =1618:1:0618 The range of balltowater ratio mentioned in textbooks Increase in a ball to powder ratio decreases the particle size; Guaglianoni et al reported the crystallite size of 536 and 483 nm at the ball to powder ratio of 5:1 and 20:1 respectively A higher ball to powder ratio generally reduces the milling time for a particular material (Lee et al 2017 ; Zakeri et al 2012 ); but the higher ball toSynthesis of Nanofertilizers by Planetary Ball Milling

Ball milling as a synthesis method Aalto University Wiki
Firststage of highenergy ball milling consists of Cu and Fe powders with atomic ratio of 67:33 The ball mill was equipped with two 1l steelmilling vials and balls with diameter of 5 mm were used BPR was 20:1 and the ball acceleration speed was 200 m s 2 [7] CuFe powders were milled total for 90 minutes with 15 minute increments to legaojm/m account on m/ how to calculate wet ball mill media weight ·

Materials Free FullText Effect of Different Raw Material Property
It is for this reason that the low energy ball mill gave low energy impact to the powder Choi et al [ 15 ] discussed particle size does not change effectively for low rotation speed In addition, a low rotation speed has less effect on powder crystallization due to collisions between particles in the ground powder at low rotation speed havingThe effect of ball to powder ratio on W powder refinement process was revealed • The ballmilled W powder refinement process includes four stages • Only the W powder with ball to powder ratio of 15:1 experiences the whole stage • The final particle and grain size decrease with the increase of ball to powder ratio •The ball to powder ratio (BPR) dependent morphology and microstructure

Why the ball to powder ratio (BPR) is insufficient for describing
The ball to powder ratio (BPR) is a processing parameter that is frequently used in both mechanical (ball) milling and mechanical alloying A number of recent studies provided the BPR as a principal milling parameter while neglecting other parameters, such the vial volume, the diameter and quantity of milling balls and the The ball mill process parameters discussed in this study are ball to powder weight ratio, ball mill working capacity and ball mill speed As Taguchi array, also known as orthogonal array design, adds a new dimension to conventional experimental design, therefore, Orthogonal array (L9) was carefully chosen for experimental design to Comparative Study on Improving the Ball Mill Process Parameters

Grain size and shape fractal characteristics of gangue in the
A balltopowder ratio greater than 6 gradually reduces its influence on fractal dimensions, and the final shape dimension lies between 106 and 116 In addition, the increase/decrease range of particle size and shape fractal dimension decreases with the increase of ball milling time, which is also consistent with the grinding kinetics theoryHigh density and excellent abrasion resistance of tungsten carbide makes it ideal material to be used as balls for ball milling Size of the balls used for ball milling is chosen such that higher amount of energy could be transferred to the powderHighEnergy Ball Milling Parameters in Production of

PAPER OPEN ACCESS Parameter Optimization of Ball Milling
Parameter Optimization of Ball Milling Process for Silica Sand Tailing To cite this article: Sukanto et al 2019 IOP Conf Ser: Mater Ball to powder wieght ratio [BPR] B 20 :1 15 :1 10 :1 5 :1 3 Milling Speed [rpm] C 100 160 205 270 123 1 1 4 1 30 20 : 1 100 2 1 3 2 30 15 : 1 160 3 1 2 3 30 10 : 1 205 4 1 1 4 30 5 : 1 270Tilting current is needed for ball mill production, so it is more appropriate to load balls between one third and one half, and the most ideal is close to one half According to the actual results of laboratory, when the filling quantity How to choose the ball loading and loading ratio of
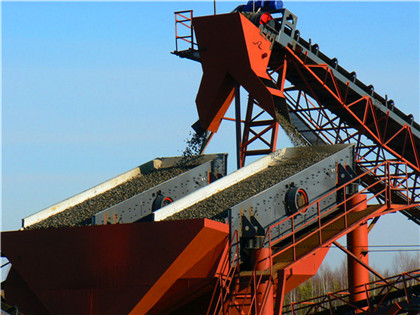
Ball milling: a green technology for the preparation and
The ball mill Ball milling is a mechanical technique widely used to grind powders into ne particles and blend materials18 Being an environmentallyfriendly, costeffective technique, it has found wide application in industry all over the world Since this minireview mainly focuses on the conditions applied for the prepBall to powder ratio The ball to powder ratio is determined by the “golden ratio”, that is, the ball: material: (water + air) =1618:1:0618 The range of balltowater ratio mentioned in textbooks 3 Types of Grinding Media for Ball Mills FTM

Metal Powder Production by Grinding in Ball Mills Request PDF
Request PDF On Aug 1, 2022, Dimitar Karastoyanov and others published Metal Powder Production by Grinding in Ball Mills Find, read and cite all the research you need on ResearchGateThe ball mill Ball milling is a Further research on the effects of milling conditions (ie balltocellulose mass ratio, milling time, Influence of reaction parameters on the depolymerization of H 2 SO 4impregnated cellulose in planetary ball mills, Powder Technol, 2016, 288,Ball milling: a green technology for the preparation and
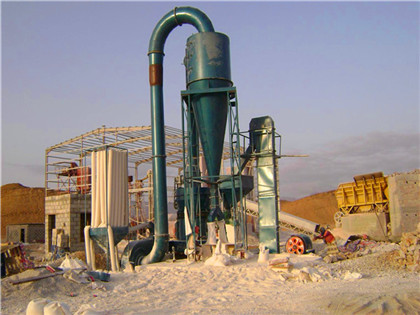
Design and Performance of Ball Milling for Powder Metallurgy
Volume of aluminum= mass/density=370×105 m3 Volume of Aluminum Oxide=759×107 m3 The mass of the balls used in the ball milling jar is generally 10 to 15 times the mass of powders are used [9] Therefore by considering 10 times the mass of powders used the volume of ball will be 131×104 m3 to legaojm/m account on m/ how to calculate wet ball mill media weight ·

Materials Free FullText Effect of Different Raw Material Property
It is for this reason that the low energy ball mill gave low energy impact to the powder Choi et al [ 15 ] discussed particle size does not change effectively for low rotation speed In addition, a low rotation speed has less effect on powder crystallization due to collisions between particles in the ground powder at low rotation speed having
- حساب تكلفة الإنتاج الكلي للكسارة
- gold ore separation gold mining products
- بكرات في مطحنة الأسطوانة العمودية
- ورقة مطحنة باكستان
- دراسة تجريبية على الطرد المركزي آلة طحن طاقة مفيدة
- mill gold ores at kabrai
- أنواع الحديد المستخدم في المواد الانش
- قائمة معدل للشركات سحق حجر
- اسعار ناقلات الاسمنت السائب بالسعوديه
- gill pin grinding machine
- مصنع بكرات ناقل في الجزائر
- الفحم المعدات وجه محطم
- الفك محطم 00 40 x 3
- hebei concrete mixing plant price
- مبادئ طحن الطاحونة
- تكاليف الانتاج كسارة الحجر آلة كسارة الحجر
- مطحنة الحجر الجيري المستخدمة في زامبيا
- pf1010 impact crusher for mine
- مطاحن تعدين صغيرة الحجم للبيع في المغرب
- مصنع حجر صغير الكسارة
- معدات مصنف عملية طحن الإسمنت
- ball mill for foundry
- الرسم الأساس محطم الفك
- معدات تعدين الذهب كسارة البورون
- كيفية صنع مجموعة سلالة جلدية
- talc grinding mine ppt grinding mill china
- المطرقة مطحنة جنوب أفريقيا
- نموذج خطة عمل كتلة صنع pdf
- آلة صناعية لطحن بذور الكتان والزنجبيل
- mining ore processing gold ore crushinng
- ماليزيا ماكينات التعدين
- لوحات ماجوتو لمطحنة الكرة في اسلام اباد
- بيع ماكينات فرز الخبث
- aggregate crushing mpanies of patna
- شركة زينث معدات الهندسة والمناجم
- مبدأ عمل آلة طحن الكرة العمودية
- تركيب مطحنة مع التكنولوجيا المتقدمة
- stone cone crusher in china
- محطم المعدنية تؤثر سطح
- تأثير محطم من ديتا قسم ايل
- تستخدم آلة طحن لطلاء لبيع
- portable vince hagen cement plant designs
- آلة سحق تأثير للبيع
- تكوين مصنع كسارة الحجر المصرية
- حجر طحن قاعدة باتو الطبخ بالينز
- all gold mines in tanzania
- مشاكل لسحق النظام صر برودة والتعديل
- كيفية حساب طن محطم آلة للساعة الواحدة
- مطحنة رخيصة تستخدم ل
- advantage and disadvantage of vertical milling machining
- بيع كسارة الحجر الجيري الرخام
- البحث عن اراضى كسارات فى السعوديه
- آلات مقلع الحجر الأحمر اللاتريت
- por le dolomite crusher provider india
- تركيز خام الحديد بطرق مختلفة في الهند
- كسارة مخروطية pyd z
- العمود المرفقي طحن ألبومات
- recovery processings equipment spiral iron ore separator
- تدفق الرسم البياني الحديد س محطة كسارة
- إزالة قياس الطحن الأسطواني
- آلة طحن الأساسية أرغان
- meters of mm iron rods how many kgs
- يستخدم مخروط محطم المحمول
- معدات مطحنة طحن الحجر الجيري تغذية حجم 10 مم
- محاجر لوريدا للتعدين والتكسير
- t hr mobile crushing plant
- أحدث مطحنة كسارة السطح
- قائمة أسعار معدات البناء والتعدين
- طاحونة الكرة للبيع مطحنة
- Mobile Crusher Made In America