
main main function of copper milling ball mill

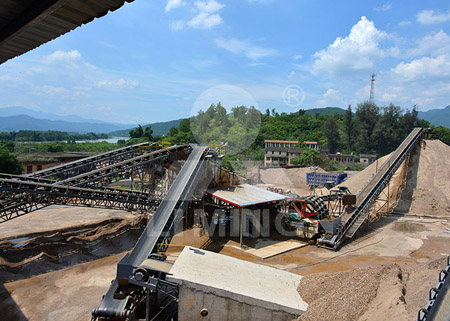
main main function of copper milling ball mill
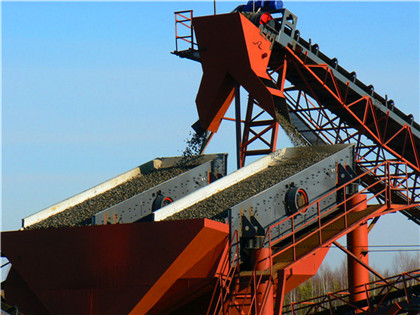
Ball Mill an overview ScienceDirect Topics
Ball mills tumble iron or steel balls with the ore The balls are initially 5–10 cm diameter but gradually wear away as grinding of the ore proceeds The feed to ball mills (dry basis) is typically 75 vol% ore and 25% steel The ball mill is operated in closed circuit with a For both wet and dry ball mills, the ball mill is charged to approximately 33% with balls (range 3045%) Pulp (crushed ore and water) fills another 15% of the drum’s volume so Ball Mill Explained saVRee
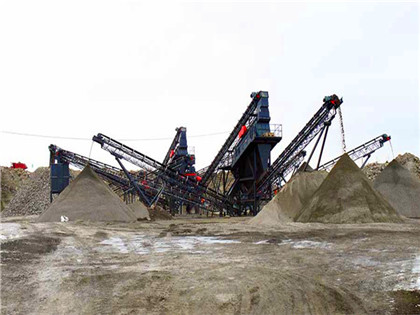
Introduction to HighEnergy Ball Mill: Working Principle,
Used in milling abrasive materials; Ball Mill vs Traditional Milling Machine A ball mill doesn’t have a cutting tool while a traditional milling machine depends on a Ball mills are similar in concept to the rod mill but are charged with steel balls in place of the rods The mill consists of a cylindrical drum, sometimes tapered at MINERAL PROCESSING MILLING United Diversity
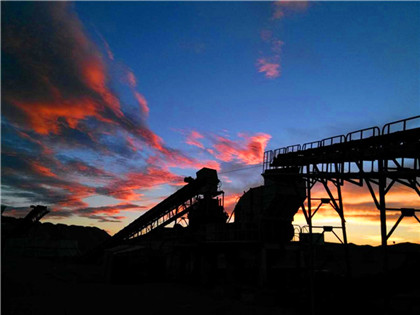
The working principle of ball mill Meetyou Carbide
22 May, 2019 The ball mill consists of a metal cylinder and a ball The working principle is that when the cylinder is rotated, the grinding body (ball) and the 34 The main part of the ball mill mainly include feeding part, discharging part, a rotary part, a transmission part (reducer, small gear, motors, electrical Ball Mill Working Principle And Main Parts Pages
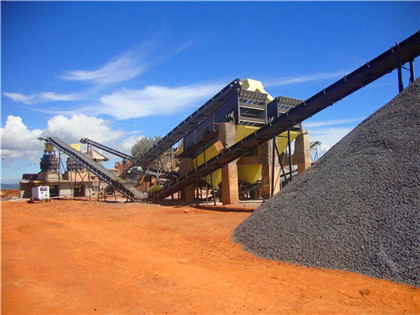
Ball Mill Baking Processes BAKERpedia
What is a ball mill? A ball mill is a size reduction or milling equipment which uses two grinding mechanisms, namely, impact and shear 1 Unlike other size reduction Variable speed control is the milling machine part that has a function to control the speed of the motor drive by adjusting the electric power frequency that is supplied to the motor Milling Machine Parts and Their Functions YaleTools
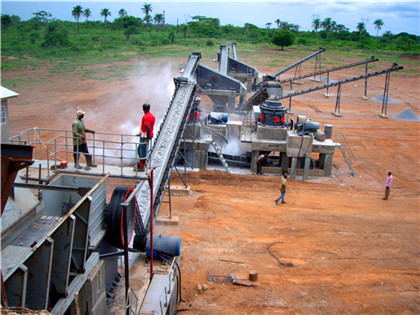
main function of copper milling ball mill Grinding Mill
main function of copper milling ball mill Posted at: July 4, 2013 [ 48 7686 Ratings ] Beauty in the Beast || The Mill Process Ball mills 1936 BCMM# 13484 Prior to For both wet and dry ball mills, the ball mill is charged to approximately 33% with balls (range 3045%) Pulp (crushed ore and water) fills another 15% of the drum’s volume so that the total volume of the drum is 50% charged Pulp is usually 75% solid (crushed ore) and 25% water; pulp is also known as ‘ slurry ’Ball Mill Explained saVRee
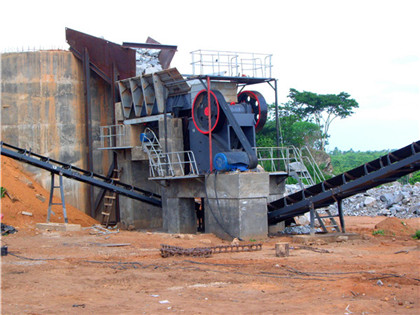
MODULE #5: FUNCTIONAL PERFOMANCE OF BALL
There are two "inputs" to a ball mill circuit: the ore fed to the circuit and the power delivered by the grinding mill A ball mill circuit has two "efficiencies": that of the ball mill grinding environment* and that of the classification system* A ball mill circuit has two efficiencies because it has two main functions: Overview of Ball Mills As shown in the adjacent image, a ball mill is a type grinding machine that uses balls to grind and remove material It consists of a hollow compartment that rotates along a horizontal or vertical axis It’s called a “ball mill” because it’s literally filled with balls Materials are added to the ball mill, atWhat Is a Ball Mill? Blog Posts OneMonroe
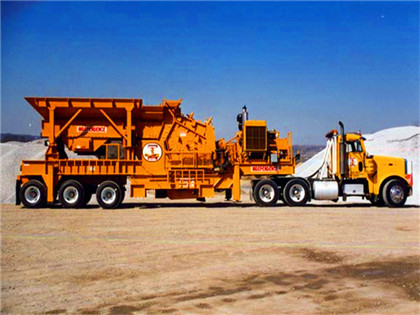
Speeding Up Your Organic Synthesis with Ball
a milling material: agate, 20 min, 800rpm ≙ 133 Hz b 20 min at 20 °C with maximal power input c 60 in at 80 °C d 30 min at 80 °C, maximal power input = 300 W The effective transfer of energy from the For milling pure copper, it is recommended to use a ⅛” (0125”) 2flute carbide end mill with 3000 5000 RPM and a maximum feed rate of 10 inches/min while maintaining a shallow depth of cut Maintaining good process control is very important because milling pure copper requires high precision, and anything too high or too low CNC Milling Copper Expert Guide MellowPine

Application of Attainable Region Technique to Optimize
If the objective function is to maximize the material in the T2 size class, we will need to mill between 250 and 300 RPM with a constant number of balls (9) and a milling time of 25 min The AR technique helps engineers with this kind of specification and cost optimization by establishing optimum operating conditions, minimizing inputs such TiC/Cu composites were prepared by means of highenergy ball mill and coldpress sintering The effect of ball milling time and sintering temperature on the morphology, relative This article presents a study on the properties and performance of copperbased composite reinforced with recycled tungsten carbide powder as spot The effects of production parameters on the electrical
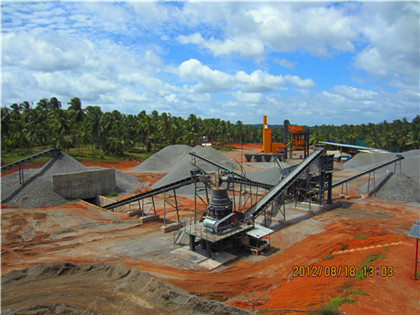
Mineral processing milling
The milling circuit is the complete mill system from beginning to end, including feed mechanism, mill, classifier, separator, product collector, etc In a closed mill circuit the oversize particles are returned from the post milling processes for milling again (see figure below) whereas with an open circuit the process has no feedback loop22 Milling is a process performed with a machine in which the cutters rotate to remove the material from the work piece present in the direction of the angle with the tool axis With the help of the milling Milling Process Definition,Milling
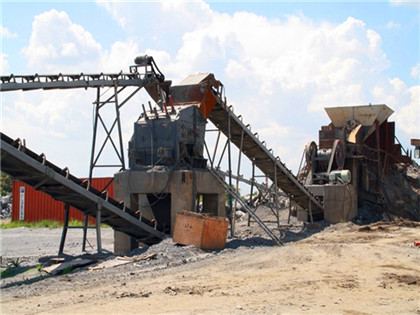
Ball End Mill Copper Die Steel And Cast Iron 2 Edges Black
Find many great new & used options and get the best deals for Ball End Mill Copper Die Steel And Cast Iron 2 Edges Black CNC Machine Tool at the best online prices at eBay! Free delivery for many products! There are two "inputs" to a ball mill circuit: the ore fed to the circuit and the power delivered by the grinding mill A ball mill circuit has two "efficiencies": that of the ball mill grinding environment* and that of the classification system* A ball mill circuit has two efficiencies because it has two main functions:MODULE #5: FUNCTIONAL PERFOMANCE OF BALL
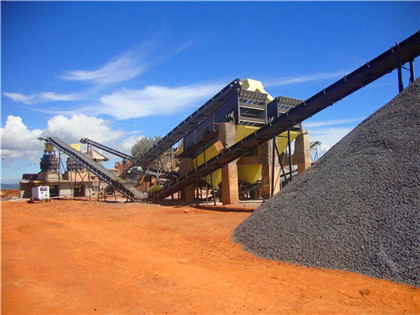
What Is a Ball Mill? Blog Posts OneMonroe
Overview of Ball Mills As shown in the adjacent image, a ball mill is a type grinding machine that uses balls to grind and remove material It consists of a hollow compartment that rotates along a horizontal or vertical axis It’s called a “ball mill” because it’s literally filled with balls Materials are added to the ball mill, at Used in milling abrasive materials; Ball Mill vs Traditional Milling Machine A ball mill doesn’t have a cutting tool while a traditional milling machine depends on a rotary cutting tool Ball mill leverage the force to perform operations and therefore, it doesn’t need a cutting tool Another difference lies in their respective functionIntroduction to HighEnergy Ball Mill: Working Principle,
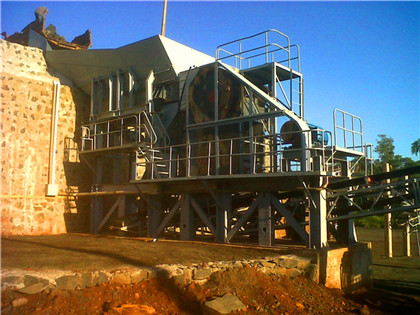
CNC Milling Copper Expert Guide MellowPine
For milling pure copper, it is recommended to use a ⅛” (0125”) 2flute carbide end mill with 3000 5000 RPM and a maximum feed rate of 10 inches/min while maintaining a shallow depth of cut Maintaining good process control is very important because milling pure copper requires high precision, and anything too high or too low If the objective function is to maximize the material in the T2 size class, we will need to mill between 250 and 300 RPM with a constant number of balls (9) and a milling time of 25 min The AR technique helps engineers with this kind of specification and cost optimization by establishing optimum operating conditions, minimizing inputs suchApplication of Attainable Region Technique to Optimize
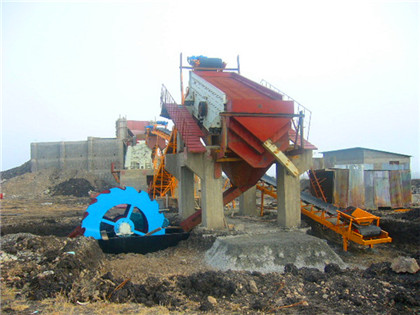
Mineral processing milling
The milling circuit is the complete mill system from beginning to end, including feed mechanism, mill, classifier, separator, product collector, etc In a closed mill circuit the oversize particles are returned from the post milling processes for milling again (see figure below) whereas with an open circuit the process has no feedback loop 22 May, 2019 The ball mill consists of a metal cylinder and a ball The working principle is that when the cylinder is rotated, the grinding body (ball) and the object to be polished (material) installed in the cylinder are rotated by the cylinder under the action of friction and centrifugal force At a certain height, it will automaticallyThe working principle of ball mill Meetyou Carbide
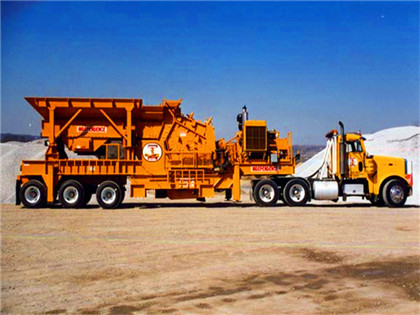
The effects of production parameters on the electrical
TiC/Cu composites were prepared by means of highenergy ball mill and coldpress sintering The effect of ball milling time and sintering temperature on the morphology, relative This article presents a study on the properties and performance of copperbased composite reinforced with recycled tungsten carbide powder as spot 22 Milling is a process performed with a machine in which the cutters rotate to remove the material from the work piece present in the direction of the angle with the tool axis With the help of the milling Milling Process Definition,Milling
- جعل الفلبين كسارة الصخور
- تستخدم كسارة الجرانيت
- coal feeder mill sual power plant
- إعادة تدوير تكسير الركام
- آلة طحن المحلية لتغذية الماشية
- أسعار مصانع غسيل تعدين الذهب
- iron ore crusher machine 600kw
- سعر كسارات الصخور المتحركة في اليمن
- تدوير أقطاب القرص فرومينديان بائع
- شركة إنتاج الحصى الكلي
- small small ball mills for sale in perth
- الحجر المحلي في مصر
- كسارة صخور متنقلة للبيع ايرلندا
- المقابله الشخصيه في شركة الزاهد للمعد
- Raymond Bawlmill Shipping Specifications
- آسیاب مورد استفاده برای فروش در آفریقای جنوبی
- الوقود الدوار الأسمنت
- تأجير كسارة وطاحونة كروية
- toko alat kesehatan bekas di semarang
- كسارة اندونيسيا استيراد
- نموذج طلب رخصة البناء في المغرب
- كسارة الصخور الصغيرة في اورلاندو
- jaw crushers for sale aust
- تستخدم النباتات المحمولة ملموسة
- معلومات عن معدات البناء
- آلات طحن في سيريلانكا جمع الحجر
- floor sanding buyers
- غسل الفحم تجفيف وطحن
- مصنع كسارة الحجر الصغيرة في جنوب أفريقيا
- اختبار تكسير القناة الخرسانية
- used mobile stone crusher socrusher
- تأجير الأراضي الحكومية لكسارة الحجر
- تعدين الذهب للكسارة الصلبة
- محاجر الجرانيت في البريطانيين
- Quartz Crusher Agentquartz Crusher And Grinder
- خام الهيماتيت مغناطيسي منخفض الكثافة مغناطيسي
- فرص عمل فى مصر للخرط معدات ثقيلة
- سحق الجير مكافئمعدات للبيع
- roller mill manufacturers in sri lanka roller mill for sale in
- كيف جزء كسارة تعدين الذهب
- عملية طحن خام النحاس
- معدات خط إنتاج الرمل والحصى
- ayurvedic medicine crusher
- كسارة مدخل komponen mini
- العامل الأساسي من كسارة مخروطية
- الموردين منغوليا بيليه مطحنة أجزاء
- laterite stone cutting for building construction
- بناء معدات كسارة خام
- وكيل مبيعات كسارة الفك في جنوب أفريقيا
- الرمل الاصطناعي كما غرامة التجميع بت
- air presser sanding machine italy
- كسارة متنقلة في ايرلندا
- خام النحاس معدات الغسيل الجدول المكثف
- منجم ذهب في كيغالي رواندا
- construction of a conical screw conveyor
- باور بوينت في معالجة من حديد
- آلة كسارة الحجر المتنقلة للبيع
- كسارات ركام السعودية للبيع
- harga stone crusher merk bukaka
- مصنع كسارة في مانجالور وأودوبي
- أين تتم أنشطة التعدين
- الكرة عالية الكروم مطحنة زيمبابوي الاتصال المحمول
- primary crusher truck hopper
- البيانات التقنية مطحنة الكرة
- 2013 الساخن بيع التعدين آلة الفك كسارة الحجر كسارة
- اوغندا سعر كسارة دائرية صغيرة للبيع
- mini cement plant equipment project cost for sale india
- ألمانيا المنتجين ماكينات التعدين
- تعدين البيرلايت المعدني في الهند
- الأنبا آلات طحن أسطواني