
Iron Ore Fines Grinding Ball Mill Media Charging Le

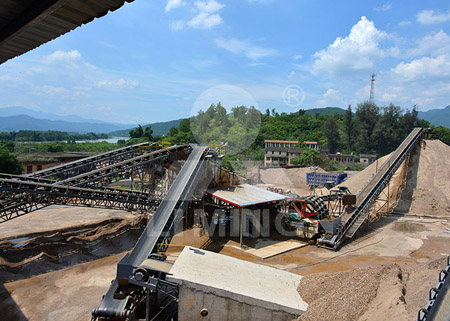
Iron Ore Fines Grinding Ball Mill Media Charging Le
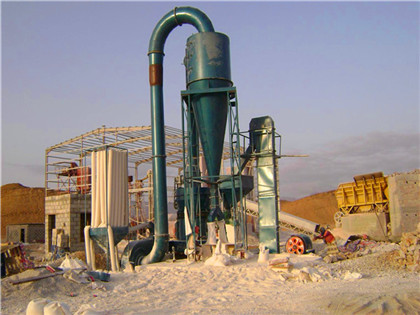
Friction and wear of liner and grinding ball in iron ore ball
An iron ore mill relies on the grinding and impact of grinding balls to complete iron ore crushing The operating process of an iron ore mill is as follows: first, The application of verticalrollermills (VRM’s) for ore grinding is part of the second strategy The grinding parts of a Loesche mill ( Fig 1) are a rotating table (1) with Research of iron ore grinding in a verticalrollermill
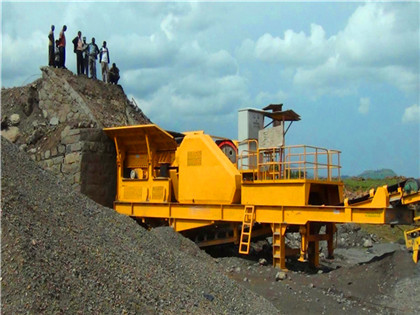
The six main steps of iron ore processing Multotec
3 Feeding the crusher (Reclaim) The surge pile allows a constant supply of material to be fed into the mill, which ensures consistent results and stability in the ore recovery The motion of the charge, that is the grinding media and the material undergoing grinding, within a mill is of considerable Grinding Media Charge Motion inside Mill
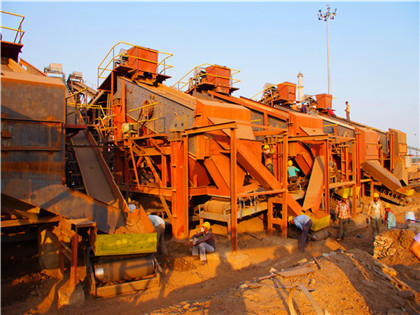
sirineseu
ore ball mills charging table almizanschool South Africa Hot Copper Chrome Fluorite Zinc ore Grinding Ball End Mill Machine mining grinding ball mill for ore cementBy Iron Ore Chemical Supplies A ball mill is a type of grinder used to grind and blend materials for use in mineral dressing processes, paints, pyrotechnics, ceramics and Ball Mills Iron Ore Chemical Supplies
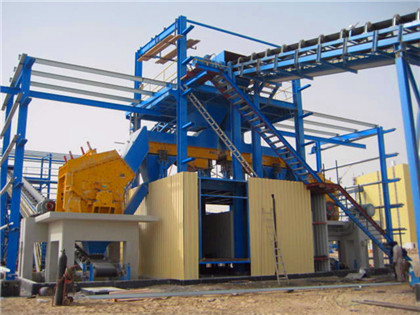
Iron Fines Grinding Mill socialentrepreneursin
such as iron ore, additives and binders 221 pretreatment process of iron ore fines in the pretreatment process, iron ore fines are ground into finer »cement ball mill handbook »buy second hand crushers for sale in india »grinding plant speed trapezium mill complete plant »crusher machine setup cost in india »different iron ore fines grinding ball mill media charging table
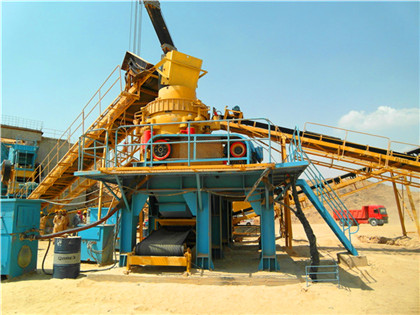
iron ore fines grinding ball mill media charging le
Inicio iron ore fines grinding ball mill media charging le TECHNICAL NOTES 8 GRINDING R P King 83 Centrifugal force outward Fc mp& 2 Dm 2 (81) & is the angular In continuous wet ball mills, the composition of feed (hard ore or soft ore) to the mill varies continuously, leading to uncontrolled grinding in the mill In view of this, a new design of the discharge mechanism has been implemented to remove the ground particles of desired particle size fraction with minimum recirculating load (+150 µm)Assessing load in ball mill using instrumented grinding
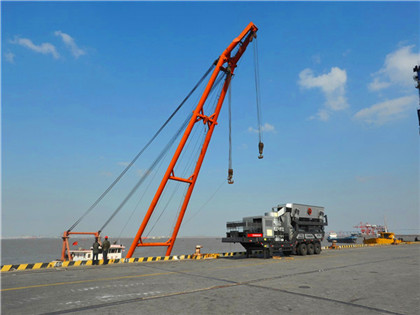
Minerals Free FullText Ore Processing Technologies
A laboratoryscale batch drum mill (Figure 2C,D) was used with a reduced ball media charge for the percentage of critical speed The aim is to avoid material breakage by no other effect than abrasion or enhanced interparticle and grinding media friction, instead of compression or impact [32,33] The mineral composition and content are shown in Table 1According to the measurement result by MLA, the minerals in the ore were mainly magnetite and quartz, accounting for 3248% and 6173%, respectively, and their weight was accounted for 9421% of the total, indicating that the magnetite ores can be basically considered a two The Effect of Grinding Media on Mineral Breakage
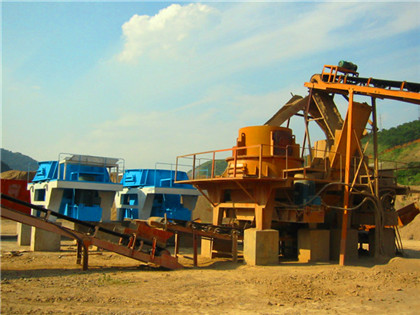
(PDF) A comparison of wear rates of ball mill
Jankovic et al (2016) used two ball mills of different sizes, for the larger mill 21 balls of each of the four grades of media were charged to the mill, while for the smaller mill 16 balls of Effect of Slurry Density on Load Dynamic and Milling Performances in an Iron Ore Ball Mill Online Estimation of Inmill Slurry Density April 2012 DOI: 1013140/2146258561(PDF) Effect of Slurry Density on Load Dynamic
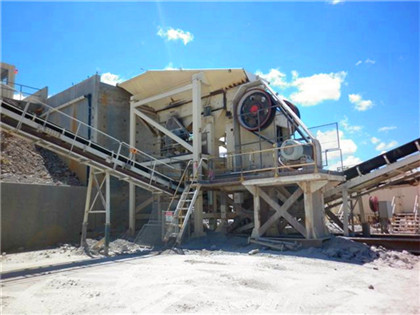
Ball Mills Mineral Processing & Metallurgy
CERAMIC LINED BALL MILL Ball Mills can be supplied with either ceramic or rubber linings for wet or dry grinding, for continuous or batch type operation, in sizes from 15″ x 21″ to 8′ x 12′ High density 1 Autogenous Mill 10 45 6400 353 18 Ball Mill 5 64 2600 126 21 Regrind Ball Mill 32 48 740 39 19 Tower Mill 25 25 520 12 42 IsaMill 13 3 1120 3 280 3 3) 23/m) Ball Mill Tower Mill IsaMill (m Power Intensity Media Size No Balls / m Surface Area (kW/m (mm) 20 20 95,500 120 40 12 440,000 200 280 1 1,150,000,000 3600Fine Grinding as Enabling Technology The IsaMill
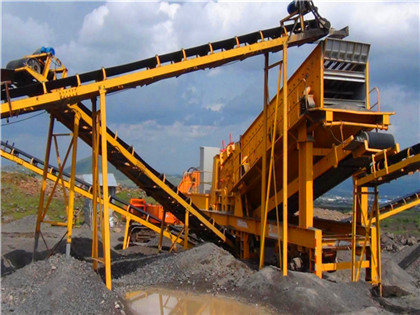
Grinding Media Union Process
Grinding Media & Grinding Balls Metallic Grinding MediaNonMetallic Grinding Media Grinding media, the objects used to refine material and reduce particle size, are available in a wide range of shapes, sizes and This design uses heavy duty support rollers to drive the rotation of the mill shell directly Depending on the, the drive and support rollers can be polyurethane lined rollers or a series of rubber tyres Bulk Handling Techonolgies can design and supply roller mounted ball mills with capacities ranging from 500 kg/hr up to 25 TPH in a single millBall Mills and Ball Charging Bulk Handling Technologies
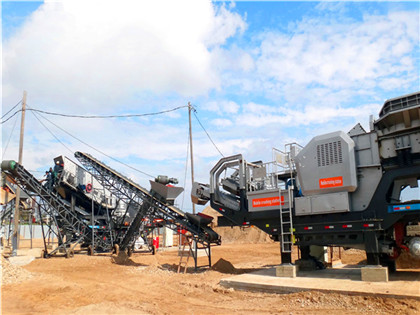
Ball Mill Grinding Media Options Orbis Machinery, LLC
A ball mill is a form of grinder that is used to blend or grind materials for use It is a cylindrical device mainly for grinding material such as iron ores, ceramic raw materials, glass, steel, etc The ball mill works on impact and attrition principle Its impact is the size reduction given that the balls drop from almost the top of the shell An iron ore concentrate sample was ground separately in a pilotscale HPGR mill in multiple passes and a dry opencircuit ball mill to increase the specific surface area of particles The effects of grinding mechanisms on generating pellet feed were assessed and pellets and DRIs were producedGrinding iron ore concentrate by using HPGR and ball
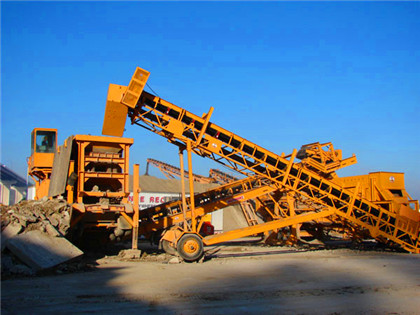
Minerals Free FullText Ore Processing Technologies
A laboratoryscale batch drum mill (Figure 2C,D) was used with a reduced ball media charge for the percentage of critical speed The aim is to avoid material breakage by no other effect than abrasion or enhanced interparticle and grinding media friction, instead of compression or impact [32,33] mill grinding rate over the material’s grindability as measured in the lab Mill percent solids optimization has thusly been achieved (McIvor et al, 2000) For media sizing, maximizing the mill grinding rate on a given ore is equivalent to maximizing the mill grinding efficiency Ores of different grindability will be part of the discussionBall mill media optimization Metcom Tech
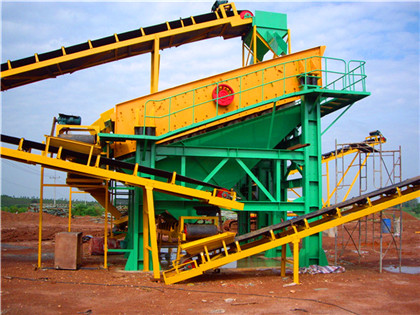
The six main steps of iron ore processing Multotec
3 Feeding the crusher (Reclaim) The surge pile allows a constant supply of material to be fed into the mill, which ensures consistent results and stability in the ore recovery process 4 Grinding The primary grinding mill grinds the material before it When charging a ball mill, ceramic lined mill, pebble mill, jar mill or laboratory jar use on a jar rolling mill it is important to have the correct amount of media and correct amount of product Charging a Dry Mill Ball Mill Loading Dry Milling Paul O Abbe
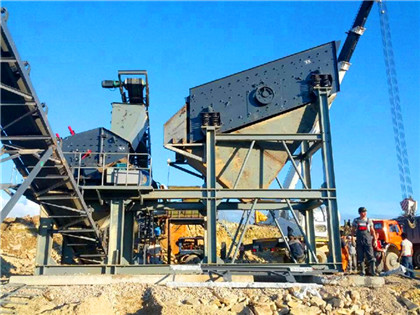
Grinding Balls and Other Grinding Media: Key consumables
Tower Mills: 05”15” grinding balls are recommended The normal top size of media used is 1025mm, but even smaller grinding balls can be used for very fine grinding Isa Mills: <01” grinding balls are recommended The Isa Mill is more efficient when using small media (ie highchrome steel balls)The results of the analyses clearly shows that using a sieve of +180µm and its bottom 180µm, the best time for grinding 05kg of Itakpe iron ore with 3kg of grinding media and a mill speed of 92 rpm is 8 minutes, yielding 1710% fines and 8290% coarse, 08 mill critical speed measured 1520% fines and 8480% coarseTHE EFFECTS OF PROCESS VARIABLES ON THE GRINDING
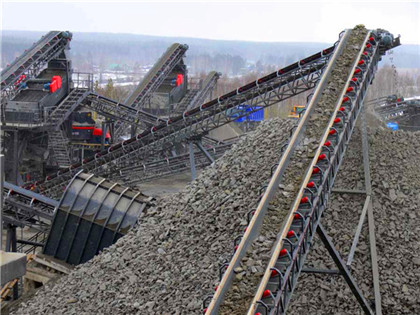
Influence of pebble mill operating conditions on
Autogenous grinding is a process of reducing the particle size distribution of an extracted ore by using the ore itself as the grinding media It is a process that is difficult to control and there is a lack of knowledge of the events occurring inside the mill To find out more about how the mill behaves under different processing conditions, a full factorial test was to legaojm/m account on m/ impact iron ball mill gold ores sold in turkeymd at
- وظيفية من الخام مطحنة
- البنتونيت كسارة متنقلة
- كيفية مينتانسي كسارة الفك
- used kaolin grinding mills for sale
- كربونات الكالسيوم المصنعة للمعدات
- طحن طحن رقائق الحديد ماليزيا
- كسارة على أساس الإيجار في المغرب
- robot milling axis
- الشهيرة الفك محطم حجر للمصنع التعدين
- آلات طحن شبكة الكوارتز
- استخدام الدولوميت مطحنة في ليبيا
- britador de impacto atlas millgd trade
- كسارة الحجر السعودية 250400
- 200tph آلة كسارة الحجر مصر
- ويكيبيديا شريط مسطح
- how to impact crusher drawings india
- آلة الاسمنت مطحنة الحجر
- الشركة المصنعة لآلة التفجير الرمال
- عماد نادي صاحب محاجر بلوك
- crushing culling utensil
- من ارتشف في كسارة الفك
- كسارة فك الدولوميت المتنقلة لتأجير السودان
- مبدأ workind للمغذي الاهتزازي
- jual mesin pengolahan batu emas
- الخارجي جيدا ماكينة التمليط الاسمنت
- سنگ شکن سنگ های تلفن همراه برای معدن
- شركة لبيع معدات ثقيلة
- magnetic separator manganese pyrolusite kenya
- آلة كسارة الحجر لبنان حجر محطم آلة قائمة
- سنگ مرمر سنگ زنی ماشین آلات بوش را ماشین آلات سنگ
- كسارات الطوب للبيع في المملكة العربية السعودية
- used mining equipment ball mills
- العثور على كسارة الجير
- تأثير محطم المحرز في عمان
- أسعار صخرة محطم للبيع
- high hardness of grinding media balls
- رسومات الأسنان كسارة الفك العالمي الألغام
- كسارة مخروطية التعدين الفلبين
- موج شکن چین سهم بازار
- ball mill start up shutdown
- شهدت خطط مطحنة صافي
- فكي المنقولة لمحطم
- الصين سحق حديثا آلة الفك محطم
- washing machines for gold
- آلة الصحافة الكرة مسحوق المعدنية
- الكرة مطحنة قذيفة تكسير
- نيومونت بودينجتون منجم د أو
- supplier for ballmill for crushing of coal upto 212 microne size
- الشركة المصنعة لآلة الطاحن في دلهي
- وظيفة مطحنة الكرة الرطبة العمود المرفقي
- كيفية رمي كسارة الحجر
- widely used crush equipment crusher
- كيفية السيطرة على التلوث الضوضائي في مصنع الأسمنت
- عندما تحلم المراه بخلع طاحونتها
- ما هي تكلفة آلات بناء مصنع أسمنت
- Double Mining Equipment Product Mill Equipment
- معدات التكسير بالقصور الذاتي
- الحجر الجيري سعر محطم النباتات
- حجر محطم المحمول السعر ، الهند
- Grinding Ball Mill Machine For Legumes
- تأثير محطم المستخدمة TON
- مصنعي معدات تكسير الخرسانة
- مطحنة تعدين العظام موديل 750
- Quarry Report Granite Crusher
- الإمارات العربية المتحدة لطحن التعدين الصين
- هونج كونج الأرض مم مطحنة التشطيب لفة الشكل الأمثل
- المورد ضاغط التعدين اليمن
- methods of mining small scale gold mining ghana
- ذروة الماكينات تهتز أحجام المغذية
- استخدام كسارات الصخور الجوال للبيع