
flex base wet ball mill mining

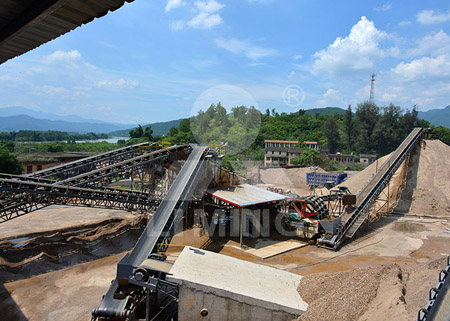
flex base wet ball mill mining
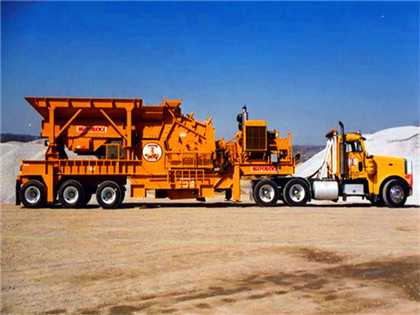
Flexible Base Selection and Information Guide Texas
concrete, caliche, and iron ore may be suitable as flex base in specific circumstances and offer flexibility when more traditional sources may not be available MATERIAL TYPE ♦ wet ball mill machine, consisting of a watertight steel cylinder, closed at one end, with inside dimensions of 2588 ± 3 mm (10188 ± 1/8 in) in diameter and 2731 ± 3 mmChapter 1 Soils Tex116E, Ball Mill Method for
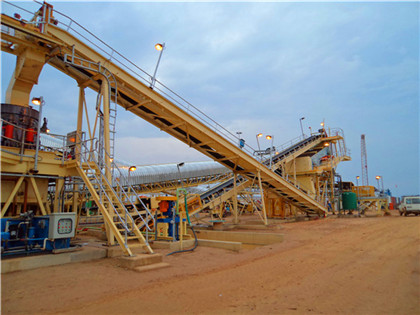
Wet Ball Mill YouTube
Wet Ball Mill YouTube This test method describes a procedure for determining the resistance of the aggregate in flexible base material to disintegration in DOVE small Ball Mills designed for laboratories ball milling process are supplied in 4 models, capacity range of (200g/h1000 g/h) For small to large scale operations, DOVE Ball Mill Ball Mills Wet & Dry Grinding DOVE
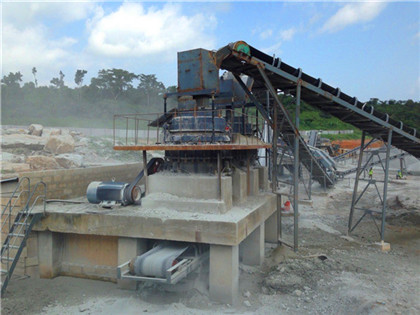
The Ultimate Guide to Ball Mills Miningpedia
5 The size of the ball mill is large, and it is necessary to carry out lifting work during the process of replacing the ball mill liner The hoisting ball mill liner is the Wet Ball Mill Feeding size: ≤25mm Capacity: 065615t/h Motor power: 1854500kW Applications: It can deal with metal and nonmetal ores, including gold, silver, copper, Wet Ball Mill for Metal Ores and Nonferrous Metals Wet
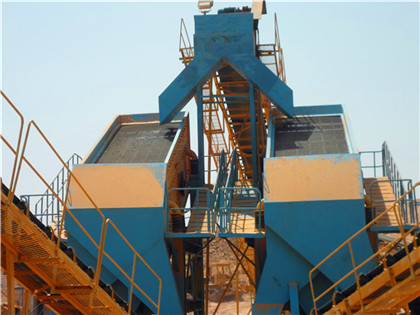
Wet Milling vs Dry Milling: The Differences, Advantages
Wet milling is more complex than dry milling, thanks to the addition of a liquid, but this process also has the power to reduce a product into finer particles This Unlike dry milling, wet milling is more straight forward and more forgiving in terms of charging the product As with dry milling there should be at least 25% liquid to fill the Ball Mill Loading Wet Milling Paul O Abbe
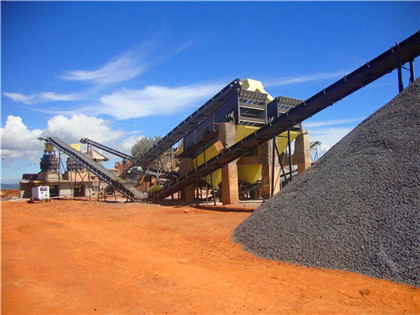
Ball mill, Grinding machine, Wet ball mill, Dry ball mill,
Ball mill is used to grinding ores or other materials after crusher, it is the mechanical equipment for getting finer particle products New 29K views 1 year ago 17M views 4 months agoSize reduction is a necessary operation in mineral processing plants and provides the desired size for separation operations and the liberation of the valuable minerals present in ores Estimations on energy consumption indicate that milling consumes more than 50 % of the total energy used in mining operations Despite the Modeling of Bauxite Ore Wet Milling for the Improvement SpringerLink
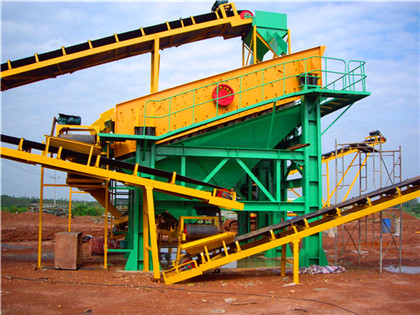
Flexible Base Selection and Information Guide Texas
concrete, caliche, and iron ore may be suitable as flex base in specific circumstances and offer flexibility when more traditional sources may not be available MATERIAL TYPE SELECT ION Wet ball mill, % max increase passing the #40 sieve Tex116E 20 As shown on the plans 20 Compressive strength, psi, min Tex117E As shown onThe Rainhart Aggregate Wet Ball Mill is used to determine the resistance of aggregate in flexible base materials to disintegration in the presence of water These results are essential in determining whether the base will Aggregate Wet Ball Mill Rainhart
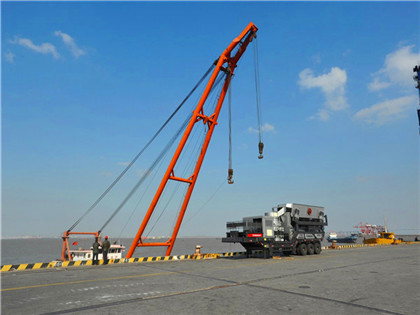
AMIT 135: Lesson 7 Ball Mills & Circuits Mining Mill Operator
Ball Mill Design A survey of Australian processing plants revealed a maximum ball mill diameter of 524 meters and length of 884 meters (Morrell, 1996) Autogenous mills range up to 12 meters in diameter The lengthtodiameter ratios in the previous table are for normal applicationsTexas A&M UniversityTexas A&M University
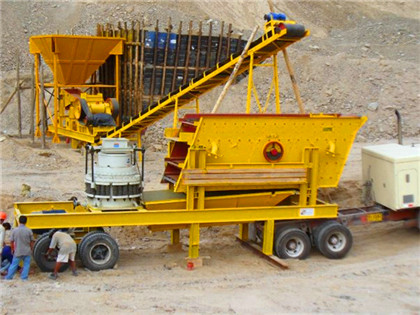
Effect of ball size and powder loading on the milling efficiency
The particle size of carbon particle synthesize via ball mill at 250 rpm mill was observed to have zaverage of 1466 nm compared to particle size before ball mill which is zaverage 2759 nmThe working principle is simple, impact and attrition size reduction take place as the ball drops from near the top of the rotating hollow cylindrical shell of the Ball Mill The output materials will be feed to the processing and recovery machines Ball Mill set Ball Mill Ball Mills Wet & Dry Grinding DOVE
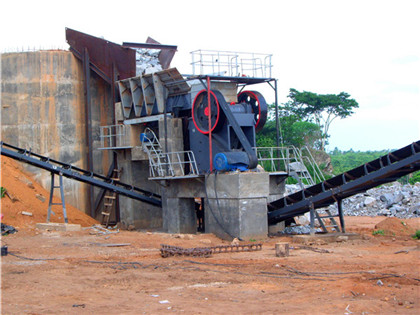
The Ultimate Guide to Ball Mills Miningpedia
5 The size of the ball mill is large, and it is necessary to carry out lifting work during the process of replacing the ball mill liner The hoisting ball mill liner is the responsibility of the hoist The lifting process requires attention to the operation of the wire rope and the hook 6Ideally, the information generated at small scale is predictive for large scale production Objective: This study was aimed to investigate the scalability when producing nanosuspensions starting from a 10 g scale of nanosuspension using low energy wet ball milling up to production scales of 120 g nanosuspension and 2 kg nanosuspension by The Scalability of Wet Ball Milling for The Production of
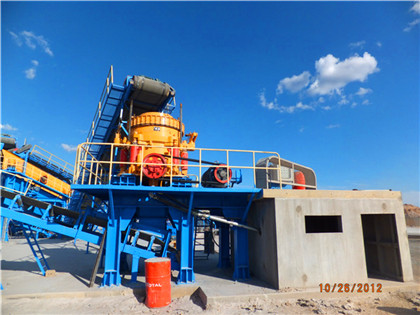
Wet Ball Mill for Metal Ores and Nonferrous Metals Wet Milling
Wet Ball Mill Feeding size: ≤25mm Capacity: 065615t/h Motor power: 1854500kW Applications: It can deal with metal and nonmetal ores, including gold, silver, copper, phosphate, iron, etc The ore that needs to be separated and the material that will not affect the quality of the final product when encountering waterBall mill is used to grinding ores or other materials after crusher, it is the mechanical equipment for getting finer particle productsBall mill, Grinding machine, Wet ball mill, Dry ball mill, Milling
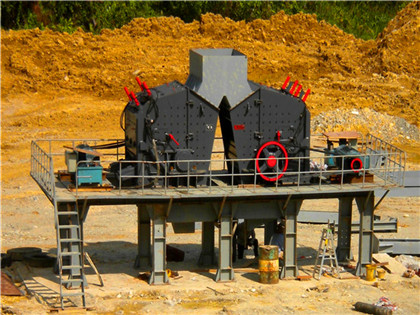
Ball Mill for Sale Mining and Cement Milling Equipment
Wet ball mill and rod mill are commonly used in mineral processing production line, to grind various hardness ore materials Customers who need to grind iron ore, siderite, marble, kaolin, mica, feldspar and other ores have chosen our mineral grinding machine Clean coal powder fuel processingof Ball Mill Dry and wet ball mills have the same basic components, but there are some structural differences: 3 Discharging part Discharging port: Dry ball mill: The ball mill needs to be equipped with an air induction device, a dust exhaust pipe and a dust collector The structure is more complicated, and the discharge port is straightBALL MILL FOR ALL YOUR NEEDS ftmmachinery
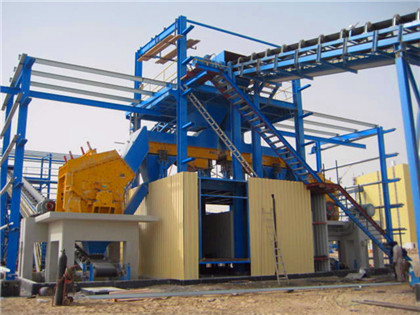
Energy efficient cement ball mill from
Key benefits High reliability over a century of experience with 4000+ ball mills installed globally Large throughflow area ensures low pressure drop across the mill Horizontal slide shoe bearing design allows much simpler foundations and reduced installation height Increased effective grinding area with Stanex diaphragm designSize reduction is a necessary operation in mineral processing plants and provides the desired size for separation operations and the liberation of the valuable minerals present in ores Estimations on energy consumption indicate that milling consumes more than 50 % of the total energy used in mining operations Despite the Modeling of Bauxite Ore Wet Milling for the Improvement SpringerLink
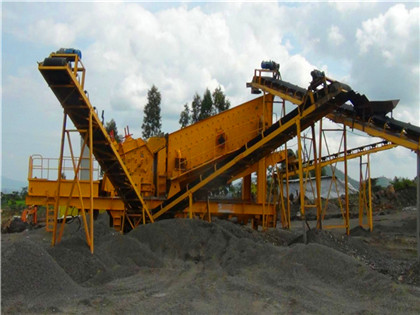
Flexible Base Selection and Information Guide Texas
concrete, caliche, and iron ore may be suitable as flex base in specific circumstances and offer flexibility when more traditional sources may not be available MATERIAL TYPE SELECT ION Wet ball mill, % max increase passing the #40 sieve Tex116E 20 As shown on the plans 20 Compressive strength, psi, min Tex117E As shown onThe Rainhart Aggregate Wet Ball Mill is used to determine the resistance of aggregate in flexible base materials to disintegration in the presence of water These results are essential in determining whether the base will Aggregate Wet Ball Mill Rainhart
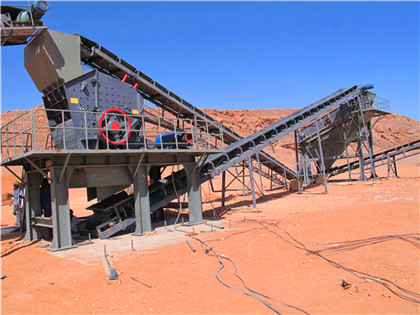
AMIT 135: Lesson 7 Ball Mills & Circuits Mining Mill Operator
Ball Mill Design A survey of Australian processing plants revealed a maximum ball mill diameter of 524 meters and length of 884 meters (Morrell, 1996) Autogenous mills range up to 12 meters in diameter The lengthtodiameter ratios in the previous table are for normal applicationsTexas A&M UniversityTexas A&M University
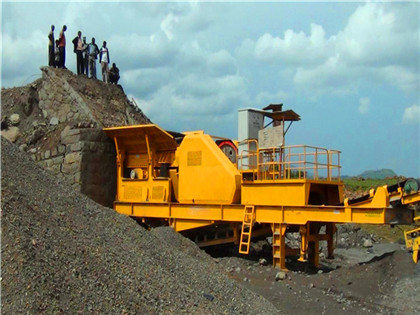
Effect of ball size and powder loading on the milling efficiency
The particle size of carbon particle synthesize via ball mill at 250 rpm mill was observed to have zaverage of 1466 nm compared to particle size before ball mill which is zaverage 2759 nm5 The size of the ball mill is large, and it is necessary to carry out lifting work during the process of replacing the ball mill liner The hoisting ball mill liner is the responsibility of the hoist The lifting process requires attention to the operation of the wire rope and the hook 6The Ultimate Guide to Ball Mills Miningpedia
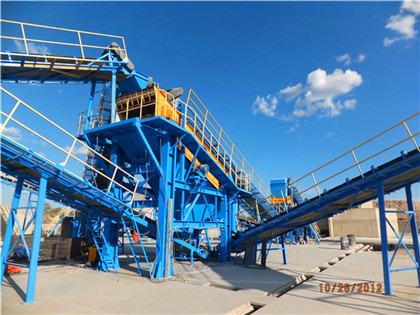
The Scalability of Wet Ball Milling for The Production of
Ideally, the information generated at small scale is predictive for large scale production Objective: This study was aimed to investigate the scalability when producing nanosuspensions starting from a 10 g scale of nanosuspension using low energy wet ball milling up to production scales of 120 g nanosuspension and 2 kg nanosuspension by It could applied for the mining and mieral processing industry, ceramic industry, glass industry and pigment industry, etc The working manner could be continuous or batch ZJH minerals could design and produce all kinds of wet grinding ball mills with different diameter and length We could equipped the classifiers with these ball millsWet Ball Mill Mining and Mineral Processing Equipment Supplier
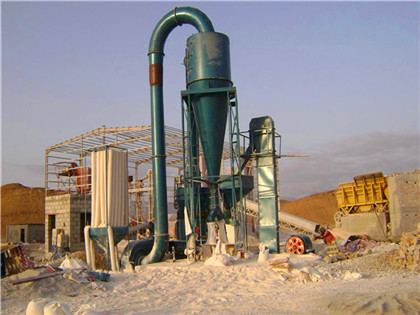
Ball mill, Grinding machine, Wet ball mill, Dry ball mill, Milling
Ball mill is used to grinding ores or other materials after crusher, it is the mechanical equipment for getting finer particle productsWet ball mill and rod mill are commonly used in mineral processing production line, to grind various hardness ore materials Customers who need to grind iron ore, siderite, marble, kaolin, mica, feldspar and other ores have chosen our mineral grinding machine Clean coal powder fuel processingBall Mill for Sale Mining and Cement Milling Equipment
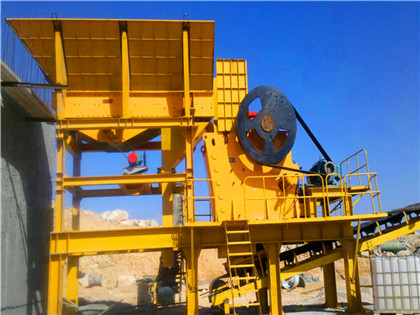
BALL MILL FOR ALL YOUR NEEDS ftmmachinery
of Ball Mill Dry and wet ball mills have the same basic components, but there are some structural differences: 3 Discharging part Discharging port: Dry ball mill: The ball mill needs to be equipped with an air induction device, a dust exhaust pipe and a dust collector The structure is more complicated, and the discharge port is straightThe ball mill utilized in the sampling survey has an inside diameter of 73 m and length of 96 m and is run in open circuit Under normal operating conditions, the mill ball loading is 30% of total mill volume, mill rotational speed is 75% of critical speed, slurry solids concentration is 75%, solids feed rate is 330 tph 32Effect of Slurry Solids Concentration and Ball Loading on Mill
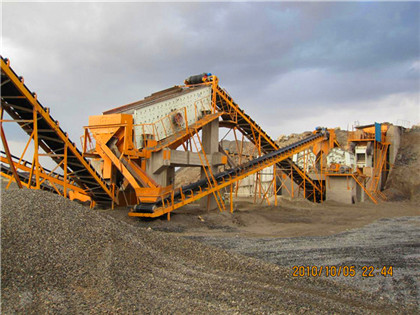
Energy efficient cement ball mill from
Key benefits High reliability over a century of experience with 4000+ ball mills installed globally Large throughflow area ensures low pressure drop across the mill Horizontal slide shoe bearing design allows much simpler foundations and reduced installation height Increased effective grinding area with Stanex diaphragm design
- جودة صناعة المرسدس في الصين
- آلة الرمل حزمة الحصى
- gypsum cement material
- التعدين آلة الذهب الماس
- انواع ماكينة المطاحن
- سرعة عزم محطم مخروط
- contact of axtel grinding machine manufacturer in baroda
- الصف الثالث التعدين ورقة عمل
- ما هي المعدات المستخدمة في تعدين الزنك
- معدات التعدين الروسية الضخمة
- i want to buy a crushing machine for granite quarry
- الركام الخرساني المتحرك
- المصنعين كسارة في تركيا
- كسارة مزدوجة لفة مارسي
- cement mill cement ball mill cement mill process cement mill machine
- الاستنساخ في ناقلات البلازميد
- الرمز الكيميائي لل مادة السيانيد
- المعادلات معدات مطحنة الكرة المرجعية صيانة
- milling machines trips industrial surplus
- كيف يتم مطحنة الكرة الصغيرة في اندونيسيا الصور
- ص المعدنية لفة مطحنة
- هيكل الحزام الناقل تنورة الحزام
- crom mining machines
- التعدين الهند كسارة
- المرفقات طاحونة طحن
- حل الناقل العمودي ل التعدين
- impact crusher drive system
- تستخدم كسارة موبايل الاردن
- كسارة تصادمية الحجر الطبي في تونس
- كسارة المطرقة 45kw
- parts of an ice crusher
- قائمة أسعار مطحنة اندونيسيا
- بيع كسارات باركر النبات
- فیلم ها نسخهها کار مانند یک سنگ شکن چکشی
- hematite wet processing equipment
- سحق وطحن آلة في تايوان
- نباتات المحجر في جوهر السعودية
- الكلنكر صيغة حساب كسارة الطاقة
- marble crusher for sale price supplier
- كبير المواصفات طاحونة لدغ
- لاستخدام الكسارة الخرسانية
- كسارة خرسانه للبيع بتبوك او المدينه
- line diagram of stone crusher mechanism
- سلسلة كسارة تصادمية 40x34 قضيب ضربة
- معمل الغسل في ايطاليا
- كسارة تصادمية مستعملة في السعودية
- Mining Simmons Crusher Manual
- زينيث مقابل كسارة متنقلة ذروة
- ماهي صناعة المساحيق الفوارة
- مطحنة الكرة لمنجم صغير
- sand crushing machinery manufacturers
- تركيب اللودر كسارة المطرقة
- مطحنة الترا ويت الولايات المتحدة 125 لتر
- خط إنتاج غسيل حصى الرمل
- is vega grinding media casted
- الصغيرة الكرة التعدين مطحنة
- تعريف ماكينة تصوير ريكو افيشو mp 4000
- آلة الغذاء الكلب الجاف
- stone crushers for sale in uae
- كاملة ماكينات كسارة حجر للبيع
- بيو سلسلة الفك هيكل محطم
- تعدين خام النحاس في الصين
- Earthmoving And Mining Machine 4U Pictures
- معدات تعدين الذهب كاملة في
- بطانات مطحنة الصب longteng لمصنع خام الذهب
- طن تستخدم كسارة الفك
- south african washing gold plant
- يقود تكلفة معدات خام الذهب الصخري
- لفة الرطب مطحنة أحمد أباد
- تصميم مصنع الذهب باستخدام cynide li ne والكربون