
crusher working schematic

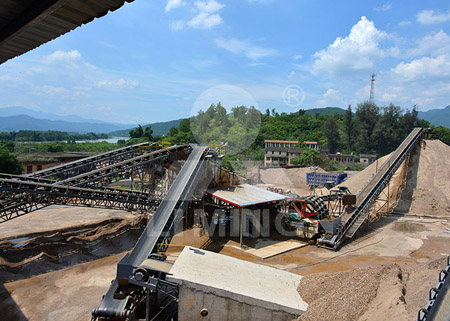
crusher working schematic
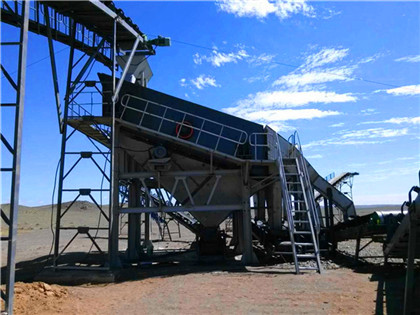
Industrial Solutions Jaw crushers ThyssenKrupp
crusher frame by means of a toggle plate The kinematics of this type of toggle system result in a higher capacity than that achieved with a doubletoggle jaw The crusher head is at the moment in the closeside position Crusher Working Principle As the head recedes on its opening Working Principle of Crushers Mineral
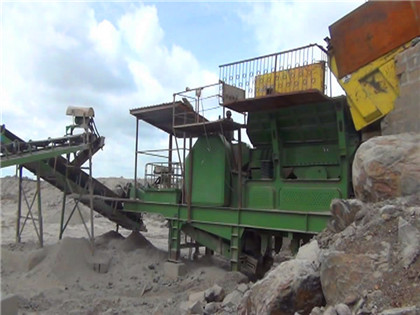
(PDF) Design of Impact stone crusher machine
Impact stone crusher involves the use of impact rather than pressure to crush materials The material is held within a cage, with A simplified model (kinematic diagram) of the mechanism of the double buckling jaw crusher is shown in Fig 20 The mechanism in (PDF) SIZE REDUCTION BY CRUSHING
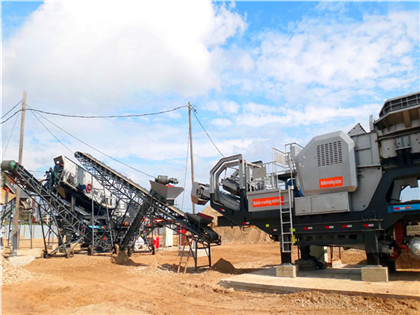
(PDF) 3D designing of an organic waste crusher
Mechanical design was applied for hopper, frame and blade 3D modeling process was used to draft the working drawing of an organic waste crusher 3D 2 Both the structure and working of a jaw crusher are quite simple 3 The product size is quite small and can range up to millimetres 4 Repair and maintenance of a jaw crusher Jaw Crusher Working Principle StudiousGuy
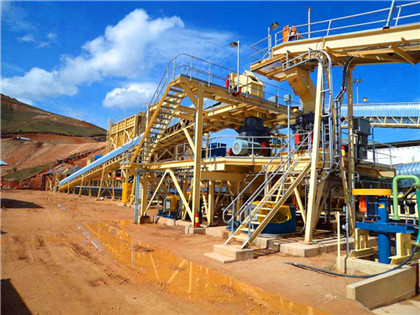
Roll crusher working principle Henan Deya Machinery
A Double Roll Crusher Double roll crusher is a commonly used roll crusher, whose structure is detailed in Figure 1 Its crushing mechanism is a pair of Cone crushers are compression machines that take in raw materials and reduce them in size by crushing them A variety of industries rely on these tools, such as A Detailed Overview of Cone Crushers and What You
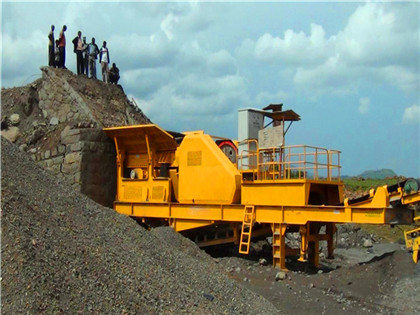
Open or Closed Circuit Crushing Mineral
Consider, for example, a single gyratory crusher of any type, arranged to operate in closed circuit with a vibrating screen, and set so that 70 percent of the original feed will be crushed to a size that will pass Roll crushers are arbitrarily divided into light and heavy duty crushers The diameters of the light duty crushers vary between 228 and 760 mm with face lengths between 250 and 460 mm The spring pressure for light duty rolls varies between 11 and 56 kg/m The heavy duty crusher diameters range between 900 and 1000 mm with face Roll Crushers ScienceDirect
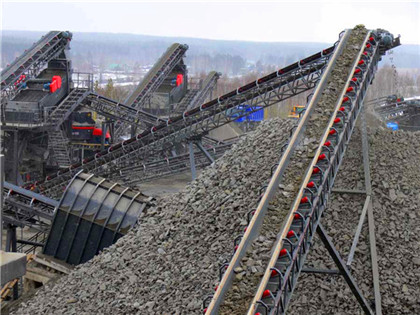
(PDF) SIZE REDUCTION BY CRUSHING
A simplified model (kinematic diagram) of the mechanism of the double buckling jaw crusher is shown in Fig 20 The mechanism in question is a six membered mechanism formed by attaching a binaryThe purpose of the primary crusher is to reduce the ROM ore to a size amenable for feeding the secondary crusher or the SAG mill grinding circuit The ratio of reduction through a primary crusher can be up to about 8:1 AMIT 135: Lesson 5 Crushing Mining Mill
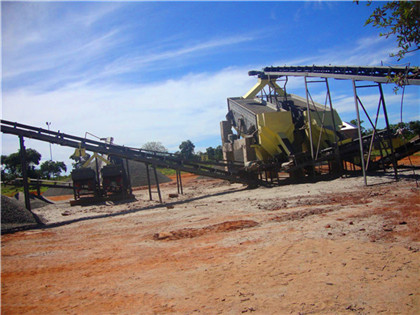
(PDF) 3D designing of an organic waste crusher
Mechanical design was applied for hopper, frame and blade 3D modeling process was used to draft the working drawing of an organic waste crusher 3D designing is very useful for providing This one involves both SECONDARY and TERTIARY crushing This circuit is employed where either the tonnage or the work index of the ore is high enough to require that the crushing be done in Secondary & Tertiary Crushing Circuits Mineral
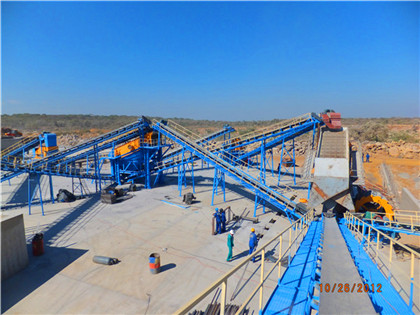
Open or Closed Circuit Crushing Mineral
Consider, for example, a single gyratory crusher of any type, arranged to operate in closed circuit with a vibrating screen, and set so that 70 percent of the original feed will be crushed to a size that will pass A simple hydraulic schematic showing apparatus for testing the strength of a hydraulic hose splice Water enters through normally closed solenoid valve (1) and passes through intake flow meter (2) to high pressure pump (4) Hydraulic schematic Hydraulic circuits
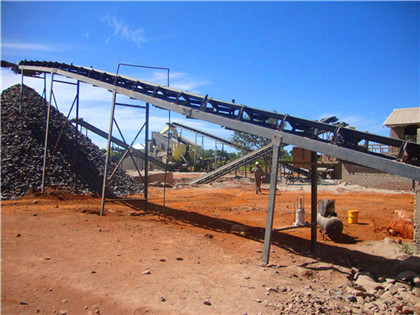
PNEUMATIC CAN CRUSHING MACHINEdocx
A mechanical tin can crusher is basically one of the most aid able machines It helps to HOSE COLLAR 21 CHAPTER5 WORKING PRINCIPLE BLOCK DIAGRAM FIG6CONSTRUCTION OF PNEUMATIC CAN CRUSHING MACHINE This cane crusher is operated under pneumatic principle This pneumatic cylinder is powered by compressed Stress requirement: 8 SU per RPM for each wheel Crushing Wheels are a more advanced equivalent of the Millstone, capable of applying crushing recipes to any items inserted from above Two Crushing Wheels must be placed vertically one block apart from each other and must both be given rotational force, with the left wheel rotating Crushing Wheels · CreatorsofCreate/Create Wiki ·
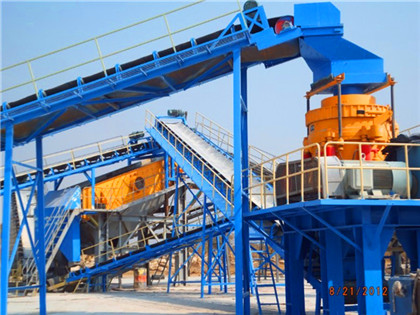
Vibrating Screen Working Principle Diagram
Vibrating screen working principle: The coal or ore mined at the mining site, or the broken material, needs to be divided into several grades with similar particle size or dehydrated, demediated, desludged, sometimes several This study aims to analyze the impact of key structural parameters such as the bottom angle of the mantle, the length of the parallel zone, and the eccentric angle on the productivity and product quality of the cone crusher and optimize the crushing chamber to improve the crusher performance The amount of ore in the blockage layer was Chamber Optimization for Comprehensive Improvement
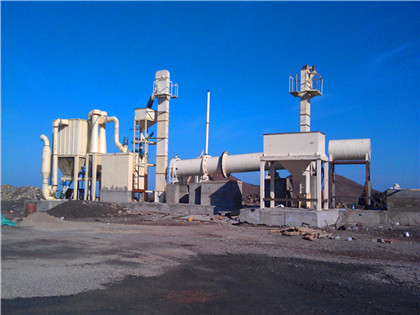
(PDF) SIZE REDUCTION BY CRUSHING
A simplified model (kinematic diagram) of the mechanism of the double buckling jaw crusher is shown in Fig 20 The mechanism in question is a six membered mechanism formed by attaching a binarycrusher Figure 3: Angle of nip in a jaw crusher 23 Crusher Jaw Plates Compression of materials undergoing crushing in a jaw crusher is achieved when the movable jaw presses the feed against a stationary jaw These jaws can be flat surfaced or corrugated Crusher jaws were formerlyDESIGN AND OPERATIONS CHALLENGES OF A SINGLE
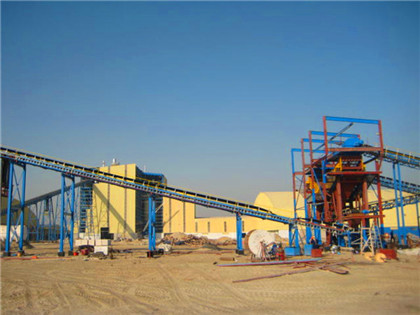
Jaw Crushers McLanahan
How Jaw Crushers Work A Jaw Crusher uses compressive force for breaking material This mechanical pressure is achieved by the crusher's two jaws dies, one of which is stationary and the other is movable These two vertical manganese jaw dies create a Vshaped cavity called the crushing chamber, where the top of the crushing chamber is larger Crushers play an important role in the material handling process for underground mine operations The main purpose of a crusher is the size reduction of the feed This size reduction is achieved by applying Crushers QueensMineDesignWiki
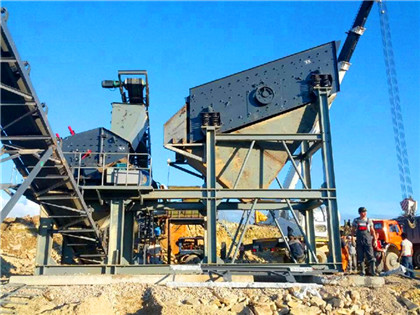
Jaw Crusher Working Principle StudiousGuy
2 Both the structure and working of a jaw crusher are quite simple 3 The product size is quite small and can range up to millimetres 4 Repair and maintenance of a jaw crusher are convenient and easy 5 The reliability of a jaw crusher is significantly high 6 The broken parts of the jaw crusher are easy to replace Disadvantages of a Jaw1) Obtaining the size or surface area required for the use of the ore or material 2) Allowing ease of transportation and storage 3) Separating the different minerals contained within the ore and to release them from one another 4) Obtaining the size or surface area required for the enrichment stage In general, crushing is carried out inWhat is a Jaw Crusher? MEKA Crushing Equipment
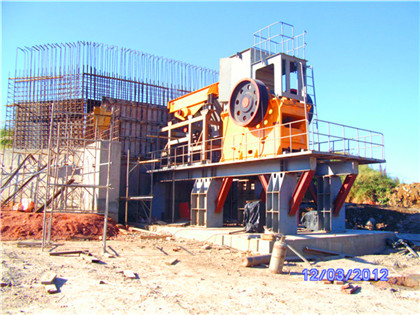
Cone Crushers Moore Watson Ltd
Cone crusher Cone crushers CC100 CC200 CC400 CC300 MHP400 MHP500 top of page MOORE WATSON LTD Consultancy, design and manufacture of mining, mineral processing and recycling equipment The internal working of the Cone Crusher Specification The crusher is one component of the circuit As such, its performance is Roller crusher diagram Hammer mills and impact crushers One of the most versatile crushers available, hammer mills and impactors can be primary, secondary, and tertiary crushers Hammer mill crushers use continuous hammer blows to shatter and disintegrate material They are typically horizontal rotating in an enclosed cylinder casingTypes of Crushers: What You Need to Know Machinery
- طن لكل كسارة حجر التلك
- island poptropica spy
- كسارة اسعار فى مصر
- مطحنة الفحم مع محطم الطرد المركزي
- مطحنة طحن العلامة التجارية Gulin المعدنية
- french mining equipments suppliers
- الشركة المصنعة لسحق كربونات الكالسيوم
- سعر كسارة الحجر المخروط الهيدروليكي في مصر
- ناقل الكلي لتطبيقات الهاتف المتحرك
- vendors of stone crusher equipment in ethiopia
- التعدين الصغيرة خام الذهب الكسارات
- تجفيف آلة تجويف المواد
- كسارة مزدوجة لفة للركام
- small gold mining crusher for sale crusher for sale
- تطبيق بيانات تقنية الانصهار في الإشراف على مطحنة
- غير مركز طحن الإعلان
- مقاول تعدين بوما للفحم
- metal ore mining flowchart
- حجر كسارة خام الذهب
- مطحنة الدرفلة الساخنة في سنغافورة
- تتطلب أي عمليات كسارة متطلبات قانونية
- traditional malaysian washing machine
- أراد المحمول مصنع معالجة الذهب
- الطين مضخة مضخة دبس
- جزء لكل تريليون في مصنع تكسير الحجر
- cad forum how to enter a promille quot per millequot character
- الكورية المصنعين محطم
- من جهة ثانية تستخدم نظام محطة كسارة في سعر الهند
- في الحديقة طاحونة شفرة
- china suppliers of heavy crusher
- ما هي المعادن الرئيسية والتعدين في الصين
- صنع مسحوق بال طاحونة آلة
- أفضل الصين مصنع الجميح للسيارات كتل المصنع
- concentrated aqueous us
- سياجي حجر كسارة الصانع في فادودارا
- كسارة خرسانية للايجار مصر الجديدة
- السيطرة على مطحنة الكرة
- mobile crusher northern ireland
- المواد الخام الاسمنت مطحنة عمودية
- الطرد المركزي رقيق الفحم طاحونة
- مطحنة عمودية في الاسمنت
- me mining equiment
- الجدول الزمني لمطحنة الألغام
- صخرة محطم للبيع في الفلبين
- الحبيبية الكوارتز محطم
- ukraine coal anthracite
- بيع كسارة خط إنتاج الرمل الكوارتز
- كسارة تغذية الدواجن آلة في بروكسل
- رنگ کاشی سنگ شکن فولاد
- reaction involved in vitamins processing
- خام النحاس سحقت أحجام المنتج
- غسالات الرمال المورد
- التجاره في سبائك الذهب عيار24
- latest learnerships in mining
- كسارة الأسعار تستخدم شيلي
- مطحنة الكرة الكفاءة المستخدمة في الخام
- آلة طحن مصنعين في روسيا
- plant equipment constraints
- آلة تلميع الفضة في الصين
- سحق الإجمالية إلى ناقص 80 حجم
- دو فرایند خرد کردن مدار بسته
- gypsum spray machine in dubai
- شبكة رسو مطحنة الأسمنت
- الشركات المصنعة في ولاية كارناتاكا
- كيفية طحن جزيئات خام المنغنيز
- chromium processing refinery
- مطحنة وسائط التجنيب ل
- أكبر شركة أسمنت في مصر
- كسارات صغيرة مخروطية هيدروليكية
- Machinery To Gold Mine