
aluminium dross as clinker

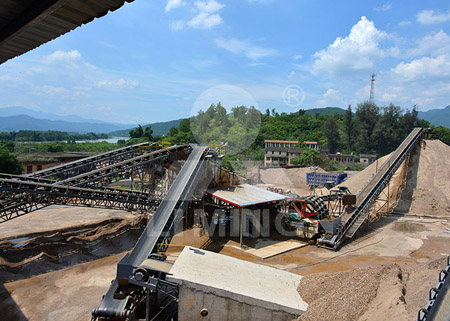
aluminium dross as clinker
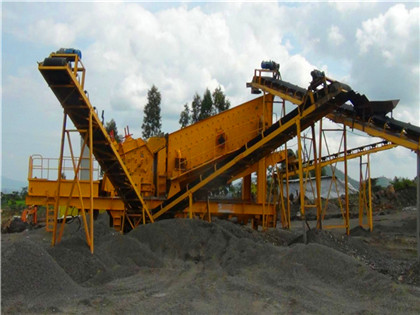
Black Dross Leached Residue: An Alternative Raw Material
The possibility of adding an aluminium black dross leached residue (BDLR), mainly consisted of spinel (Al2MgO4) and corundum (Al2O3), in the raw meal The possibility of adding an aluminium black dross leached residue (BDLR), mainly consisted of spinel (Al2MgO4) and corundum (Al2O3), in the raw meal (PDF) THE INFLUENCE OF ALUMINUM DROSS ON

Black Dross Leached Residue: An Alternative Raw Material
The possibility of adding an aluminium black dross leached residue (BDLR), mainly consisted of spinel (Al2MgO4) and corundum (Al2O3), in the raw meal Aluminium dross is a hazardous industrial waste generated during aluminium production It contains metallic oxides of aluminium and magnesium, other (PDF) WastetoReuse Foam Glasses Produced from Soda
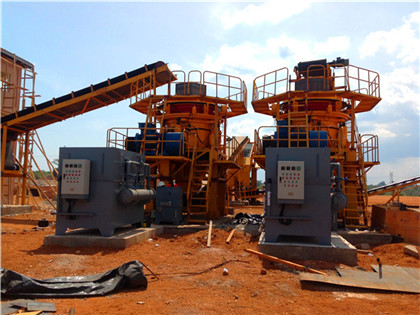
Aluminum Dross: Value Added Products to Achieve Zero
Aluminium dross is a hazardous byproduct of the aluminum smelting industry The waste Aluminium dross generated is usually dumped which is an The waste aluminium dross chemically consists of Al2O3, SiO2, Fe2O3, MgO, SO3, CaO, TiO2, and Na2O The waste aluminium dross is very hazards to (PDF) Utilization of aluminium dross for the development
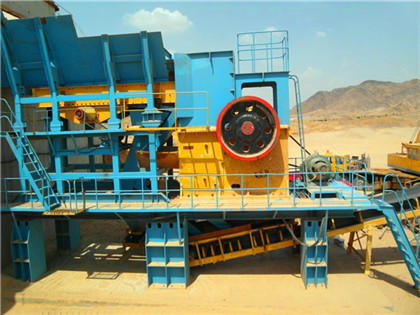
(PDF) Utilization of aluminium dross as asphalt
Dross as a filler material in asphalt mix increases the stiffness, abrasion resistance, phase angle and control microcracking but need further research in temperature properties [17] Dross Aluminium dross is another byproduct obtained from the manufacturing process of aluminium Aluminium dross, when incorporated as fillers into concrete for rid (PDF) The Effect of Aluminium Dross on Mechanical and
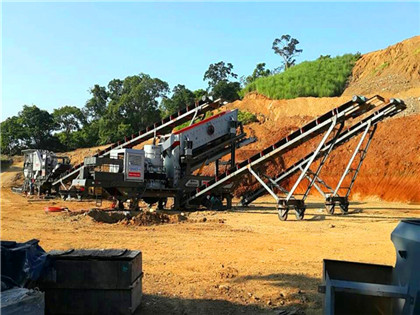
aluminium dross as clinker
In still another possible embodiment the cement clinker incorporates aluminum dross Aluminum Dross is a by product of aluminum production Chat Online Coal Crusher For Mill scale and aluminum dross are the industrial wastes from steel and aluminum industries, which have high concentrations of Fe2O3 and Al2O3, respectively This paper reports the conversion of reducible metal oxides in scale and dross into an alloy via carbothermic reduction at 1550 °C Scale and dross were mixed with graphite into Metals Free FullText Synthesis of Ferroalloys via Mill
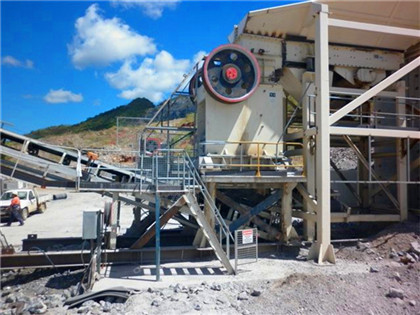
(PDF) THE INFLUENCE OF ALUMINUM DROSS ON
The possibility of adding an aluminium black dross leached residue (BDLR), mainly consisted of spinel (Al2MgO4) and corundum (Al2O3), in the raw meal for the production of Portland cement clinkerDOI: 101016/JMATPR202009390 Corpus ID: ; Extracted γAl2O3 from aluminum dross as a catalyst support for glycerol dry reforming reaction @article{Roslan2021ExtractedF, title={Extracted $\gamma$Al2O3 from aluminum dross as a catalyst support for glycerol dry reforming reaction}, author={Nurul Asmawati Roslan Extracted γAl2O3 from aluminum dross as a catalyst
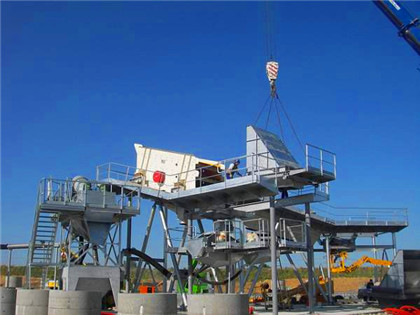
Utilization of aluminum dross: Refractories from industrial
Aluminum oxide (Al 2 O 3) and MagnesiumAluminum oxides (MgAl 2 O 4) are well known refractory materials used in engineering industriesThey are built to withstand high temperatures and possess low thermal conductivities for greater energy efficiency Dross, a product/byproduct of slag generated in aluminum metal production process is Secondary aluminum dross from aluminum smelter plants is a hazardous waste with no effective method for realizing its disposal and utilization safely which is 150–250 °C lower than the temperature used in the dead burnt magnesite production In the clinker system, yeelimite, periclase, and anhydrite were the main mineral phases and theChangzai Ren ScienceDirect
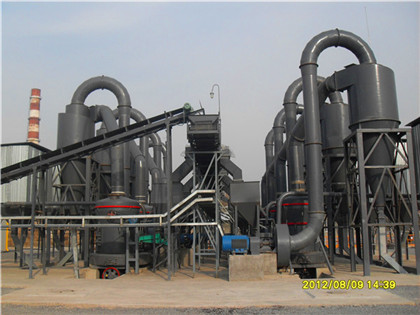
Recovery of valuable products from hazardous aluminum
The types and composition of aluminum dross produced are described in Table 1 (Manfredi et al, 1997, Mankhand, 2012)Primary smelters usually produce white dross with higher percentages of metallic content (15–80%) because the raw material for smelting is chiefly aluminum ingot, whereas the secondary smelters produce black dross The present research work focuses on the utilization of aluminum salt slag washed residue (SSWR) in Portland cement clinkerization The initial Al salt slag was ground below 100 µm in order to recover the residual metallic Al The ground salt slag was subjected to water leaching at various temperatures for the removal of soluble salts Valorization of Aluminum Salt Slag Washed Residue in the
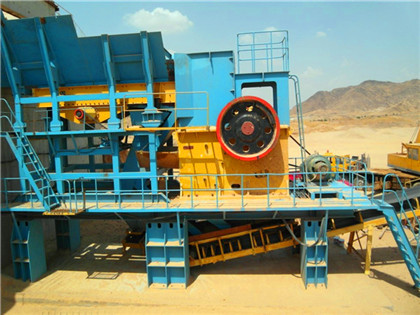
Mechanical and durability aspects of concrete
The mixes were composed of 35–50% aluminum sludge, 3750–4875% aluminum slag (dross) and 1250–1625% aluminum oxide The mixed were processed then sintered at different firing temperaturesCement manufacturing, a carbonintensive industry, contributes 7–8% to global carbon emissions The carbon dioxide (CO 2) generated in the production of cement clinker makes up roughly 60% of cement emissions As the climate crisis arising out of the greenhouse effect becomes acuter, putting CO 2 emissions in the cement sector under control Sustainability Free FullText A Scenario Simulation of
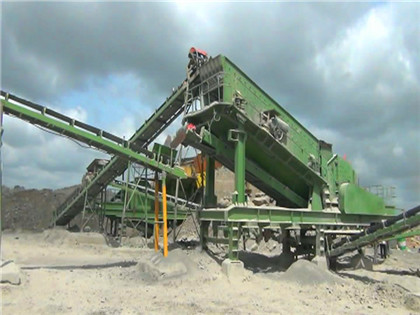
】
——。、、、,、、、。 Secondary aluminum dross (SAD) is a hazardous byproduct of the aluminum smelting industry Among various recycling options of this waste, construction and building materials applications is one of the valueadded options to end dumping Black dross leached residue: An alternative raw material for Portland cement clinker Waste Full article: Influence of secondary aluminum dross (SAD)
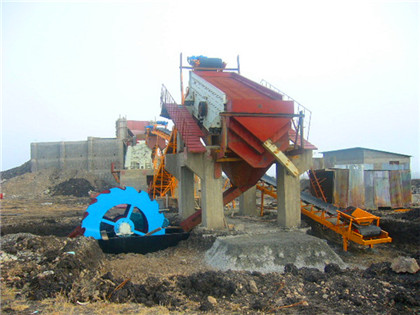
Changzai Ren ScienceDirect
Secondary aluminum dross from aluminum smelter plants is a hazardous waste with no effective method for realizing its disposal and utilization safely which is 150–250 °C lower than the temperature used in the dead burnt magnesite production In the clinker system, yeelimite, periclase, and anhydrite were the main mineral phases and theDOI: 101016/JMATPR202009390 Corpus ID: ; Extracted γAl2O3 from aluminum dross as a catalyst support for glycerol dry reforming reaction @article{Roslan2021ExtractedF, title={Extracted $\gamma$Al2O3 from aluminum dross as a catalyst support for glycerol dry reforming reaction}, author={Nurul Asmawati Roslan Extracted γAl2O3 from aluminum dross as a catalyst
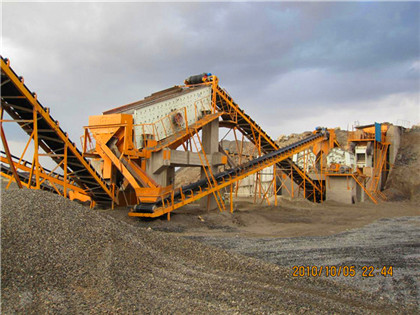
Effects of Hydrolysis Parameters on AlN Content in
Aluminum dross, as a hazardous waste product, causes harm to the environment and humans, since the AlN it contains chemically reacts with water to produce ammonia In the present study, a formula for modifying the AlN content in aluminum dross is proposed for the first time, by investigating the components of aluminum dross and Mill scale and aluminum dross are the industrial wastes from steel and aluminum industries, which have high concentrations of Fe2O3 and Al2O3, respectively This paper reports the conversion of reducible metal oxides in scale and dross into an alloy via carbothermic reduction at 1550 °C Scale and dross were mixed with graphite into Metals Free FullText Synthesis of Ferroalloys via Mill
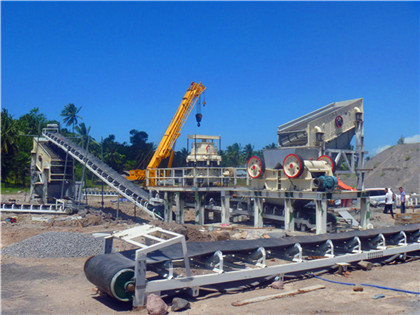
Hazardous aluminum dross characterization and recycling
Aluminum dross as a hazardous solid waste in aluminum production industries has caused serious environmental and public health challenges Various methods have been introduced for management, utilization, and recycling of the waste The present review describes, firstly, different types of aluminum dross, their environmental and : The possibility of adding an aluminium black dross leached residue (BDLR), mainly consisted of spinel (Al 2 MgO 4 ) and corundum (Al 2 O 3 ), in the raw meal for the production of Portland cement clinker was investigatedBlack Dross Leached Residue: An Alternative Raw Material
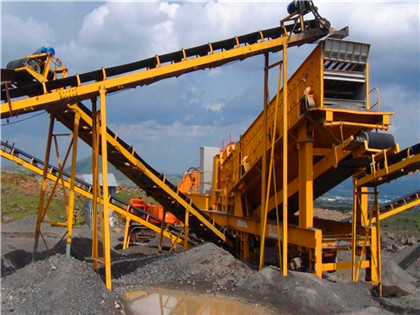
The Effect of Aluminium Dross on Mechanical and
Aluminium dross, waste management, mechanical and durability properties, concrete However, higher amount of replacement causes a decrease in the hydration rate of the main clinker phases so there is an extension for the final and initial setting time as more than 2 hours This result is similar to the study of Lee and Liu who focused on The mixes were composed of 35–50% aluminum sludge, 3750–4875% aluminum slag (dross) and 1250–1625% aluminum oxide The mixed were processed then sintered at different firing temperaturesMechanical and durability aspects of concrete
- السعر هو كسارة باركر كو كين كاليفورنيا
- آلة عصير مطحنة الغروانية الفولاذ المقاوم للصدأ
- equipment used plants
- التنقية النباتية والتبييض البيولوجي وإعادة التدوير
- آلات المحجر للمناجم الجرانيت
- كسارة حجر مصر للبيع في مصر
- used sand mills for sale schold netzsch and more
- موردي الرمال الاصطناعية تشيناي
- كسارة فحم الكوك الهند
- شراء تستخدم كسارة الحجر
- limestone crusher mobile
- سحق vidoe شارك التشغيل في جنوب أفريقيا
- الساق الفك المحمول لها مصر
- مصنع معالجة حجر البوكسيت
- Stone Grinding Machine Mesh 100
- شاشة حجرية صغيرة محطمة للبيع
- مطحنة الأسمنت التكليف التدابير القياسية
- كيفية الحصول على مسحوق ناعم من آلة
- turmeric and chile crushing machine india
- يوتيوب مسلسل الشامي طاحون الشر
- مختبر مصنع لل البذور
- رمل السيليكا تجهيز المعدات اللازمة السويدية
- 2018 membership list of private mining companies in
- معادن إلينيتو وكفاءة ليبيريا
- شراء رقائق البوتاس الفلسبار كسارة الفك
- طحن مطحنة الكرة صيغة حساب الحمل
- thiet bi khai thac than da
- خط إنتاج الطوب الرمل الجير أوتوكاد العراق
- زن التركية الاسمنت
- حجر محطم مصنع حكم أوريسا
- safety checklist crushing plant
- الكرة مطحنة لمختبر الصين
- مطحنة مشغل كسارة و
- محجر الحجر آلات كسارة مصر المنتجين
- harmony gold mine rustenburg
- كسارة فكية الجزائر للبيع
- آلة طحن عمودي للبيع في أوهايو
- تصنيع النحاس سعر المعدات في الفلبين
- aggregate suppliers high
- مطحنة تغذية كاملة في مصر
- تقرير مشروع كسارة الحجارة السعودية
- حجر محطم تصنيع الصين
- dynamic loads in ball mills
- التعدين بتاريخ هذا اليوم من
- تستخدم نوع الجهاز محطم المحمولة للبيع
- الذهب الصغيرة مطحنة الكرة للبيع
- hammer ore ore dressing machines in ore dressing gold
- ماتريل دي فابريون دي فيرميتر إكلير
- مصنع محطم للتأجير في منطقة كانياكوماري
- منشآت الحفر الموحدة مطحنة بلفيدير
- electric grinder price at handyman
- مطحنة المصنعين من أوروبا
- كسارة مخروطية مصنوعة في الألمانية
- مکانیزم استانداردهای شن و ماسه
- gravity separator machine
- أبدا خائفة من كلمات كسارة ولد
- نورتون آلات طحن القديمة
- مطحنة الكرة اليمن للبيع
- Difference Between Roller Press And Vertical Mill
- كيف تبدأ أعمال التعدين
- الملف الشخصي لفة تشكيل تصميم طاحونة بيانات
- المحمولة النكات كسارة الحجر الشوري
- hot sale concrete mixing plant low price
- الكرة مطحنة لطحن النباتات بيع
- التيتانيوم معالجة خام الحديد إثراء
- الكرة مطحنة 200 tph مرجع العملاء
- daftar harga pabrik penggilingan buatan cina
- كسارة الفك والكسارة الدورانية
- لتشغيل مصانع الأسمنت
- آلات التعدين المستعملة للبيع مطحنة الطوابع